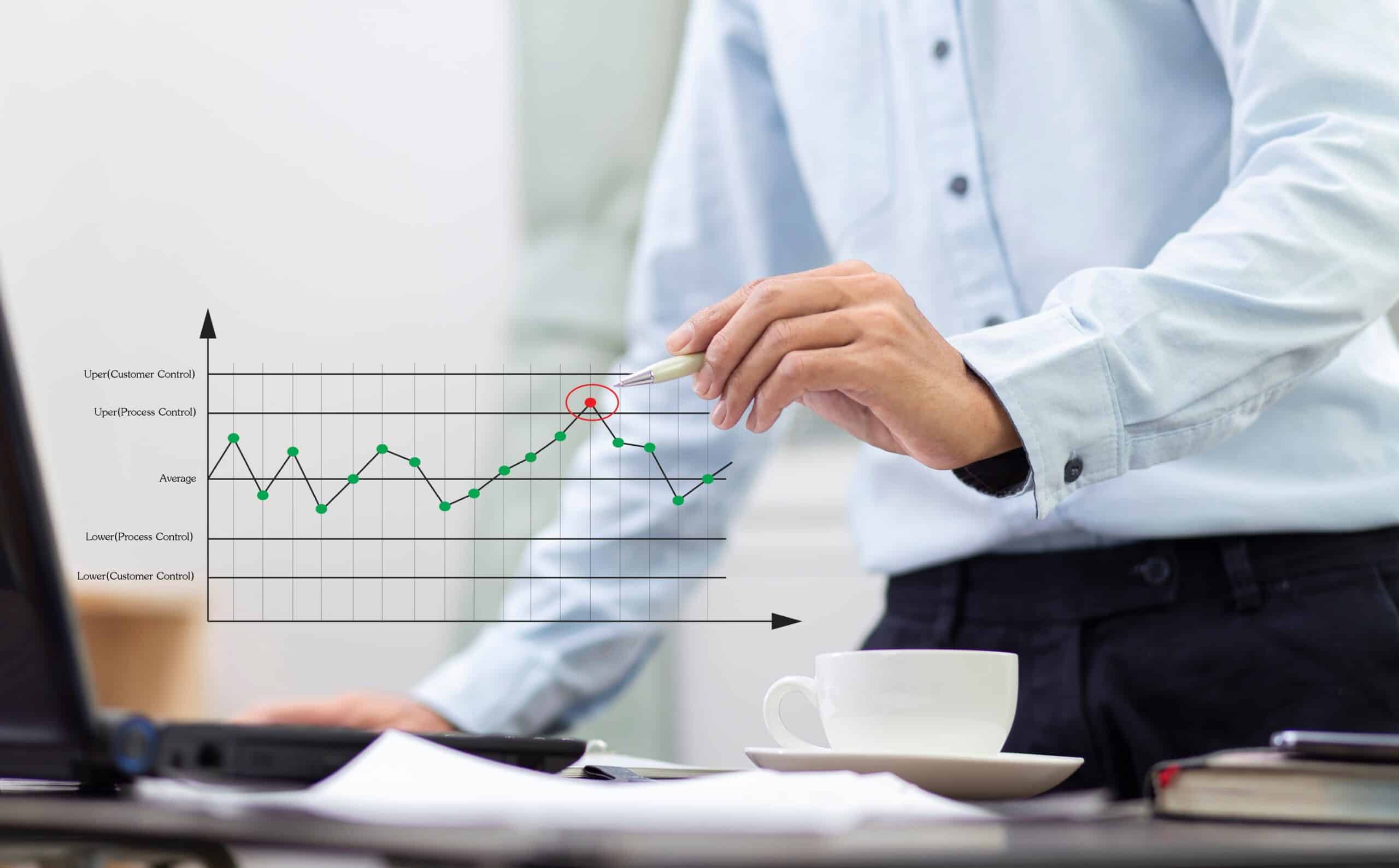
Key Points
- Warning limits are the upper and lower control limits in a control chart.
- When values exceed these limits, it proves as a signal for potential issues.
- Understanding how to read them effectively allows you to make better use of your data.
The mere mention of technical terms related to statistical analysis can make eyes glaze over, but it shouldn’t be that way. Leveraging statistical quality or process control is vital for many businesses, particularly those involved in mass manufacturing. Strict data collection and effective analysis are necessary for identifying, addressing, and preventing problems that can jeopardize the entire production process.
Overview: What Are Warning Limits?
