
Key Points
- FOCUS PDCA is a methodology for improving processes and solving problems.
- It allows users to maintain focus and cohesion throughout the entire methodology.
- It is a comprehensive approach, applicable to process improvement from start to finish.
PDCA (Plan-Do-Check-Act) is a popular iterative methodology to fix a problem or improve a process.
Developed and promoted by Drs. Deming and Shewhart it is a cycle of examining a problem, collecting some data, improving the process, and then monitoring it to be sure your improvement was successful. If not, you repeat the cycle.
The preceding FOCUS expands the methodology and combines it with PDCA to form a comprehensive approach to problem-solving and process improvement.
Overview
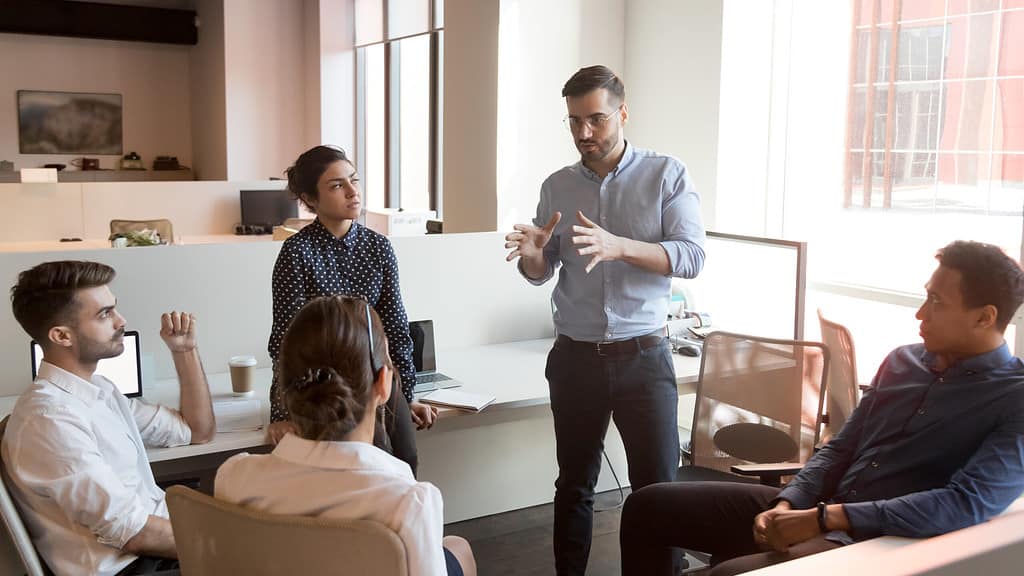
The FOCUS PDCA approach was developed for the healthcare industry. It’s an extension of the classic PDCA methodology, where FOCUS is a set of activities that precede those used in the PDCA cycle.
The components of FOCUS PDCA are:
- Find a process to improve: Sometimes the problem is obvious. Sometimes you will discover a problem using such tools as value stream maps, Pareto Diagrams, control charts, or other process tools.
- Organize a team: Your team should consist of people who are doing the process, process customers and suppliers, and those who might be subject matter experts in specific elements of the process.
- Clarify the current state of the process or problem: You need to collect data on the process so you have an objective understanding of the process rather than subjective anecdotal information. You might use the 6W approach to ask questions.
- Understand the problem: After collecting data in the step above, you will want to understand the process variation and what might be the root cause of your problem.
- Select a strategy for improvement: Using brainstorming and other solution-generating tools, you can start formulating recommendations for improvement.
PDCA with FOCUS
The PDCA, used in the context of FOCUS, is a variation of the original PDCA.
- Plan: In the standard PDCA approach, the Plan step defines the problem and a solution is developed. In FOCUS PDCA, this is done in the Select stage. In FOCUS PDCA, Plan is where you start planning for the implementation of your solution.
- Do: Collect data to characterize the condition of the process before changes are made. Then the required changes are made — that is, the plan is implemented.
- Check: Did your changes make a difference? Collect data and compare the actual results against your projected or target results. If your results were not achieved, you can go back and review the previous steps, possibly even starting at the beginning again.
- Act: Similar to Control in the DMAIC process, you will want to put things in place to “maintain the gain.”
Major Benefits
Any improvement methodology will have benefits for the organization. Some of the specific ones related to using FOCUS PDCA are discussed below.
It’s Comprehensive
The FOCUS PDCA approach starts at the beginning by identifying the problem and ends with a control plan in place to ensure your improvements don’t disappear over time.
Simplicity
Most of the tools used in FOCUS PDCA do not involve complex statistical analysis. Many are intuitive and don’t require deep analytical skills. This means almost everyone can serve on the team without worrying about whether or not they have the necessary skills. A good attitude, an openness to collaborating, and being open to change are the primary skills your team members will need.
It Provides a Framework
This approach provides a simple 9-step framework and guidelines for consistently addressing and resolving process problems.
Planning for Everything
So, why should you consider using FOCUS PDCA? There are many tools at your disposal when it comes to problem-solving. However, when you get right down to it, not many provide a total framework from start to finish. If you’re already on the ropes with defects and flaws in your production, FOCUS PDCA can help you get back on track.
