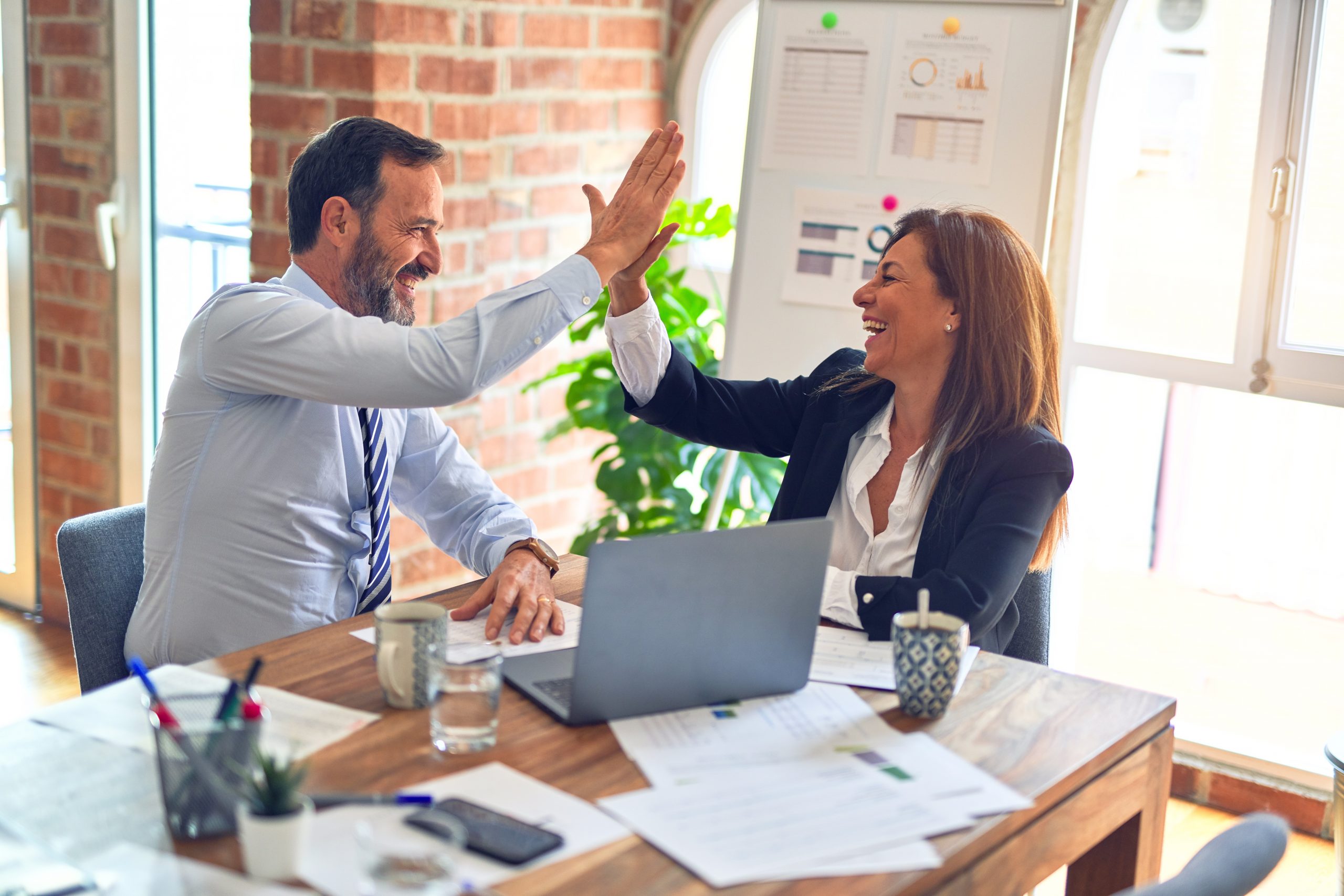
Top process improvement professionals in the energy sector met recently at the 2010 iSixSigma Live! Energy Forum for Process Excellence, May 24-27, in Houston. Presentations covered a broad range of topics – from innovation to leadership and getting started to giving back. Each of the topics was tailored to the specific needs of professionals in the energy sectors, including oil and gas, coal, and nuclear power; exploration and production and refining; and power generation, transmission and distribution. Here are a few highlights from the event.
The Topic on Everyone’s Mind
![]() |
Conference Chair Bob Silvers, a managing director with SSA and Co., kicked off the event. |
There was one topic that, while not on the agenda, could not be overlooked – the Gulf Coast oil spill. In his opening address, Conference Chairman Bob Silvers addressed a tough question: Could better management practices have prevented the BP disaster? Silvers, who is managing director and oversees the energy practice at consulting firm SSA & Co., expanded on the topic in an article (“Deepwater Horizon Disaster Raises Risky Questions“) published in the Houston Business Journal.
