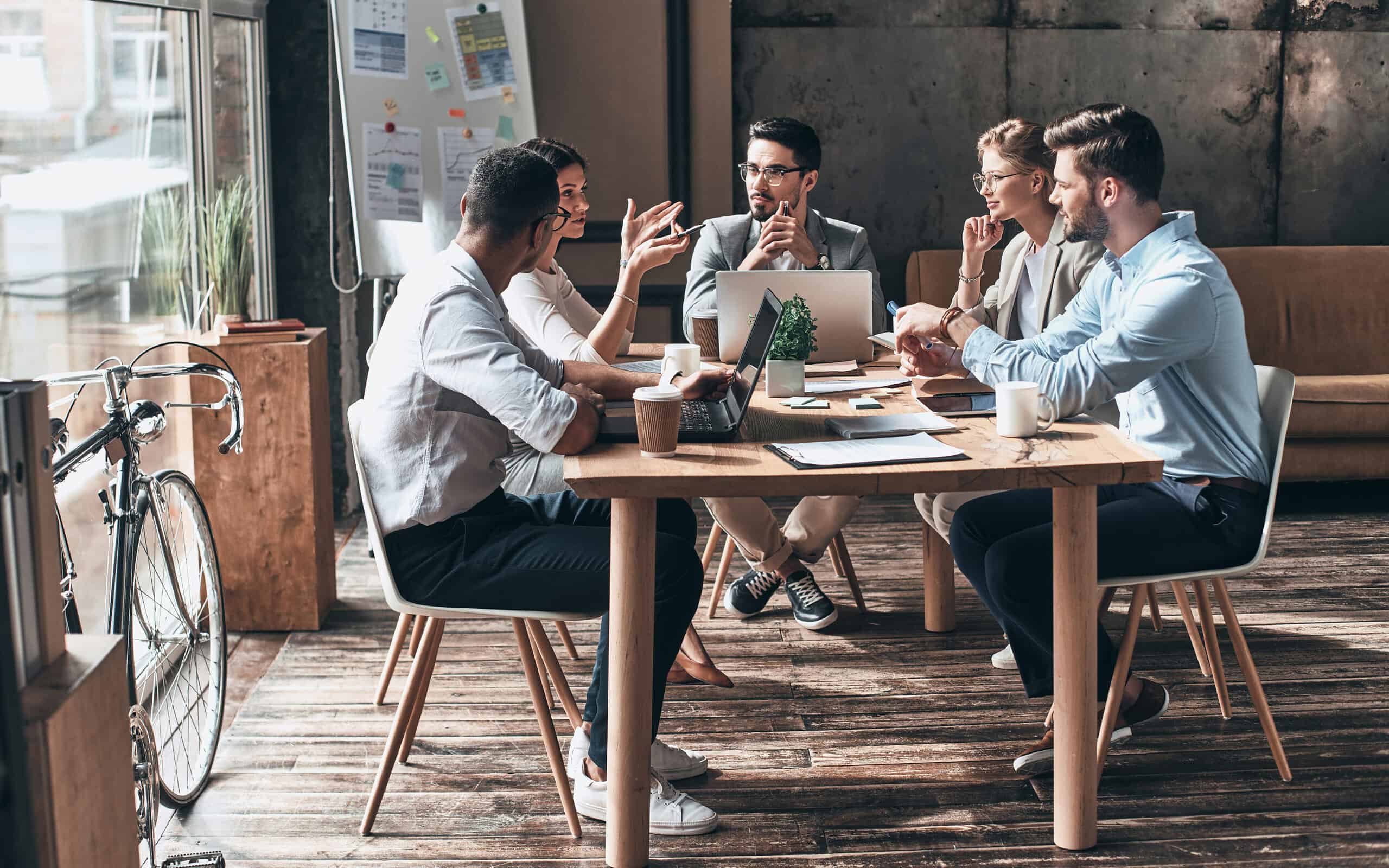
While many organizations utilize Kaizen (often referred to as a Kaizen Event or Kaizen Blitz) for expedited improvement activities, there is often confusion as to what a true Kaizen is and how to properly execute one.