Why It’s Important
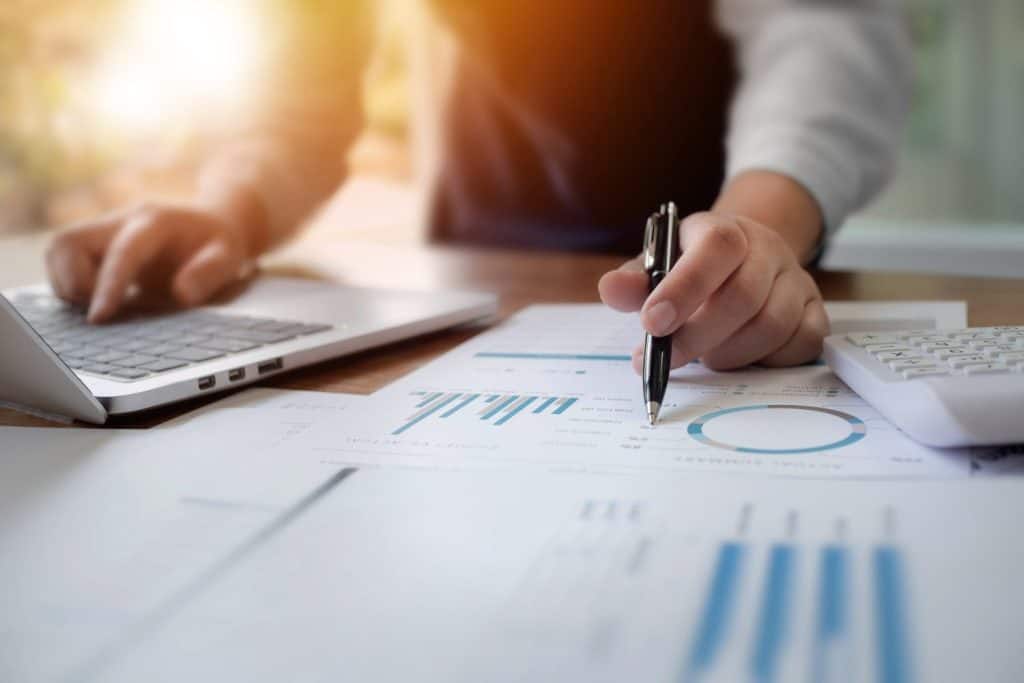
©Oakland Images/Shutterstock.com
As a simple but powerful tool for improvement, your understanding of how to use it will be beneficial both to you as well as your organization.
It Maintains Focus
As the acronym suggests, by focusing on a specific problem and using a focused problem-solving approach, you will get better results and improvements.
It Fosters Engagement
As the CFO of a well-known corporation was fond of saying, “The best ideas come from our people.” Understanding and applying FOCUS PDCA will allow you to engage a wide range of business employees and foster a culture of continuous improvement.
It Helps You Understand Your Process
The use of FOCUS PDCA forces you to gain greater insight and understanding of your process. Knowing what to do — and how to do it better — will make your organization better able to satisfy your customers.
An Industry Example
A large healthcare organization had a run of problems regarding the wrong administration of meds to patients on the hospital floor. They initially used an FMEA to explore the specific problem areas. After identifying the possible source, they formed a team to develop specific recommendations to eliminate the problem.
The team utilized the FOCUS PDCA approach to identify, define, understand, and eventually improve the process. Through the use of technology, they were able to come up with several solutions. One was the delivery of meds to the patient floor via robotic carts with a safety mechanism that prevented disbursing of the wrong med. They used a signature verification technology to prevent mistakes caused by handwritten scripts. They also implemented better drug labeling to prevent accidental administration of the wrong drug or wrong dosage.
Best Practices
Like any improvement method, there is the right way to use it and a not-so-right way to use it. Here are some suggestions for the right way to do it.
Involve the Right People
Select your team based on the people who are the most effective at solving a particular problem. Don’t necessarily rely on volunteers, but hand-select those you feel have the right skills and knowledge to make maximum contribution to the team.
Avoid Coming in With a Solution
The purpose of FOCUS PDCA is to fully understand the nature and root causes of the problem. The solution will result from that deep understanding. Don’t come in with preconceived notions of root causes and solutions. Trust the process of FOCUS PDCA.
Communicate
Frequent communication will prevent many surprises. Keep in close communication with the appropriate level of management, important stakeholders, and other people involved in the process.
Other Useful Tools
Are you looking to bolster your Six Sigma knowledge? Well, you’re in the right place when it comes to getting up to speed with new concepts and tools. One way you can nip problems in the bud before they happen is by using an MSA test. These tests are intended to check for the reliability of your measurements and can help ensure total accuracy.
Additionally, if you need some number-crunching power-ups, you might want to learn all about the Kruskal-Wallis test. This is a non-parametric test that is readily used with your real-world data. If you’re looking for the differences in sample sets, this is the way to go.
Summary
PDCA is a common tool for solving problems and improving processes. The healthcare field expanded the approach by adding five preceding activities they referred to as FOCUS.
In total, the FOCUS PDCA approach is a powerful yet simple method for addressing a business problem, and through the active involvement of your people, you can identify and implement improvement solutions at your organization.