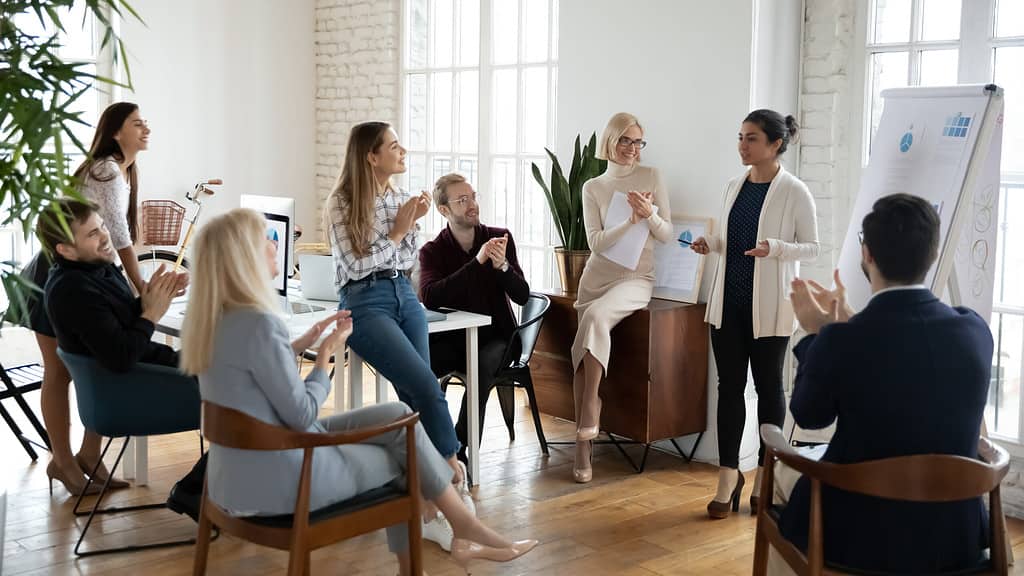
You can’t appreciate these limits without a basic understanding of control charts. Control charts are data-heavy graphs that illustrate metrics regarding a business or production process based on multiple variables or attributes. These graphs typically display multiple horizontal lines, called action or control limits, that indicate a serious problem. These lines essentially represent the limit of acceptability. Any data sample that falls outside of these limits must be addressed.
Upper and lower limits are placed within the confines of the action or control limits to serve as an early alert system. They are closer to the expected mean of the data sample. If a sample crosses this line, it indicates a need for further sampling and possible investigation of the deviance.
Using Warning Limits
We’ve talked about what they are, but how do you use warning limits? While control charts have applications originally in manufacturing, they serve a vital purpose for a variety of industries. As such, you’ll find they work best for forecasting data, looking at trends, and determining if defects are present in deliverables like software or services.
3 Benefits of Warning Limits
Most of their benefits revolve around maximizing your statistical analysis techniques and adopting a proactive stance against deviance. Consistency is an important attribute for any company, particularly when flaws or deviance can compromise the usability of the product.
1. Planning for Prevention
Since these limits are set at a tighter range than the controls, they indicate deviance before these anomalies start compromising quality. This can help you identify the early signs of a problem, whether it’s mechanical, procedural, or human error before it starts causing losses.
2. Improved Sampling Efficiency
When data breaches this limit, the standard response is to take another data sample. If this one also passes the upper or lower warning line, then it’s time to take action. They help minimize the burden of data collection by focusing additional sampling on processes that already show signs of deviance.
3. Flexible Applications
These limits conform to the standards of the control chart and processes in question. Lines can be adjusted to tighten or relax monitored deviations to reduce false alarms without compromising quality.
Why Are Warning Limits Important to Understand?
Limits are a useful component for control charts, which are an essential part of any serious statistical quality control (SQC) initiative. This kind of quality control is particularly important in complex and high-stakes manufacturing environments.
1. Reading Control Charts
Anyone involved in quality control or statistical analysis should know how to read control charts, which also means understanding warning and action limits. Even though these charts are closely associated with production environments, they can actually be used to evaluate any kind of business process.
2. Appreciate Potential Accuracy
It’s also important to understand that these limits can raise a lot of statistical false alarms. Even in normal operations, you can expect about 1 in 20 samples to pass this limit, but only a small portion of these should exceed the control lines.
3. Fundamental to Process Control
Since warning lines are linked to statistical deviation, understanding them also means understanding the fundamentals of statistical analysis. Some of the equations can be complicated, but the principles and implications are foundational for business management.
