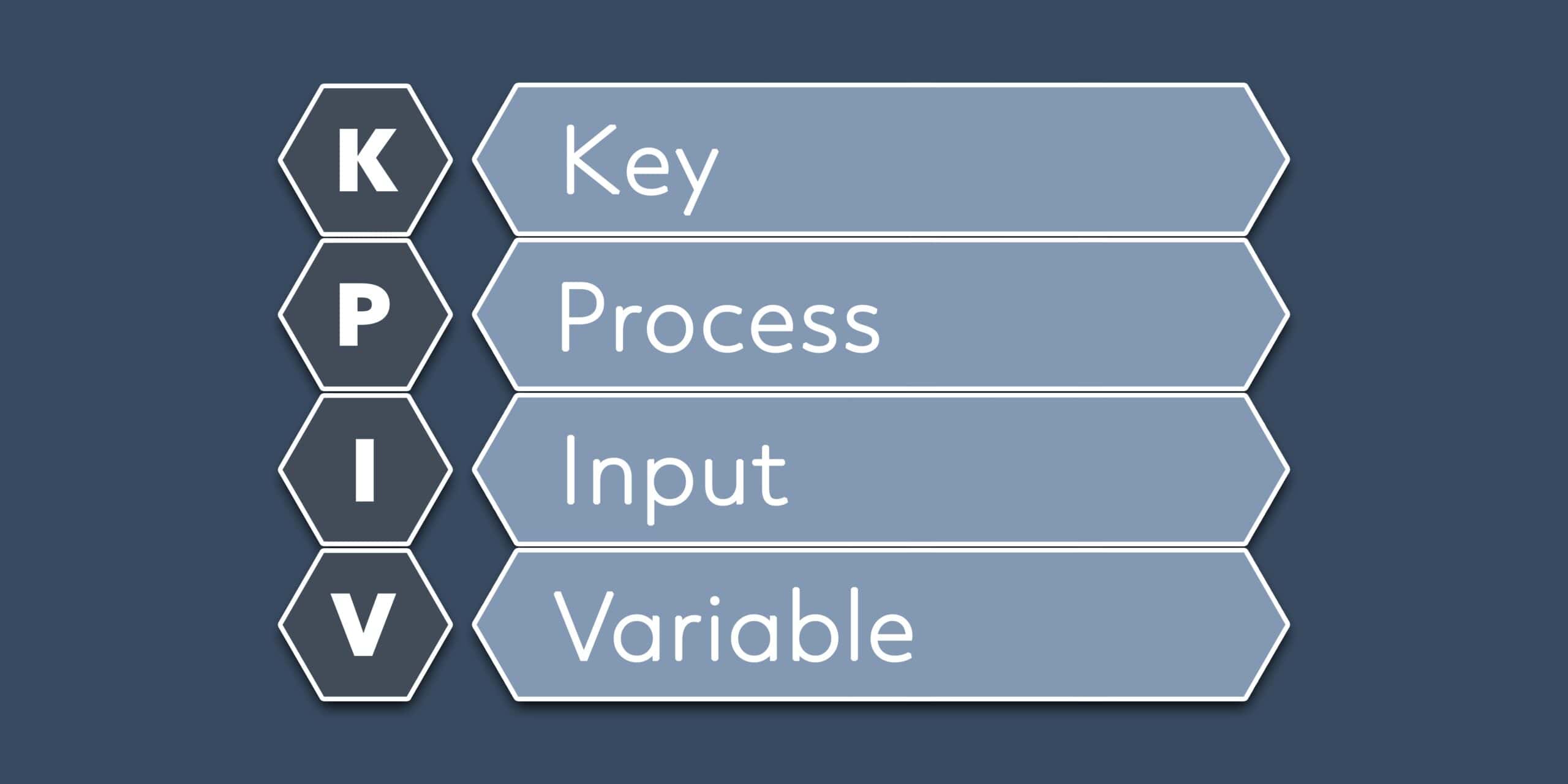
Key Points
- KPIV is a process input that can determine product quality.
- Analyzing it can be time-consuming but worthwhile.
- You can utilize cause-and-effect matrices to see the overall effect on your project outputs.
