
Key Points
- Yield can quantify many things in Lean Six Sigma.
- It is frequently used as a KPI in process improvement.
- Additionally, it can determine and monitor the effectiveness of your current processes.
In Lean manufacturing, the “area of improvement” is part of the system under observation. In other words, it’s the part of the factory where defects are produced the most. The goal is to find and fix these defects before they cause any more harm. The concept is a tool used to measure how close you are to meeting this goal. By understanding this tool, you can achieve better performance and manage your work more effectively.
Overview: What is Yield (in Lean Six Sigma)?
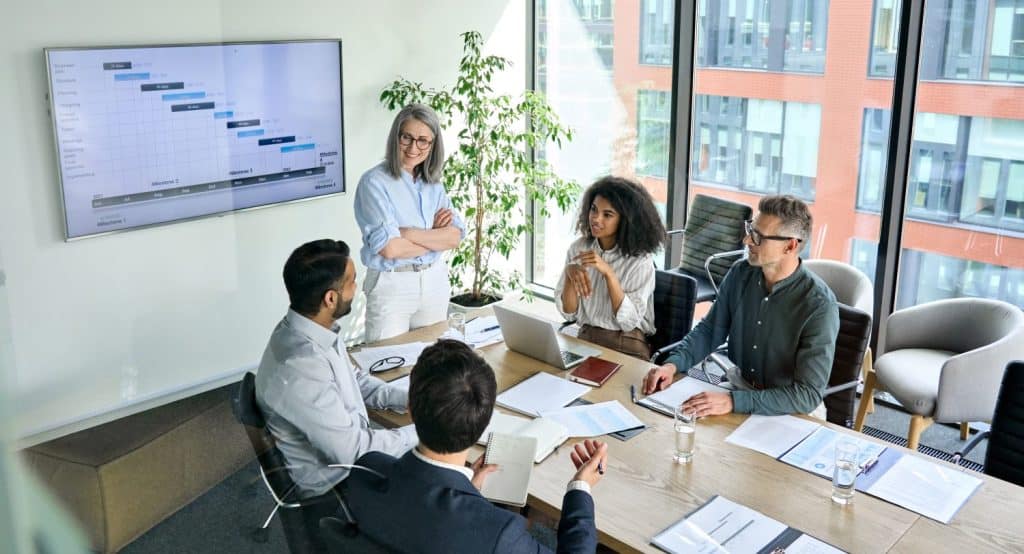
©Ground Picture/Shutterstock.com
It is a measure of the percentage of items produced that meet customer quality or specification requirements. It can be used to manage resources, optimize processes, and measure performance. In Lean Six Sigma, it is often used as a key performance indicator (KPI) in process improvement projects.
Additionally, it can be used to monitor the effectiveness of various improvement projects or processes to determine whether they are producing expected results.
For example, if you were running a process for reordering goods and have determined that this step is lowering your output percentage but not significantly affecting defects per inspection unit (DPI), then it may just be time to evaluate alternate approaches. By measuring how well you’re doing against expectations with specific tools like output management and trend analysis, you can improve the chances of long-term success.
Why It Matters
So, why does yield matter in Lean Six Sigma? There is no shortage of metrics and measurements you keep track of when analyzing any process. However, what yield indicates is exactly how a process functions. While you have plenty of tools in your toolbox, this is one of the most crucial for seeing the final result of your labor.
3 Drawbacks of a Yield-Focused Approach
Some potential drawbacks to a heavy focus on this concept include:
1. Some Employees Could Become Complacent
It can be difficult for employees to embrace this concept because the importance of quality for many companies is not a large priority. Why would employees embrace it if the company does not? With no one incentivized to improve performance over time, the company may suffer from middling results because workers don’t understand or care about what they’re doing or why. Complacency also happens when business leaders aren’t consistently employing this concept as a metric concerning other key processes.