“Risk management, scenario planning, and process improvement are nothing new to the oil industry,” he wrote. “However, with more transparent processes and a clear understanding around the broader system as a whole, companies can better anticipate and prepare for the ‘virtually impossible.’ Does this guarantee that catastrophic events won’t take place? Of course not. But CEOs and process improvement professionals alike are paid to maximize opportunity and minimize risk. Continuous improvement is among the few key variables to help accomplish that.”
Unlocking Creativity
Another key variable in today’s business world is creating the products and services that add significant value to an organization and its customers. When it comes to achieving continuous innovation, there’s no silver bullet, but the path forward isn’t as obscured as one might think. In his keynote address, George Land, an expert in innovation and creativity and co-founder of Leadership 2000, walked attendees through nature’s guide for innovation, how the brain works and a disciplined innovation process.
![]() |
George Land, expert on creativity and innovation, said companies must either “innovate or abdicate.” |
Innovation requires imaginative thinking, he said; unfortunately, creativity is unlearned with age. In 1968, Land and a colleague gave 1,600 5-year-olds a creativity test used by NASA to select innovative engineers and scientists. He retested the same children five and 10 years later. They then gave the same test to more than 1 million adults (with an average age of 31 years). The table below shows the fascinating results.
Imagination and Age
Age | Highly Imaginative |
4 to 5 years | 98% |
10 years | 30% |
15 years | 12% |
Adults | 2% |
The good news is that humans can recapture their creativity, he said. There is a lot of brainpower that people simply aren’t using. The key is to avoid stress and fear, and to learn how to think divergently. Divergent thinking, or out-of-the-box thinking, is defined on Dictionary.com as “creative thinking that may follow many lines of thought and tends to generate new and original solutions to problems.”
More good news: Even though people aren’t often using this part of the brain, it does not atrophy. According to Land, it is kept in shape by dreaming, and is therefore ready to be tapped.
How Leaders Can Leverage Tribes
Through innovation, organizations can create breakthrough ideas. To help execute those ideas, they need to leverage their employees and understand the makeup and culture of their company and its groups.
According to Dave Logan, every company is a tribe, or a network of tribes. These tribes are groups of 20 to 150 people in which everyone knows everyone else and shares the same thinking. Logan, who teaches leadership and negotiation in the University of Southern California Executive MBA program, wrote about the topic in Tribal Leadership: Leveraging Natural Groups to Build a Thriving Organization (HarperBusiness, 2008).
Logan present on the topic at the 2009 TEDxUSC:
Starting Up a Process Excellence Program
For process improvement professionals, this concept of tribal leadership – and how to move people from one group to another – may be particularly helpful when they are starting and growing a process excellence program.
Sharing their experiences on “Starting Up and Growing a Process Excellence Program,” were the following panelists, shown below (left to right):
- Stephen Turnipseed, Lean Sigma Advisor, Chevron
- Steve Wells, Special Projects Manager, Luminant Operating System
- Randal Simons, Director, Management Systems, PNM Resources Inc.
Panelists shared their experiences and lessons learned on starting up and growing a process excellence program.
Starting out questions included:
- How do you govern a Lean Six Sigma program, especially in a decentralized organization that is geographically challenged?
- How do you access the performance and maturity level of a Lean Six Sigma program?
- How do you make sure the saving gains are captured and sustained starting out?
- What is your prioritization system for initiating projects?
Giving Back
Much of the forum focused on applying Lean Six Sigma within businesses, but a unique presentation this year reminded attendees that process improvement is a passion that can be applied outside work.
Mauricio Puente, Halliburton, EPIC Lean Six Sigma Manager, and Emily Turner, GE Oil & Gas, Supply Chain Lean Leader, talked about sharing Lean with the Houston Food Bank, the largest source of free and low-cost food for hungry people in 18 southeast Texas counties. When 200-plus grocery stores started donating out-of-shelf-tolerance items, the food bank team had 400,000 pounds of products per week to pick up, repack, sort and redistribute. If not handled in a timely manner, food could spoil.
Emily Turner and Mauricio Puente presented on a Lean project that the Houston Lean Six Sigma Professionals started with the Houston Food Bank.
So volunteers from the Houston Lean Six Sigma Professionals (HLSSP) group – an organization of process and operations improvement focused people – trained core team members at the Houston Food Bank on basic Lean Six Sigma. After mapping the value stream, the team found only 7 hours of value-added time, but 42 hours of non-valued-added time. Together, they came up with an improvement roadmap that includes Kaizens on material movement, freezer truck space, information management and meat inspection standard operations.
Lasting Contributions
The takeaways that attendees gained from the forum went beyond improving their process excellence efforts to how their efforts are making an impact in people’s lives, both within and outside of their organizations. To see more photos from the event, click here.