This article will describe what a Kaizen is, the benefits of a properly executed Kaizen, and some best practices to take advantage of a Kaizen.
Overview: What is Kaizen?
The concept of Kaizen was developed and popularized by Masaaki Imai, a Japanese organizational theorist and management consultant. Much of his work was based on the Toyota Production System (TPS) and its lean principles.
In 1986, he founded the Kaizen Institute Consulting Group to introduce the concepts, systems and tools of Kaizen to western organizations. His two published books, Kaizen: The key to Japan’s competitive success and Gemba Kaizen: A Commonsense, Low-Cost Approach to Management served as the foundation for implementing Kaizen.
Simply put, Kaizen is the philosophy of continuously improving all processes in an organization through the engagement and involvement of all employees. It is a continuous, structured, and methodical approach to improvement. The word Kaizen is the combination of two Japanese words, Kai and Zen. Their literal translation into English is shown below.
A Kaizen is an expedited formal and structured improvement activity consisting of a Team of inter and/or intra functional people (5-8) over a concentrated duration of time (3-5 days) who utilize the DMAIC (Define-Measure-Analyze-Improve-Control) methodology to solve a scoped problem and improve the underlying process(s).
A Kaizen will usually be facilitated by a Lean Six Sigma Green Belt, Black Belt, or Master Black Belt and sponsored by a member of leadership.
Unfortunately, some organizations use the term Kaizen to describe any activity where two or more people get together to talk about problems. A true and proper Kaizen, though, is structured with a Charter — a defined problem that’s driven by data — and with participants chosen to provide the best input for optimal outcomes.
Depending on your specific Internet search, you will find there are 3, 4, 5, 10, 11, or 15 principles of Kaizen. If we check the website of the Kaizen Institute founded by Masaaki Imai, you will see he summarized Kaizen with 5 principles.
5 Fundamental KAIZEN™ Principles
A Kaizen utilizes the DMAIC methodology in three sequenced phases: Preparation, Event, and Followup. A typical 5-day Kaizen will use the following schedule, although there is flexibility depending on the problem being addressed.
Define (Preparation Week)
- Clearly define the objective of the Kaizen.
- Pre-Kaizen prep: Select your Team, organize the Kaizen logistics, notify participants, collect needed data, and provide any Kaizen training for the team or organization.
Measure (Prep Week and Monday of the Kaizen)
- Review and validate any process mapping that was done.
- Go to Gemba (where the work is done) and observe and record any observations relevant to the Kaizen.
Analyze (Tuesday-Wednesday)
- Validate root causes, identify and review potential sources of the problem.
- Brainstorm potential process improvements.
Improve (Wednesday-Friday)
- Create an action item list for implementing any improvement recommendations including people, responsibilities, timelines, and status.
- Pilot your improvements if appropriate, train employees, revise as necessary, and ensure the process is capable.
Control (Thursday-Friday)
- Develop and write standard operating procedures to document and sustain your improvements.
- Present your Kaizen outcomes to the appropriate level of management, complete your follow-up, and develop a control plan to maintain your gains and monitor your results over time.
According to the Kaizen Institute, here are some of the reasons you should use Kaizen:
6 benefits of Kaizen
Rapid continuous improvement in the form of a Kaizen has benefits to an organization. Here are a few.
1. Training
Pre-event training provides the opportunity to expose participants to the concepts of Lean Six Sigma as well as the variety of improvement tools used during the Kaizen. Likewise, applying the tools to a real problem increases the improvement skills of the team members.
2. Discovery
One of the first activities in a Kaizen is for participants to go to Gemba and observe the current state of the process. The participants, if appropriate, may be assigned to separate subcategories of the problem or process. Each sub-team independently goes to Gemba, documents their observations, and returns to present their findings to the entire team.
