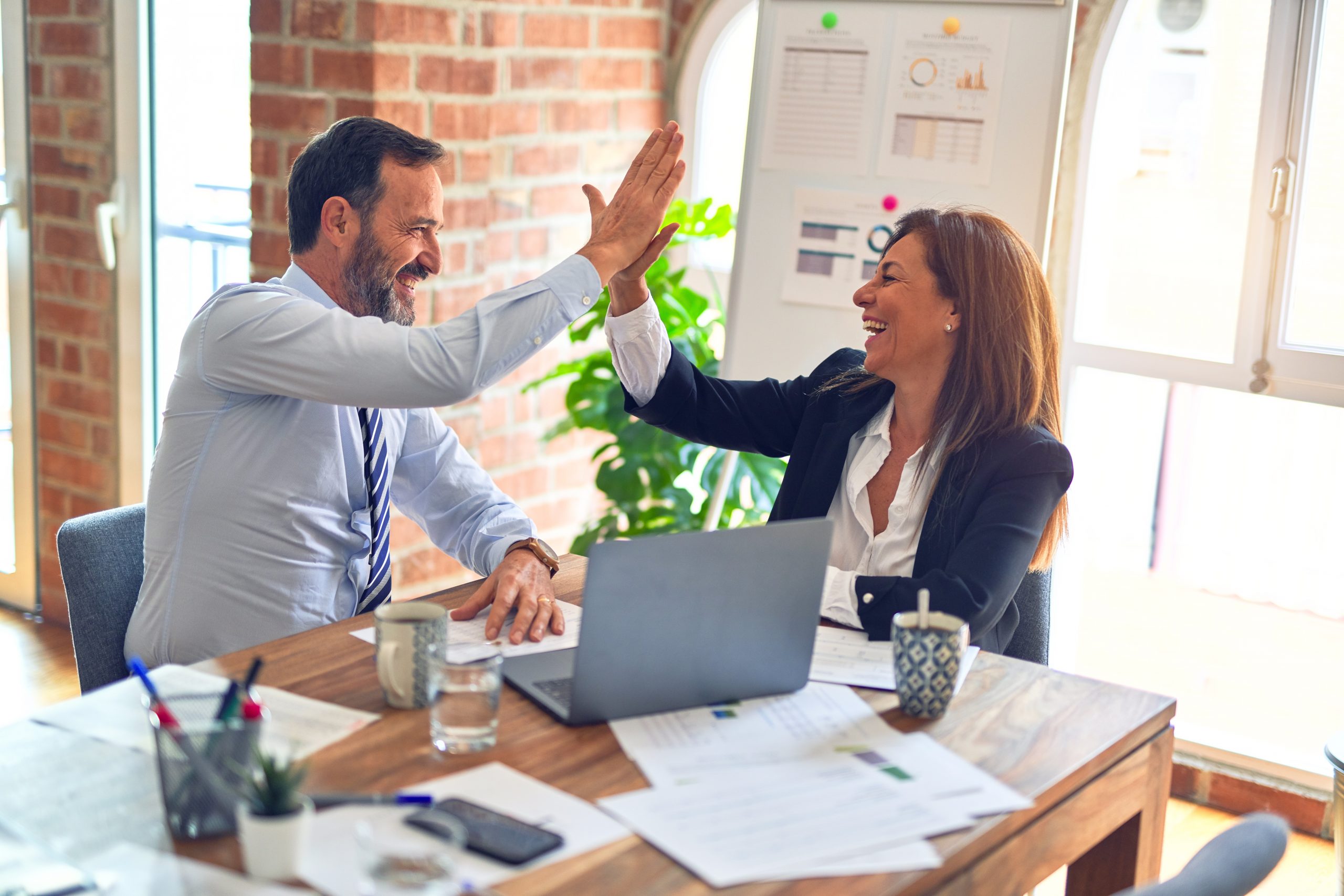
As expressed in my first blog, learning and practicing Lean Six Sigma helps me communicate with more clarity and consistency. In my opinion, one of the barriers to continuous improvement is the use of words without clearly defined and mutually agreed upon meanings. It’s common to see project charters include vague statements like these:
- improve efficiency (or productivity)
- create a more flexible process
- reduce defects/errors
- improve customer satisfaction
- reduce cycle time
W. Edwards Deming devoted an entire chapter to Operational Definitions in this book Out of the Crisis. He pointed out “Adjectives like good, reliable, uniform, round, tired, safe, unsafe, unemployed have no communicable meaning until they are expressed in operational terms of sampling, test, and criteria.”
In our Lean Six Sigma training, we have learned to use the SMART goal statement to be Specific, Measurable, Achievable, Relevant and Time-bound. It certainly has helped. However, even a SMARTer goal statement, such as “To reduce the time from order to delivery for part #123 from 12 days to 5 days by October 2010,” still requires further clarification regarding “sampling, test and criteria.” For example,
- What defines the order event or delivery?
- How is the time measured, and by whom?
- Is the time in business days or calendar days?
- Is the 12 days or 5 days the average or maximum?
- Does the time variation matter?
- What is the sample size required to determine if the goal is achieved?
- Does October 2010 mark the start or the end of the Control phase? Is process stability required by October 2010?
One reason for unclear goals or metrics lies in the lack of understanding of statistical concepts such as variation, sampling, and process stability. Unless people understand how a measured characteristic depends on the measurement method or the difference between special cause and common cause variations, they will not recognize that the goal or metric is unclear.
A Six Sigma framework, such as DMAIC, forces us to pay careful attention to the definition of Critical-to-Quality characteristics (CTQs), Performance Standards (defect definitions), Data Collection Plan, and Measurement System Analysis. The Define and Measure phases are particularly important in defining the right problem to solve and setting a SMART goal.
So the next time you review someone’s charter, ask similar questions.
Do you have any examples of unclear goal statements or metrics to share? What did you learn and how did you improve them?