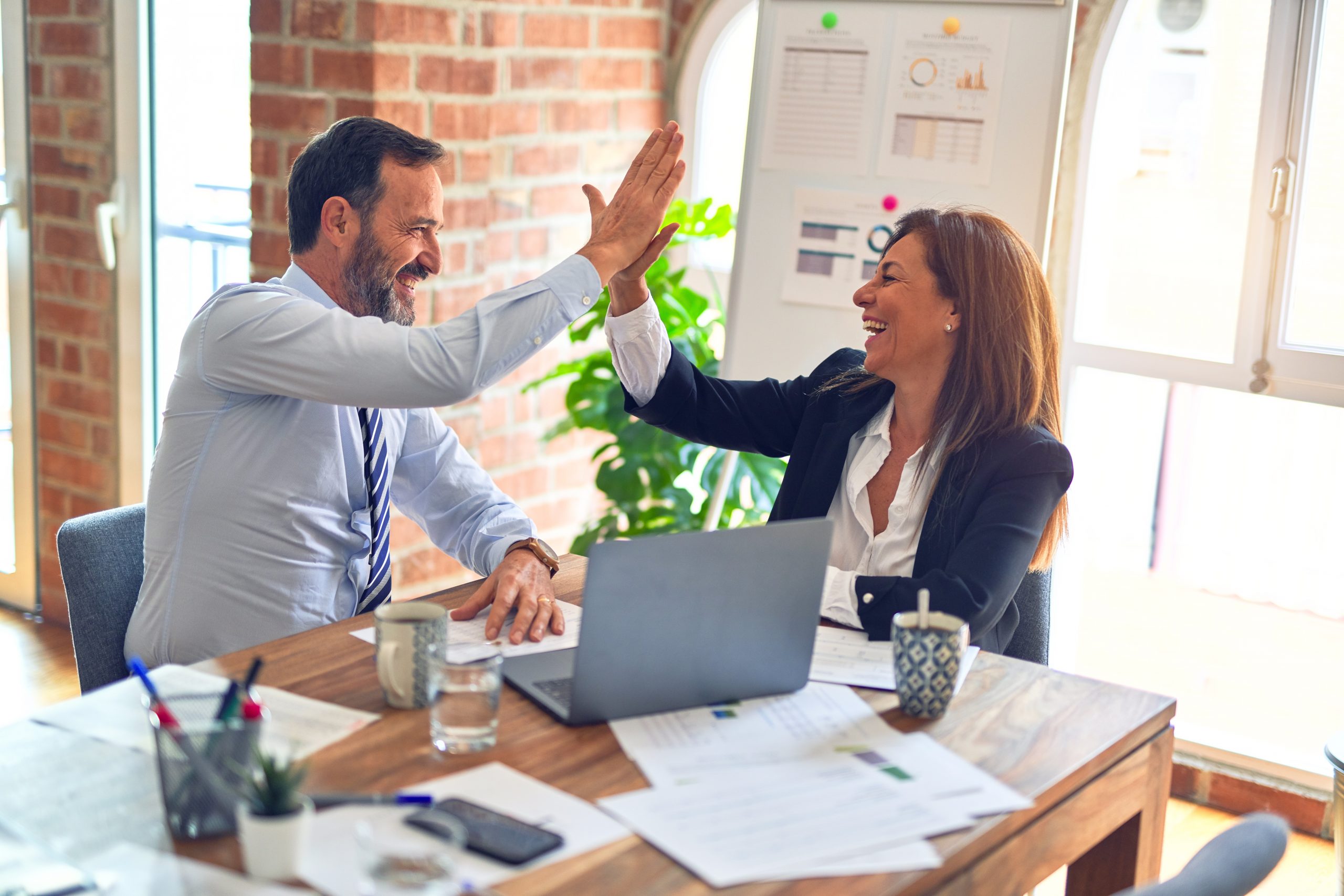
DMAIC is a very powerful method and provides a framework for leading business improvement projects. The consistent rigor has led to many great results. However, I have also seen less successful DMAIC projects that took too long and/or generated little improvement.
As mentors, we all have seen inexperienced belts struggle with various tools. However, my experience shows that many projects fail to achieve desired results not because of incorrect or insufficient use of tools, but rather the use of DMAIC itself. As some skeptics have argued, DMAIC is not the best or only approach to process improvement. There are different and/or simpler ways of improving what we do. Deciding on when to use the full DMAIC method requires some experience and judgment.
What has worked for me is to assume that DMAIC is the right approach first, and then look for signals that help me decide whether to continue on the DMAIC path. The beauty of the DMAIC method is that it allows me to see these signals early in the Define and Measure phases. The following are a few examples.
-
The sponsor or customer requests a specific solution. This is a case where understanding the root cause of a problem is less important to the business or customer. It’s OK to skip Measure and Analyze and just do it ASAP. Make sure the Control phase elements are in place to verify the effectiveness of the solution.
-
The process was never designed to deliver the specific product or service. It can be very confusing to a team as to why we need DMAIC when the root cause of the problem is so obvious. A Lean or Design for Six Sigma approach would be more effective in understanding and meeting the need.
-
Cost reduction is the only goal/metric. Cost saving or process efficiency is often a result of many Lean Six Sigma projects. However, unless there is another metric, such as quality or lead time, that links to customer value, cost itself rarely provides the focus needed in a DMAIC improvement project. Use Lean and Kaizen instead.
-
The process is undefined or chaotic. It’s hard to improve a process if we don’t know what it’s supposed to do. It’s not uncommon to see DMAIC projects fail to show improvement because the baseline was never clear. Define, standardize and stabilize a process before trying to improve it. Lean and statistical process control tools can be used without a full DMAIC project.
-
Process data are not sufficient. One challenge in a non-manufacturing environment is that quality data is scarce. People simply never thought of measuring processes or collecting data. Measurement systems typically do not even exist. The quality of DMAIC improvement is only as good as the data we have. So start from defining CTQs, and develop measurement systems to understand the process capability before staring a DMAIC project.
Continuous improvement is not about projects, DMAIC or otherwise. In any case, concepts and tools used in DMAIC can and should be applied when appropriate.
I am sure many of you have similar and/or different criteria in choosing a full DMAIC, an alternative, or some hybrid approach. I would like learn about your experience and lessons in choosing the right method in your continuous improvement effort.