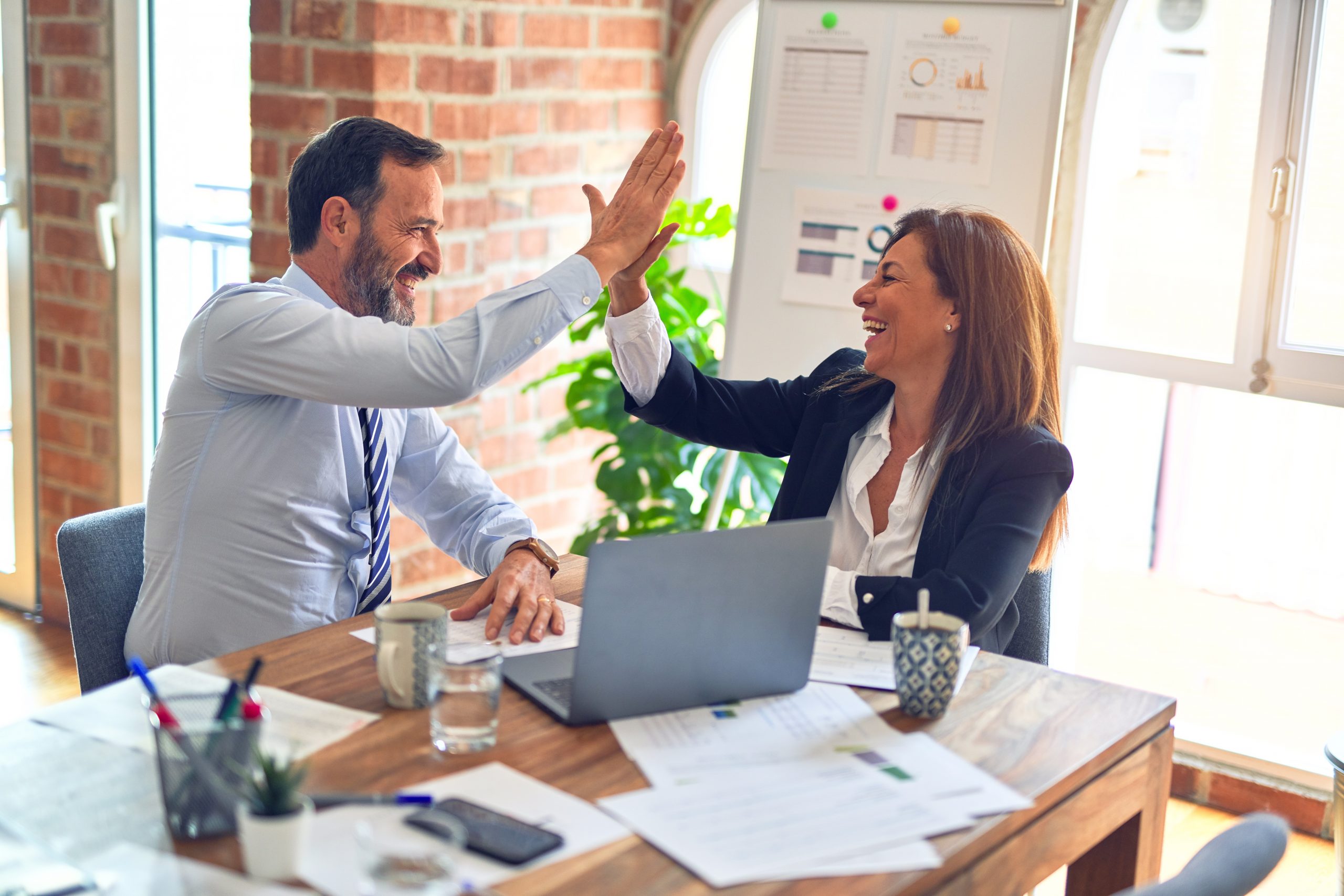
Over the past weeks and months I have become increasingly aware that there is a grouchy counter-Six Sigma-culture out there. As indisputable proof of this, a Google search on the phrase “Six Sigma sucks” returns no less than 111,000 hits. (See for yourself here.) Even discounting bitter G.I. Joe fans, this is a big number.
I certainly didn’t read through all of the links, but I did peruse the first score or so. And I also spent quite a bit of time reading through the collected wisdom on a page ostensibly devoted to “The Truth about Six Sigma Quality…Fallacies, Faults and Errors” located here. Incidentally, I was directed to this site from, of all places, the forums on www.isixsigma.com.
