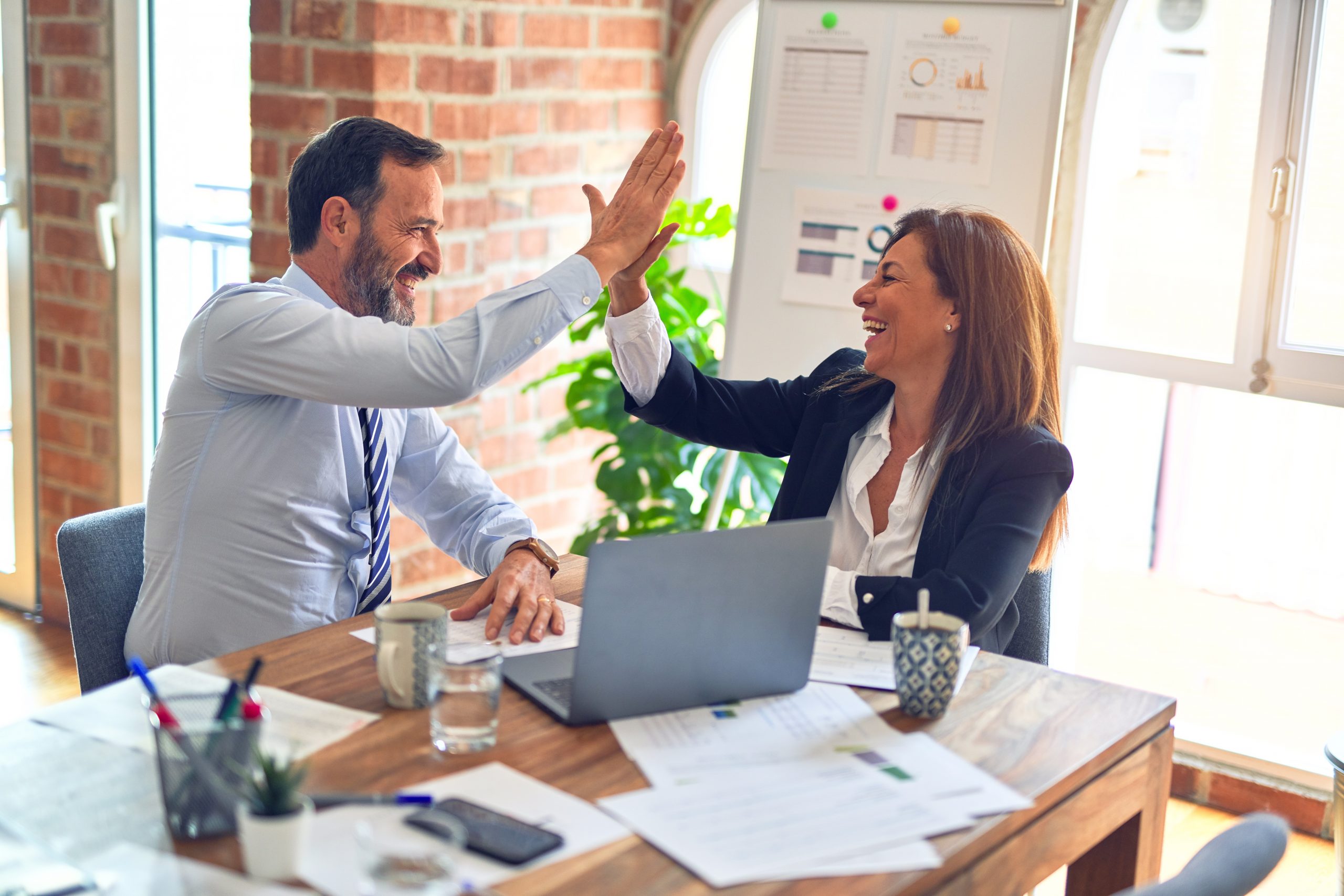
How’s your Lean initiative doing? Is it going great? Or is it starting to lose steam? Or is it clearly failing to meet expectations? Have you given up and gone back to the not-so “good old days” from which you had hoped to escape? These are questions I see a lot of firms both asking and answering in recent times. Unfortunately, all too often the responses are negative.
