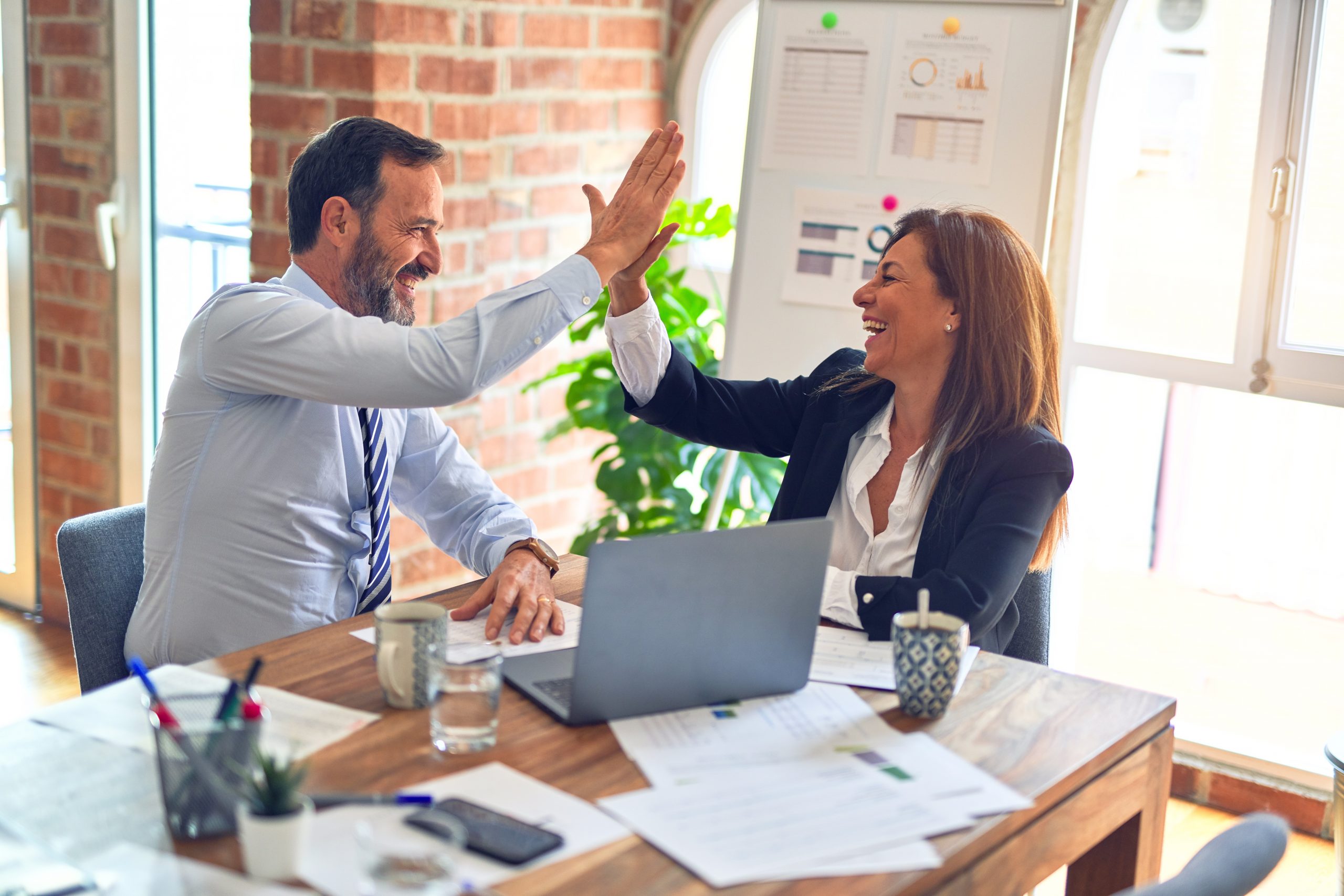
Perhaps you all arrived at this conclusion way ahead of me, but I’m starting to worry more and more about the way we, as continuous improvement professionals, are spending our time.
It’s becoming increasingly clear that the world in general, and the economy in particular, has gone off meds. Yes, I know, this isn’t news at this point. But lest you think I’m the last one to get the message, seek out the open letter that John Stumpf, The CEO of Wells Fargo, recently placed in the New York Times and elsewhere. He was explaining his view on “the value of team member recognition”…which apparently boils down to paid travel to fun places in his mind. Clearly there’s at least one other person slower on the uptake than me.
The press has been all over this letter, including this piece by Maureen Dowd. I don’t have anything to say about it that hasn’t already been said by smarter people. But it does highlight that there is a true shift going on out there. What used to be reasonable, even commendable, has become detestable.
Deming exhorts me to create constancy of purpose, and Wheeler explains to me why reacting to random variation is a bad thing. I feel I have both and intuitive and statistical understanding of “special cause”, and I try to apply that understanding to the work in front of me. Usually that means resisting the tendency to chase special causes in favor of common cause work, and for a long time I have been confident that was the right thing to do.
But now? A lot of things are changing. Those changes feel drastic. Is it time to react in a special way? Or is this just fluctuation of the larger system? Do we keep running our Six Sigma programs, Lean initiatives, and Quality Management systems and wait it out? Or has the time come to move on to changes and initiatives that are more radical and sweeping? More special? Deming does advocate constancy of purpose, but in the next breath he points out the need to adopt a new philosophy for a new economic age. Which advice applies now? What would Deming do?
Let me offer a few more things to think on to frame this question. Continuous improvement programs usually rely on projects as units of work. Using various toolsets, each project is able to return more value to the organization than they consume in money and resources. Group a bunch of these projects together, add up the saving, and you have a program.
Successful programs might generate 5% productivity each year. In other words, if we do things right, we might produce 105% of what we produced last year for the same amount of money. Or maybe we produce the same amount for 95% of the cost. You get the idea. For the past several years, maintaining that sort of incremental improvement in consecutive years was a great result.
But now? Your sales are down 80%. Your raw material cost are up 150%. You can’t spend $100,000 even for a guaranteed return of $125,000 because credit is frozen. Double digit percentage layoffs abound. In this environment, that ongoing 5% productivity that was great a few years ago is less than a rounding error compared to the huge swings that are happening largely outside our control.
Take Wiremold as a cautionary example. If you are reading this blog, there’s a good chance you already know something about this company from Womak and Jones’ book “Lean Thinking.”
Great company, hugely strong in Lean, right? Well, read this. Sure, there were clearly other factors involved, and maybe their commitment to Lean isn’t as strong as back in the day. But anyway you slice it, this is a titan in the continuous improvement world staggering from a serious blow. Lean can’t help if there is no demand. You can’t save your way to top line growth. It doesn’t matter how efficient you are if no one has money to buy what you are selling.
I think we at least need to ponder whether anything that we are doing matters at this point. Whether we are maybe even part of the problem. It’s easy to spank Wall Street CEOs as they assume the position in front of Congress, but are we just as guilty of failing to confront a new reality?