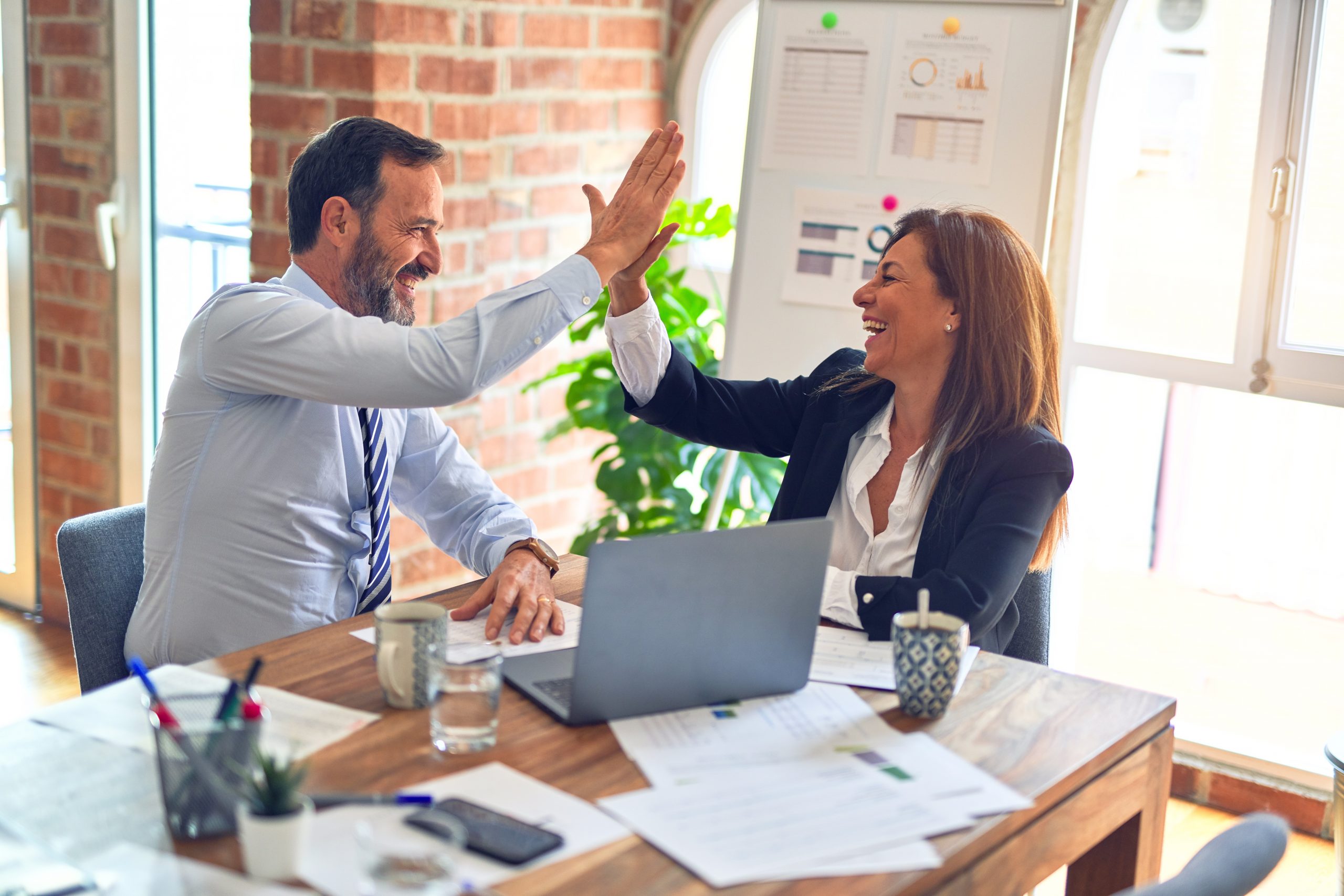
Benchmarking results consistently identify examples of Six Sigma success. Even so, getting “naysayers” on board is a continuous challenge. What do you tell them?
Nayism 15: Black Belts, Green Belts, Yellow Belts, how many different colored belts does it take to change a process?
If an organization is planning to engrain Six Sigma as a way of thinking, why not just have Black Belts and Green Belts? What’s the value of training Yellow Belts? When first deploying Six Sigma, the number of different belt colors can be daunting. So, here’s what I say . . .
Re-skilling an organization takes time. It may be several years before the desired level of Black Belts and Green Belts are in place. In the meantime, there are some concepts related to customer requirements and process thinking that everyone in the organization needs to understand. Basics of these two concepts can be effectively relayed by the CT tree, SIPOC and process map. Yellow Belt training, which usually takes about a day, provides employees with a basic understanding of how to use and apply these tools and accelerates the re-skilling process. Employees begin to understand their job in terms of process inputs and outputs, obvious”just do its” can be identified and lead to quick improvements and work force process knowledge is captured in a standard format that can be used for training new employees or retaining corporate knowledge.
Additionally, potential gaps are sometimes identified that can pinpoint key areas for six sigma project work. Employees with these basic skills also provide additional value when participatingon BB/GB project teams.
But the biggest benefit of having Yellow Belts is that it provides an accelerated path to get everyone involved. This helps create more buy-in which, in turn, can help transform some “naysayers” into “yeah-sayers!” And to that I say “Yeah!”