2. Time Could Be Lost Looking for Trends That Are Too Difficult to Identify
This means that companies could be using the concept to calculate certain thresholds for making a process improvement but fail to recognize when these targets are met. One of the most common arguments against applying this concept as a metric is that it doesn’t always make sense in many situations, such as eliminating unnecessary overhead steps on production processes like purchasing agents or managing inventory easily.
While this may not be true at first, looking closely and intelligently enough through the data can at times provide a quick insight into whether adopting these specific metrics could pay off.
3. It’s an Unreliable Way for Companies to Measure Progress or Improve Performance Over Time
This is the most common criticism of this concept because some experts say even small fluctuations in outputs can have large financial implications when applied during decision-making processes by executives. However, other experts believe this criticism oversimplifies things too much. As a result, it’s sometimes the case of just not being able to measure output in a way that makes it clear enough for decision-making or analysis.
Why Is Lean Six Sigma’s Concept of Yield So Important to Understand?
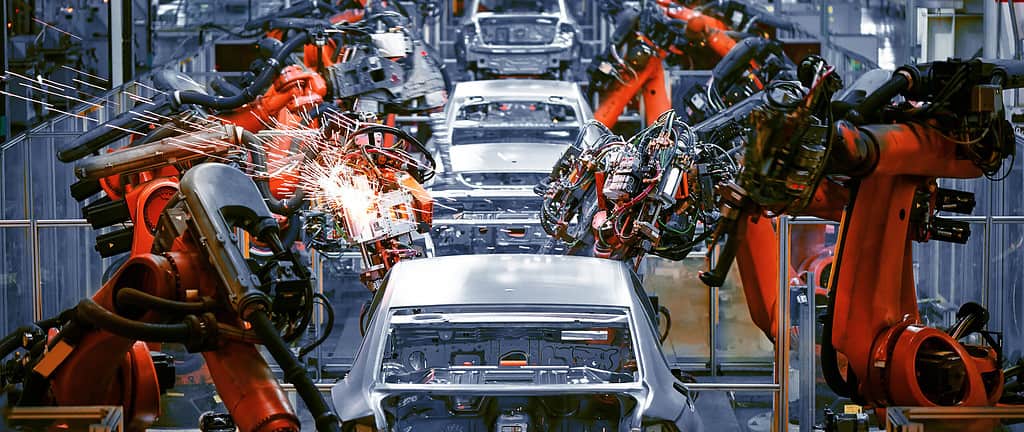
This is an important metric to understand because it helps organizations identify and address areas where they are (or are not) delivering value to their customers. This understanding provides insight into areas where management and staff can focus their efforts, thereby also improving performance.
What this means is that decision-makers are allowed to focus on the performance of their organization because they’re given information that helps them gauge how much value they are delivering and where improvements can be made.
This metric is also important in an interesting way that other metrics are not: it’s a way for companies to measure competition in general, and the direction that competition is going, specifically.
This allows for increased recognition within an organization – a heightened awareness of the space that particular organization occupies within the industry and about other companies doing the same thing – which can be instrumental not only in retaining top employees but also in attracting new ones.
An industry example of yield
A simple illustration of the concept can be found in cooking or baking. When you look at a recipe for brownies or cookies, just as two examples, there is an ending quantity.
This is the number of servings or how many individual cookies or brownies you should have at the end – the amount of “product” that you should have if everything came together and you were able to capitalize on every opportunity to make another defect-free cookie using the supplies and instructions given.
If there are mistakes, a shortage of materials, a flaw in the instructions, or a problem with the ability or skill level of the person executing the recipe, that output will change. Missed opportunities will produce smaller output.
It’s important to note that this can showcase an example of a higher output not necessarily being a good thing either. Higher output could mean the finished products are smaller, were assembled with less care, or were missing required ingredients, all resulting in products that fail to meet expectations.
