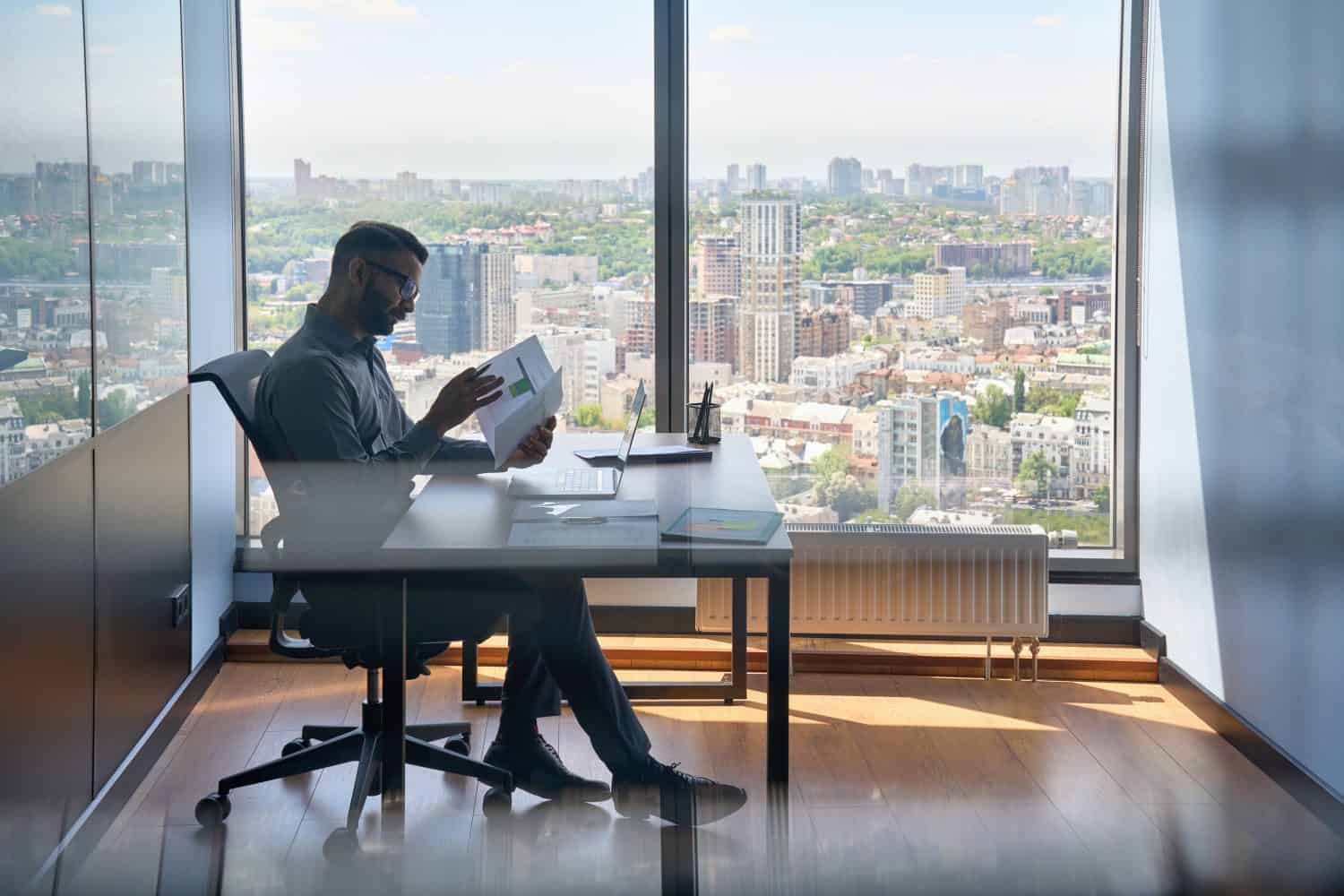
© Ground Picture/Shutterstock.com
Key Points
- An ECR is a form used for proposing changes to a product.
- Before starting the change process, you file an ECR.
- It can be time-consuming and cost-prohibitive to enter the change process, but might be necessary.
An ECR is not something you typically want to happen. They generally result in some additional cost, a slowdown or shutdown of the process, and delays in the completion of the work.
