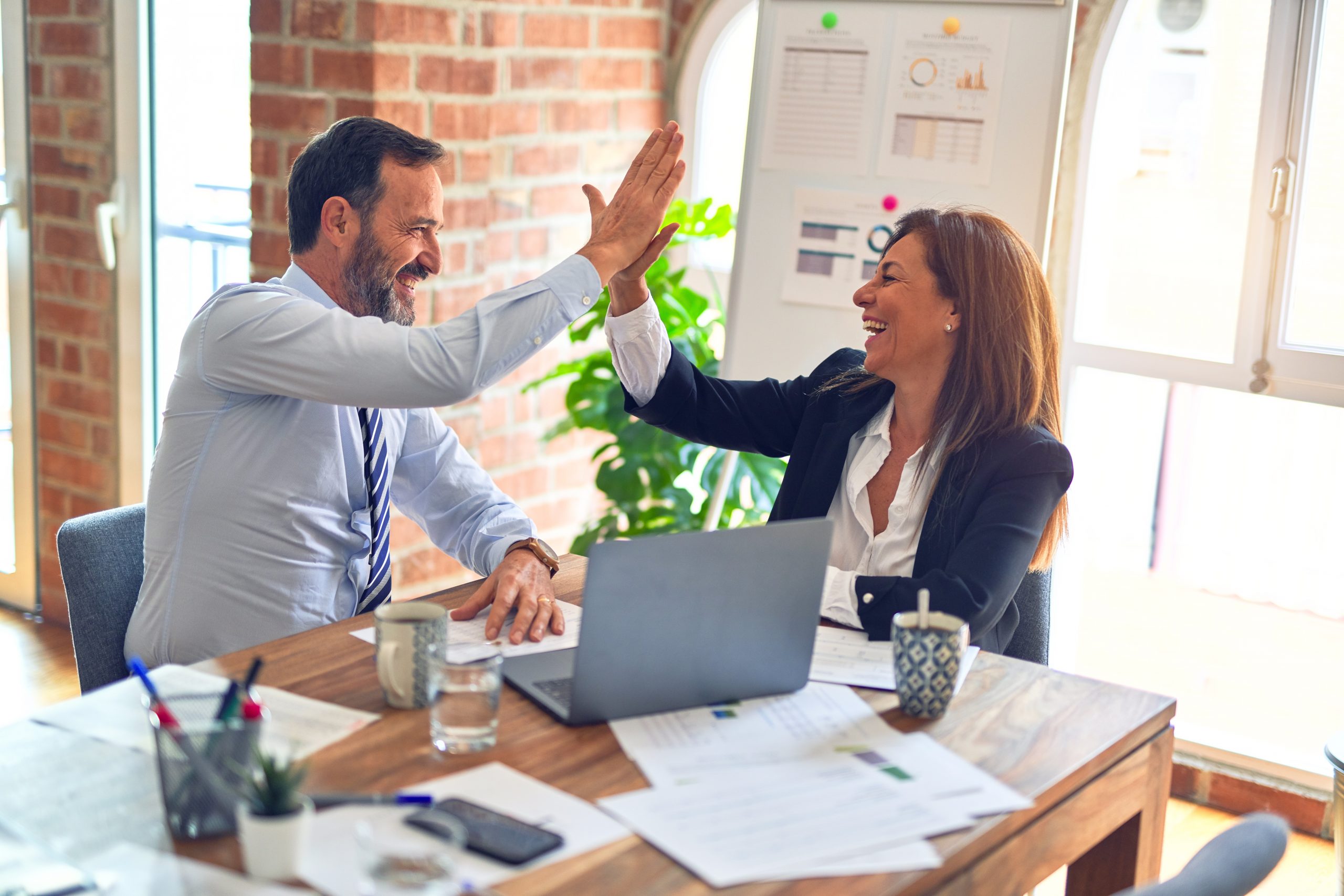
A conversation I regularly get into involves discussion of the difficulties encountered when deploying Six Sigma in an environment that is already saturated with other programs and toolsets. A majority percentage of the time the discussion is about deploying Six Sigma in an area where Lean is already well established, but there are many other variations out there.
Certainly it is possible to create conditions where Six Sigma plays nicely with other disciplines. First order combinations like Lean Sigma and its many variants are an example of this. So are higher order hybrids, like Design for Lean Six Sigma Using Triz. And from an intellectual perspective, there is a lot of appeal to this approach. If you think about it hard enough, there are significant synergies to be explored and interesting combinations to be leveraged.
But from a practical perspective, I’m not so sure. For my money, a significant amount of the value of a program like Six Sigma comes from its ability to function as an organizing concept. It gives the organization something to rally around. It crystallizes diverse thoughts and aligns what might otherwise be diverse efforts as improvement. Six Sigma has value simply as an excuse to get everyone thinking about problems in the same way. Diverse groups come together through training programs to have prolonged discussions about approaches to problem solving. Results (and lack thereof) start to get visibility. Executives take an interest. People on the shop floor get involved. Everyone goes on the journey together. Even if you don’t think that the content of Six Sigma is useful, the cohesion of thought and action it produces clearly has value.
The thing is, this is true of almost any program properly deployed. Lean will certainly do it. Numerous safety programs do it. Good business transformation initiatives do it. Implementation of major systems like SAP or Oracle do it. Assuming you can execute, the one thing you need to get this sort of benefit is a simple, compelling organizing concept. Or to put it more colloquially, you need an approach. The simpler and more persuasive, the better.
If you buy this line of thinking – that a large part of the value of any particular organizational program lies in the fact that it is a program at all, not in its content – then the question of how to deploy multiple overlapping programs becomes easy to answer. Don’t do it. If you already have an organization succeeding with Lean, don’t mess with it by deploying Six Sigma on top. You’ve got your organizing concept. Adding another program on top (or even worse, visibly switching to the new program from the old one) can do nothing but detract from that focus. Simpler is better in terms of rallying a group around a way of thinking, even if there really are synergies to be explored through more complicated approaches.
Don’t get me wrong – I’m not suggesting that new toolsets and approaches shouldn’t be added in over time, and that new techniques shouldn’t constantly be considered. But I am suggesting that moving too far away from an organizing concept that is already working well is a mistake to be avoided.