Because there is a lot to read on the subject of “Six Sigma Sucks”, allow me to paraphrase the vast majority of what is out there in the three points below. And, of course, to respond. Because behind the smarmy smarter-than-thou attitude that pervades most of these pieces, there is little more than a lot of unfounded assumptions, much plain misunderstanding, and no small measure of grumpy complaining masquerading as fact.
1. The math is wrong.
There seems to be a small but dedicated community of folks (mostly academics and consultants) who are obsessed with some or all of the following: the definition of defects; the focus on defect reduction; use of Sigma as a process measure; usefulness of DPMO as a process metric; whether using the normal curve as a basis for process improvement work is appropriate; whether Harry’s “1.5 sigma shift” is real and if so how it may be explained; whether Six Sigma is a reasonable goal in the first place; etc, etc, etc.
Such arguments, in my opinion, entirely miss the point regarding data-driven continuous improvement. Sure, math and statistics get tortured and misused all the time in the name of Six Sigma. And sure, errors are made. That’s not surprising – a few weeks of training and access to a lot of computing power does not make people into statisticians or mathematicians. But if we can get to the point of discussing and debating the problems and opportunities in an organization in a data-driven, consistent way, then the battle is already won. We don’t have to be right in every case, or even most cases, to make progress. Dwelling on the fact that the math is sometimes wrong is a bit like suggesting that we should never start jogging to lose a few pounds unless our running technique is already perfect. In fact, we make a lot of progress even if our technique is terrible. And not to start at all would be a much worse mistake than starting poorly.
Furthermore, “the math is wrong” is not only a weak argument, but also one aimed against a view long since discarded by most serious practitioners of continuous improvement. In my opinion and experience, the best Six Sigma programs today no longer focus on simple defect reduction. Many don’t even teach Z-scores or process capability indices. As the detractors are fond of pointing out, gurus like Deming, Shewhart, Wheeler, and many others have much more sophisticated and nuanced views than simple “Six Sigma quality” on the use of statistics to drive continuous improvement. What the detractors don’t seem to realize is that Six Sigma practitioners realize this too. We’re not dumb or close-minded. We all continue to learn, and Six Sigma curricula have largely moved on in their own cumbersome, evolutionary fashion.
2. Consultants vastly overstate the value of the program.
This one, of course, is often true. But it’s definitely not a Six Sigma-specific problem. And it’s not done by good consultants, consultants who understand the plusses and minuses of Six Sigma, and are careful to talk clients through both. There will always be examples of very expensive programs that start with a blizzard of flashy PowerPoint and end with no results, but that’s hardly the fault of Six Sigma in general. Where and when it happens, it happens independent of the program or subject matter. “Caveat emptor” always applies to any consultant services, and “garbage in, garbage out” always applies to any program or initiative. Six Sigma isn’t any different, but that’s hardly a serious knock against the subject matter.
3. Six Sigma isn’t anything new – [insert your favorite author here] had it right way back when they wrote [insert your favorite book here].
Well of course they did. You won’t find a bigger fan of Deming than me. And Shewhart was absolutely a genius. Every book that Wheeler has written has provided me with numerous light-through-the-clouds moments. Tufte is beyond elegant in his views on the graphical display of information. And yet Deming’s 14 points and PDCA methodology still aren’t common vernacular. The vast majority of people using Shewhart’s control charts still don’t understand them. Wheeler’s intuitive and eminently comprehensible explanations of basic statistics still get misunderstood regularly. And to what I can only assume is Tufte’s ongoing dismay, three-dimensionally rendered bar graphs showing one variable are more common than ever. So apparently just being right isn’t enough. We need a way to institutionalize those realizations across large organizations, a way to create a common vocabulary, a way to get everyone a company moving in the same direction. We need an excuse for everyone to read the magic book. And like it or not, programs that generate hype provide a means to those ends. If there’s a better, more efficient way to achieve the same cultural results, I haven’t found it yet.
What bothers me most about the various “Six Sigma Sucks” pieces I read is that their authors inevitably imbue their words with a certain the-Emperor-has-no-clothes self-heroism, subtly suggesting that they are cleverer than we Six Sigma lemmings who run blindly towards the sea. But what they fail to realize is that those of us on the inside are thinking about the same things they are, wrestling with the same issues, lying awake at night wondering how best to evolve Six Sigma going forward. We understand and worry over the shortcomings of the program more than anyone. The only difference is that we don’t let it stop us from doing the best work we can right now, even as we seek better ways.