Reducing and controlling product or process variation is fundamental to meeting customer requirements and building customer satisfaction. If we understand which input variables are key to achieving consistent output, and we prioritize and optimize these variables, then we have just defined our KPIVs. Let’s find out more.
What Is the Key Process Input Variable?
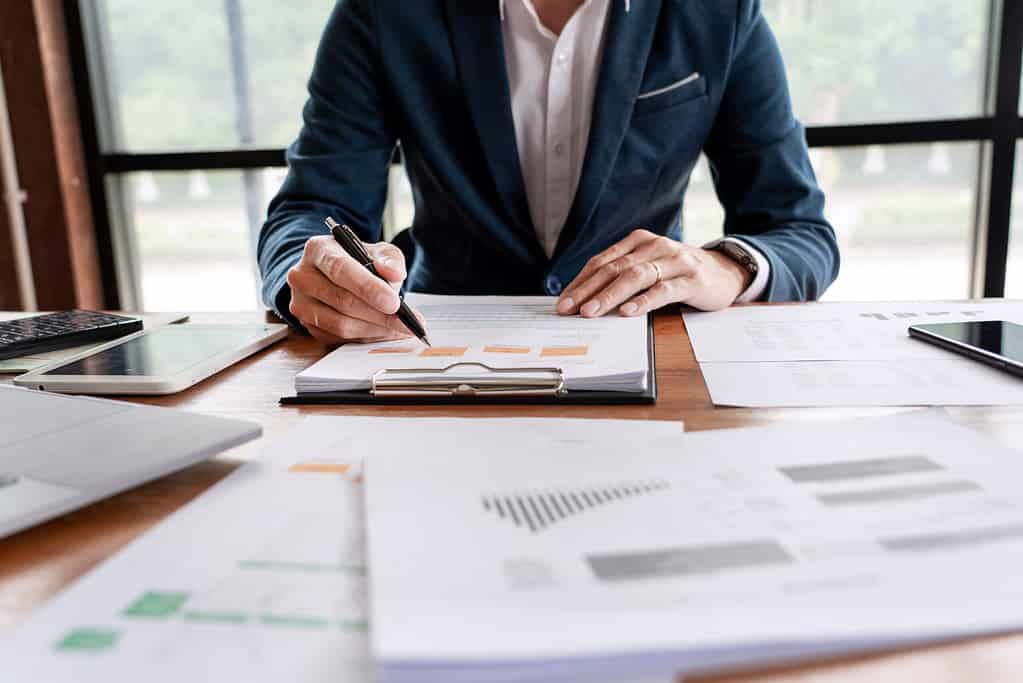
A key process input variable (KPIV) is a process input that provides a significant impact on the output variation of a process or a system, or on the key process output variable (KPOV) of a product. If a KPIV is held constant, it will yield a predictable and consistent output. As such, the KPIV determines the overall quality of the KPOV or the quality of the output of either a process or a product.Â
In a classic Six Sigma project, we are striving to reduce process variation and remove defects, and KPIVs are part of our toolbox to achieve this. However, before we can understand and assess our KPIVs, we will first explore our customer requirements to ensure we are controlling our process output or product attributes to match the customer’s needs.
To better illustrate KPIVs, let’s consider these two cases:
- A specific material hardness is a defined customer requirement and KPOV; the temperature at which the material is hardened and the time at temperature would be KPIVs.
- The minimum slip torque of an automatic transmission torque convertor is a defined customer requirement and KPOV; friction plate flatness and material coefficient of friction would be KPIVs.
Often, the most difficult challenge is determining the correct KPIVs in a product or system that will yield the most significant impact on the output variation. A One-factor-at-a-time (OFAT) approach may be appropriate if the number of KPIVs and KPOVs is small, but often this is not the case. For more complex interactions, we can utilize a statistical analysis approach such as the Design of Experiments (DoE), which significantly reduces the time and resources required to map the relationships between KPIVs and KPOVs.
2 Benefits and 1 Drawback of Key Process Input Variable
Understanding how to influence and control product or process variation with KPIVs is fundamental to the adoption of Six Sigma principles. Let’s explore some benefits and drawbacks of utilizing KPIVs.
Fully Explore the Relationship Between Input and Output Variables
Typically, products and processes have multiple input and output variables, which we can explore via input process output analysis. Once documented, the input variables can be assessed for their impact on output variation reduction and then prioritized as KPIVs.