Let’s get a deeper understanding of what an ECR is and what should be included on your form.
What Is an Engineering Change Request?

Once you realize a change is needed in your product or product design, the first step is the completion of an ECR. You can define an ECR as a form used to describe a suggested enhancement, revision, or fix to a product. The form begins the change process and initiates discussions within the engineering team to help determine the impact of the proposed change and the best possible solution.
Once the ECR is approved, an engineering change order (ECO), is completed that further describes the details of the proposed change. This allows for a more formal review and approval process with all teams involved in planning, procuring, testing, assembling, and supporting the final changes.
The ECR form should include the following information:
- A description of the problemÂ
- Why the change is needed
- Recommended change
- The part number(s) affected by the problem
- The part descriptionsÂ
- Who is making the request
- Submission date
- Names and roles of key stakeholders
- Stakeholder feedback on the change
- Next steps and actions needed to resolve the problem
Why It Matters
It would be disastrous to enter the change process without some form of documentation. The ECR helps to communicate the need for changes to all those involved, from the stakeholders down to the average team member. Further, it acts as a safeguard, ensuring that you and your team understand the problems that have arisen and know the need for remediation.
An Industry Example
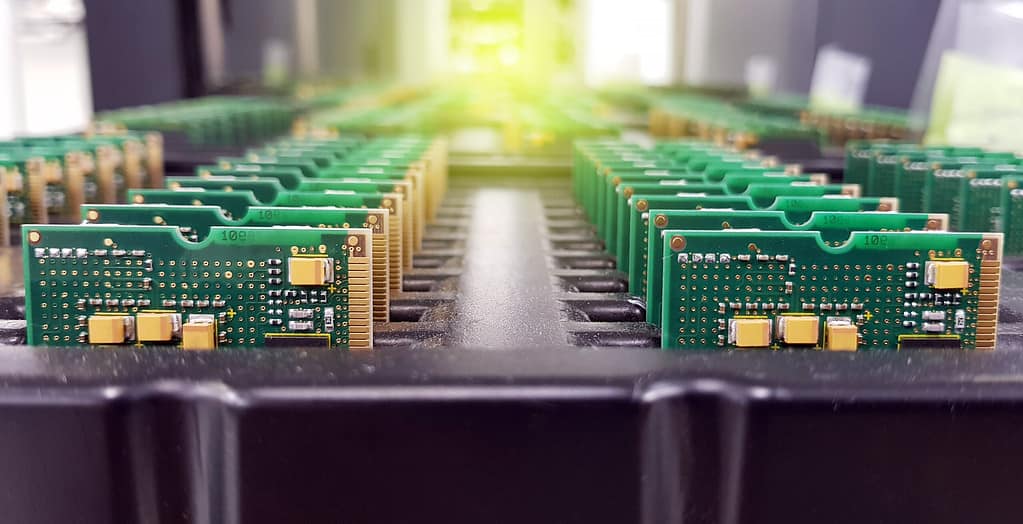
An electronics company was experiencing a higher-than-normal reject rate on one of its components. The engineering manager proposed the company create an ECR to try and rectify the problem.Â
Below are the steps they used to create an ECR and ECO:
- Identify the issue or problem that needs to be fixed
- Create an engineering change request (ECR)
- Make your business case for the proposed change by including the following:
- Expected outcomes
- Reasons for the change
- Expected costs
- Potential obstacles
- Discuss with appropriate people and teams, revise, and seek approval. Seek feedback from those you expect to participate in the change request.
- Upon approval, an engineering change order (ECO) is created
- Prepare changes and start implementing them
- Release changes
- Document changes and communicate them
- Close the change order. Upon completion, the engineering change order is closed.
- Document the results
Finally, document the changes, and their results, and communicate these results to relevant parties.
Other Useful Tools and Concepts
If you’re on the hunt for some extra tools for your organization, you’re in the right place. Understanding how natural tolerances occur and how to adjust for them is a vital part of any statistical analysis. We’ve got a guide covering the subject that explores exactly how you do so.
Additionally, understanding how a clean point factors into your production is vital. Losing customer confidence can be a massive blow to any organization. You can get back on track with a clean point, but it will take time and effort.
The image featured at the top of this post is ©Ground Picture/Shutterstock.com.