An Industry Example of Warning Limits
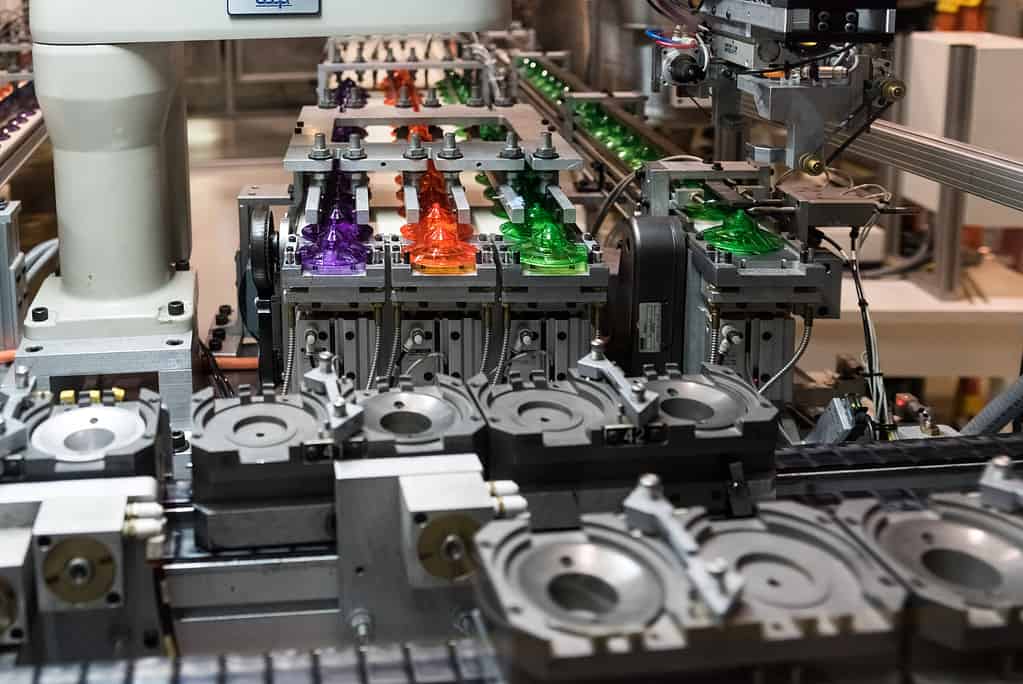
A large manufacturer produces many kinds of packaged foods at one of their sites. One of their key products is small, serving-size bags of chips. Each bag is advertised as weighing 8 ounces or about 227 grams. This weight of 227 grams is the mean or expected value of each bag, but not every bag will be exactly this weight.
To ensure general quality, the manufacturer selects sample bags at random and weighs them. In this example, a standard deviation for this bag would be 4 grams. Any bag beyond three standard deviations (12 grams), which is above 239 or below 215 grams, is considered not acceptable for sale. In this case, the warning limit would be set at 8 grams on the control chart, so samples that include bags weighing less than 219 or more than 235 would warrant further sampling.
3 Best Practices When Thinking About Warning Limits
The best way to consider and leverage these limits requires the effective use of control charts in your process control methodology. Accurate and consistent data sampling and analysis are key to preventing and addressing problems during production.
1. Know Your Standard Deviation
Standard deviations are calculated by using a complex formula on a comprehensive data set. This initial evaluation serves as the base for all of your further sampling and control limits, so it’s vital to do it well and to only use up-to-date information.
2. Set at a Useful Sigma Line
Limits set at two standard deviations from the mean are also called 2 sigma, while those at three deviations are 3 sigma. Even though 2 sigma is the standard for control charts, there are occasions to set the line closer or farther from the mean. This can take some trial and error to find a place that maximizes preventative potential without causing an undue amount of additional sampling.
3. Develop Data Collection Practices
Control charts and limits are only as useful as your data collection methods. This means you need to ensure your sampling, metric evaluation, and overall analysis are all done according to the proper procedure for statistical analysis.
Other Useful Tools and Concepts
Warning limits aren’t the only thing you’ll need to keep track of in your organization. Learning how to effectively conduct root cause and failure analysis is an effective way of reducing costs and correcting defects as they occur.
Further, you might need to brush up on how to deal with special cause variations. These variations can cause spikes in your warning limits, so learning how they apply to your production line will save time and headaches.
Conclusion
The phrase “know your limits” isn’t just about being cautious and reasonable in your personal life, it has applications for businesses as well. Control charts and limits on deviancy from expected results are essential for keeping your finger on the pulse of your production process. Statistical monitoring is foundational for basic quality control, loss prevention, and procedural problem-solving.