Best Practices
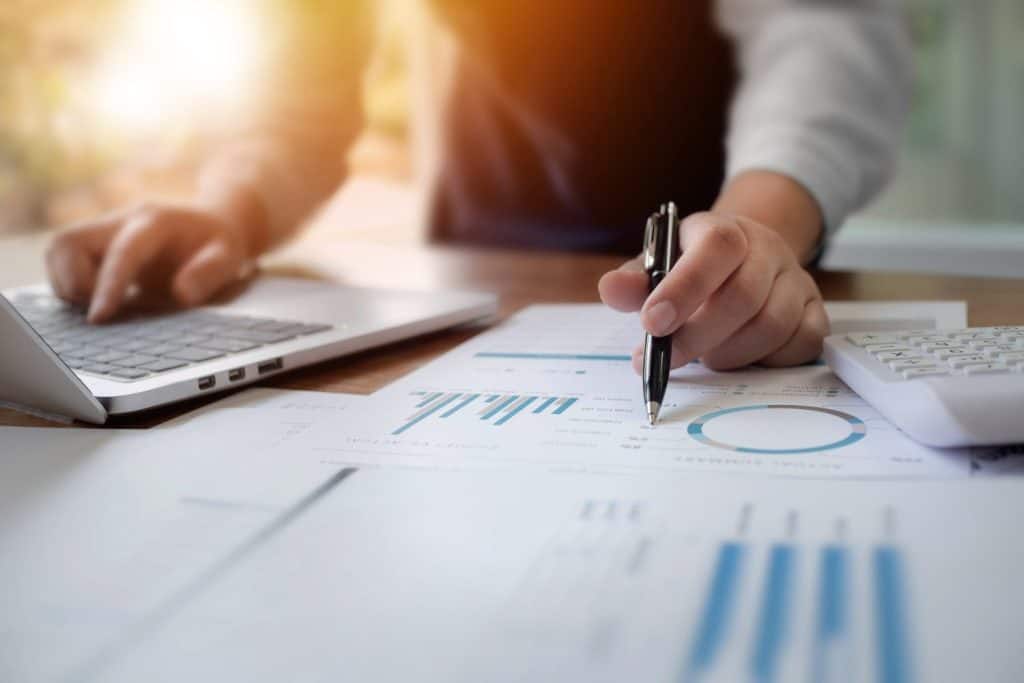
©Oakland Images/Shutterstock.com
1. Maximize the Output from Processes and Remove Waste
In other words, make these processes repeatable, efficient, and reliable. Then, the recipe for constructing a product can be established efficiently. As a result, the supply chain can be optimized to incorporate processes that move the product through it with speed, and quality control steps can ensure lower losses.
2. Periodically Evaluate Process Outputs to Determine If They Are Meeting Desired Outcomes
Then, the process of making a product can be adjusted, eliminated, or added as necessary. This will induce improvement in the quality of products, maximum efficiency, and reduction of waste cascading back down through the supply chain optimizing margins at every step level.
3. Identify and Implement Optimization Techniques to Increase Output*
Different applications require different processes. Techniques to increase outputs include careful strategy design, fully implemented process improvements, and increased workforce efficiency.
Each of these areas will also have targets defined for improvement over time based on an open-ended goal or a specific target value that must be achieved to obtain new cost savings or improved profitability metrics that are aligned with business objectives such as higher margins or lower overall costs.
*When doing so does not result in an inferior product or one that fails to meet expectations.
Other Useful Tools and Concepts
Looking for some other tools to supercharge your production? Understanding how Tollgates function throughout the DMAIC methodology is a vital thing. These function as a stopgap in the entire process improvement methodology, allowing your employees to see exactly how things are going.
Additionally, you might want to pay attention to Ppk. While yield is useful, Ppk can clue you into how your production line is functioning daily.
An Omen?
Ultimately, this is a concept that pertains to management decisions as a measure of asset utilization and value creation. It is a dynamic system that depends on the amount it can produce per dollar spent and is also a measure of production and the return on investment for management. But most significantly, it can be an omen of a company’s future performance. In other words, one’s output is the measure of value that a company has produced from its investments, and by extension, this can make it an indicator of future performance (value).