3. Teamwork
Given the diverse nature of the participants, the opportunity to interact and collaborate towards a common goal allows for development of some of the soft skills of working in a team environment.
4. Learning curve
The more Kaizens an organization successfully runs, the greater the opportunity to involve more and more employees. This will lead to more effective and efficient future Kaizens.
5. Leadership opportunities
It is recommended that the “leadership” role of the team be shared amongst the team participants. This will enhance the personal skills of the participants and give the organization a chance to observe and assess whether there is a “hidden jewel” on the team who could be slated for a future leadership role in the organization.
6. Improvement culture
The more organizational people immersed in successful improvement activities, the faster the improvement culture will develop.
Why is Kaizen important to understand?
To utilize the power of Kaizen, it is important to understand when and how to conduct one.
Still follows the DMAIC methodology
A Kaizen is a time-compressed process that still utilizes the DMAIC approach. It is not equivalent to a quick win or simple problem-solving.
Implementation of improvements should be quick
You will want to implement as many improvement recommendations as you can within 30-60 days of the Kaizen. In fact, you may be able to implement some during the Kaizen.
Not all team activities are a Kaizen
Many organizations use the term Kaizen to describe any kind of activity where people get together to address process issues. However, Kaizen is a formal and structured approach and not just a quick get together of employees.
An industry example of Kaizen
A major consumer products company delivered their products to customers on heavy-duty reusable plastic pallets. The site chosen for the Kaizen purchased over 100,000 pallets during the year for a cost of over $8,000,000. The standard process, after delivery, is for the driver to pick up and return the empty pallets back to the company location. The problem was the return rate was only 72%, requiring the ongoing purchase of new pallets.
A Kaizen team was formed to include members from finance, delivery, warehouse, sales, merchandising, and the pallet supplier. The team was subdivided into three groups to go visit local customers consisting of large grocery stores, small grocery stores, and convenience stores. Each group recorded their observations on how the pallets were handled and stored in the stores. All groups returned and shared their observations and insights.
After analyzing the problem and process, the team determined the problem was due to driver issues, customer issues, and theft. Recommendations were made to improve communication, accountability, and security.
On the fifth day of the Kaizen, the team made a presentation to the sponsor and the entire executive leadership team. The site improved the return rate from 72% to over 85% for a direct savings of approximately $1,000,000. The team also made recommendations to replicate their work, resulting in a system-wide capital savings of over $4,500,000.
Best practices when thinking about Kaizen
A Kaizen requires planning and coordination. Some of the best practices consist of:
- Preplanning to identify the appropriate scope, participants, and the collection of relevant data.
- Having support in the form of Green Belts, Black Belts, and/or Master Black Belts as well as, most importantly, the sponsor.
- Staying focused and on task.
- Making available a subject matter expert (SME) during the Kaizen who, if needed, can quickly collect and analyze additional supporting data.
- Identifying people in the organization who can provide specialized knowledge but are not required to participate for the entire Kaizen.
- Communicating frequently with the sponsor(s).
Frequently Asked Questions (FAQ) about Kaizen
Where does the word Kaizen come from?
The word Kaizen is derived from the Japanese language. Kai means “change” and Zen means “for the better.”
Can I do a Kaizen Event in less than the recommended 3 to 5 days?
While it depends on the scope of the project, it is not recommended since most Kaizens of shorter duration will likely be incomplete and skip the needed work for a successful outcome.
What are some of the most important considerations for a successful Kaizen?
Some of the most important elements are a properly scoped project, a supportive and active sponsor, carefully selected team members, and accurate and reliable data.
Final thoughts on Kaizen
Historically, Kaizen has been a successful expedited approach to improving organizational processes and solving problems. But, be warned — it takes proper planning, coordination, resourcing, and communication to be successful. Keep in mind that improvement can be rapid, improvement can be breakthrough, and the best ideas will come from your people.