
Key Points
- Special cause variations are new variances that have never been encountered.
- Typically, these are caused by factors outside of your control when managing processes.
- There isn’t a way to viably prepare for these, but you can spot them readily.
Common cause variations are those variations that happen as part of natural patterns. These kinds of variances are inherent in the process, consistent, and normal. Special cause variations are quite different than these sorts of variances.
Overview: What Is Variation (Special Cause)?
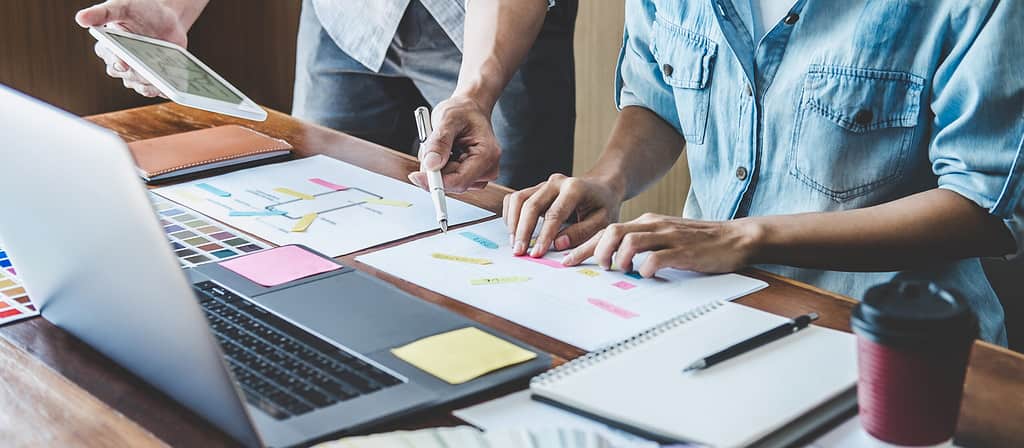
These are the variances that are unexpected, non-quantifiable, and unusual. Special cause variations are those that in a process have not been encountered before. They are caused by unpredictable factors. Examples of special cause variations include machine faults, power surges, operator absences, and computer faults.
3 Drawbacks of Special Cause Variations
There are some drawbacks to special cause variations that should be acknowledged:
1. They Can Be Difficult to Prepare For
Special cause variances can be so random that it can be extremely difficult to adequately prepare for them.
2. They May Cause Serious Problems
Some special cause variations can be eliminated due to them being a technical issue. If preventable, they should be as they can cause major problems for the business.
3. The Source Can Be Difficult to Find on a Control Chart
The source of special cause variations can be difficult to spot on a control chart if you are not plotting in real time. To find the source of the special cause, you would likely have to have annotated data or an exceptionally good memory.
Can You Prevent Special Cause Variations?
Not really, at least not in any way that matters. The simple fact of the matter is that you’re going to have to rectify these issues as they arise, rather than taking preventative measures. Common cause variation allows you to take corrective actions, you’re chasing after shadows with special cause variation, however.
Why Are Special Cause Variations Important to Understand?

For the following reasons, special case variations are important to understand:
Statistical Instability
If you have a chart that only has common cause variations, it means that your process is likely “statistically stable.” Understanding special cause variations on your chart, helps you recognize the inverse. It means that your processes are “statistically unstable” and that modifications may need to occur.
You Can Spot Them on a Control Chart
By understanding special cause variations, you can probably pretty easily spot them on a control chart. Should the measurements of a process be distributed normally, it is almost guaranteed that a measurement will fall within plus/minus three deviations. Measurements that fall outside these limits are likely to be special cause variations.
Understanding Them Makes Them Easier to Investigate
If you get a measurement on a control chart that appears to be a special cause variation, the expectation is that it will be investigated, there will be a root cause analysis, and appropriate measures will be taken.
An Industry Example of Special Cause Variation
A project manager has been leading the test drilling for a new site where it is believed that there is likely a significant amount of untapped crude oil. The test drilling was supposed to last for a week, but one of the drills malfunctioned, which caused a delay. Instead, the test drilling took a total of 30 days once the faulty drill issue was addressed. The malfunction is an example of a special cause variation.
Best Practices for Special Cause Variation
Here are a few practices to bear in mind when it comes to special cause variations:
1. Countering Special Cause Variations
Contingency plans can be used to counter special cause variations. With this strategy, additional processes are incorporated into operations that prevent or counter a special cause variation.
2. Recognize Them on a Control Chart
Remember that if it falls plus/minus three deviation limits of a measurement on a control chart, it is probably a special cause variation.
3. You Can Avoid Over-Tampering
If you do not understand how variation works, you could feasibly over-adjust, which can then lead to even more variation every time there is a process change.
Other Useful Tools and Concepts
You might need some extra tools to account for and document variation in your processes. Understanding how common cause variation works is a complimentary knowledge set for any production cycle.
Additionally, learning about total observed variations allows for better overall quality in your deliverables. Learning how to manage and measure this sort of variation can be tricky, but our guide has you covered.
Eliminating Special Cause Variations
While it can be difficult to predict an initial special cause variation, steps can be taken to help ensure that the same problem does not arise again. Technical improvements, proper training, and other strategies can all help protect your company from repeat incidents.