Desensitize and Control Your Product or Process Output Variation
We want to focus our time and apply our resources to those input variables that desensitize and control our output variation. With our KPIVs identified, we can efficiently target the right output quality to meet our Critical to Quality (CTQ) requirements.
Analysis Can Be Complex and Time-Consuming
Multiple KPIVs and KPOVs mean the potential for complex relationships that can be time-consuming and resource-intensive to explore. However, statistical analysis approaches such as Design of Experiments (DoE) can be helpful to reduce the resource burden.
Why Is the Key Process Input Variable Important to Understand?
By using and understanding our KPIVs, we can optimize our products and processes, reduce rework, and build customer satisfaction. Let’s explore this further.
Meet Your Customer Requirements
Customers require and expect certain features and attributes to be delivered consistently. By understanding and controlling our KPIVs, we are on the road to consistent product or process delivery and customer satisfaction.
Control the Variation in Your Product, Process, or Service
If we fully understand the relationships between KPIVs and KPOVs, we can control and optimize the variation in our products, processes, or services. Cause and effect matrices are great tools to help map these relationships.
Optimize the Value, Cost, and Function Equation
Often, we find there are multiple KPIVs that combine to deliver the required functional output. By understanding the sensitivity of each KPIV, we can rebalance and re-optimize the value, cost, and function equation to both meet our customer requirements and our internal cost and profitability targets.
An Industry Example of Key Process Input Variables

A Six Sigma Black Belt project was initiated to understand the reasons for unexpected variations in the viscosity of a gearbox oil. The end user of the oil performed product conformance testing and rejected several batches due to the viscosity being too high.
Viscosity was one of many key process output variables being checked for conformance, and historically, the process input variables had been assessed and prioritized to ensure acceptable output variation.
The Black Belt team leader conducted a fresh-eyes review with the oil formulation and blending teams to ensure all process input variables had been documented. Due to the high number of input and output variables, a factorial Design of Experiments was designed to understand the complex interactions and determine KPIVs.Â
One of the most significant interactions found was a viscosity modifier additive, the overall oil viscosity being extremely sensitive to the amount of additive and blending time. With these two KPIVs, a further DoE experiment was conducted to refine and reduce the output variation. With the revised settings for both the amount of viscosity modifier additive and blending time, the gearbox oil no longer exhibited unexpected variation in viscosity.
Relating KPIV to KPOV
We’ve discussed how to calculate and why to use key process input variables. However, we haven’t covered the best way to show the relation to your key process output variables. The best tool for the job is going to be a cause-and-effect matrix. This shows all underlying relationships and can help reduce the time needed
Best Practices
As with many process-driven activities, there are some key things for us to consider when investigating our KPIVs. Let’s look at three of these.
Understand Your CTQ Characteristics
There is a logical sequence to follow that helps us evaluate and prioritize our KPIVs. Starting with CTQ, we understand what attributes are important to our customers. We then analyze our KPOVs and focus on how we can control our KPIVs to ensure consistent output and quality.
Fully Evaluate the Relationship of KPIV to KPOV
Most products and processes will have multiple KPIVs and KPOVs, and we need to evaluate and explore the relationship between these. Our efforts should focus on those KPIVs that efficiently reduce the variation of our KPOVs.
Use Statistical Analysis Tools Carefully
With multiple KPIVs and KPOVs, it can be complex and time-consuming to evaluate their relationships. However, we can use statistical analysis tools such as Design of Experiments (DoE) to help us reduce the time and resource burden. We need to take care with the interpretation of the outputs from a DoE and fully test our hypotheses.
Other Useful Tools and Concepts
If you’re on the hunt for other useful tips and tricks, you’re in the right place. Hypothesis testing can be daunting, but making use of the two-proportions test can get your testing back on track. This handy test helps with determining whether to pass or fail your null hypothesis.
Additionally, you might want to consider learning about the Anderson-Darling test. This tool enables you to analyze data that doesn’t fall within the confines of a normal distribution.
Conclusion
Focusing efforts on determining and understanding those key process input variables that significantly impact our output variation is an all-around winner. We not only meet our customer requirements, but we reduce our internal costs and scrap rates, too.