I am both distressed and disappointed by these responses, but not surprised. I am distressed because Lean Manufacturing is a proven, practical, culture-changing methodology which can launch a firm to new levels of competitiveness and security. It works in repetitive as well as job shop environments, and it can work in the service sector as well as manufacturing. I am largely disappointed because regression in Lean success is both unnecessary and avoidable.
In this article, and four subsequent articles, I will address this challenge of avoiding the regression of benefits that were once achieved. In essence, the issue is: How to sustain the gains from Lean? The solution: It can be done using the tools of cultural change.
How Many Lean Users Fail?
Although Toyota and a few other recognizable companies have mastered Lean, the skills it takes to implement this methodology remain a mystery to some. So what’s the mystery that some have unraveled, yet others miss completely?
Fueled by this question, I churned through my records and reviewed 17 of my clients from the last 20 years, and categorized their efforts. Of the 17, four were clear successes. They were still very profitable, growing and expanding their Lean manufacturing system five years or more after implementing Lean as a manufacturing philosophy. Another two were successful so far, but they were less than five years into their effort, so the jury is still out. Five others were performing below expectations, but still engaged and trying. And six were clear failures with little progress and were either giving up on Lean or had already given up. So my data shows a majority (65 percent) underperforming; specifically 29 percent were performing below expectation and 35 percent were clear failures. It also shows that 35 percent are successful so far or a clear success.
I began studying the Toyota Production System more than 35 years ago; I find no fundamental weaknesses in it or the Lean methodology. However, it appears that a significant percentage of the efforts fail – partly or totally. In fact, for the six initiatives previously mentioned as clear failures, there were two common failings. First, none of the six wished to perform a serious external review of their competitive position. The management uniformly viewed their company in a much more positive light than those outside the company. They were able to focus intently on their company’s strengths and minimize obvious weaknesses as if they did not exist. Second, in each of the six initiatives the facility manager tried to delegate the leadership of the initiative. Actually, the manager did nothing more than assign the implementation task to a subordinate – and in four cases the subordinate was not even a direct report but rather an engineer/manager at least two organizational levels below the facility manager. This guaranteed that the person named as the Lean implementation leader was virtually powerless to implement the initiative.
How to Stay Strong?
Even with a good start, Lean initiatives can falter after some time. It is rare that one does not lose steam as it progresses to maturity. Almost always this regression is due to either misapplying or only partially applying key cultural principles necessary to have a successful culture-changing event. It makes no difference what a culture-changing event is called – be it Lean, TQM or Six Sigma – there are some principles, which if ignored or misapplied, will ultimately cause the effort to either partially or totally fail.
So how can organizations avoid this flagging over time? The general answer is not too difficult. They need to formally and functionally inculcate the new behaviors into their culture. They need to sustain the newly learned behaviors so they become “just how we do things around here.”
There are four cultural principles that allow organizations to sustain those changes. These four principles address: an organization’s purpose, its leadership, how it treats its people and how the organization views continuous improvement. Stated in question format, they are:
- Do you have a clear statement of purpose for the business?
- Do you have Lean leadership?
- Is your business philosophy based on respect for people?
- Do you have a real, functioning continuous improvement process?
Many people read this list and say, “Of course, we have addressed all four.” But I want to caution you. First, did you do a good job to begin with? For example, consider Lean leadership. Did you do a good job distinguishing Lean leadership from Lean management? Can your Lean leadership provide creative tension without providing undue stress? And just how deep is your continuous improvement effort? Are you really improving or just fixing the same old problems again? Are you ready, willing and able to stress your system until it breaks? If not then you really don’t have a continuous improvement philosophy.
These are just some of the questions this article series will explore. Even if your organization addressed these questions well from the get-go and is still making good progress, you might need to review and make some minor corrections. And to those who are not making good progress, maybe your organization did not do such a thorough job of evaluating these principles as you might have thought.
Stay tuned to learn how to assess and adjust your organization’s culture so that you have a culture that is more capable of sustaining the gains you have worked hard to achieve.