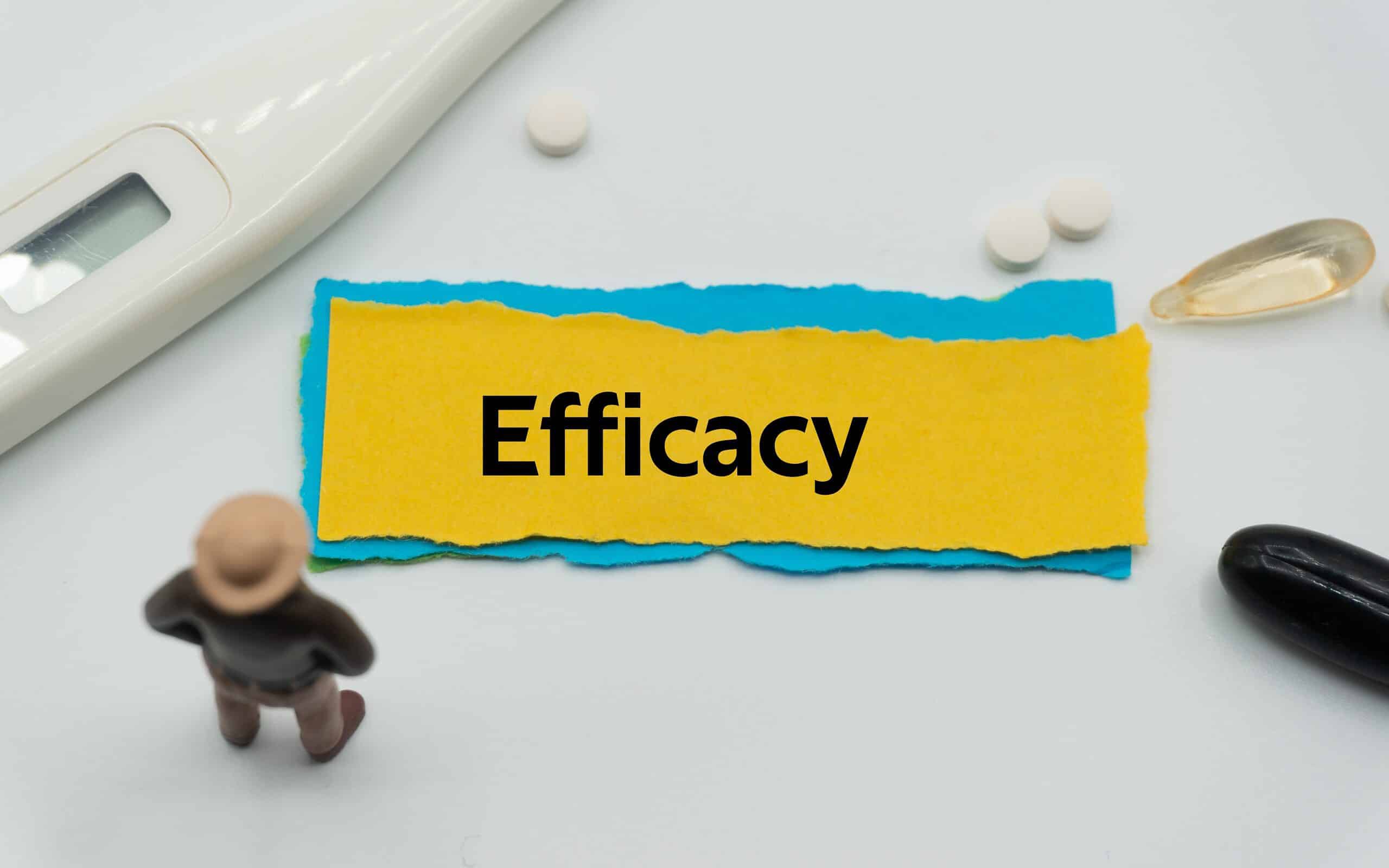
Efficiency and effectiveness are vital elements of any successful organization, but in the realm of Lean Six Sigma, there is another crucial concept that holds the key to achieving optimal results: efficacy. Efficacy goes beyond simply measuring efficiency or effectiveness; it encompasses the ability of a process or methodology to consistently deliver the desired outcomes while minimizing waste and defects.
Overview: what is efficacy?
Efficacy, in the context of Lean Six Sigma (LSS), refers to the ability of a process or methodology to produce the desired results consistently. It signifies the effectiveness and efficiency of the approach in achieving specific objectives. In essence, efficacy measures how well a process performs in delivering value and meeting customer expectations while minimizing waste and defects.
3 Benefits to efficacy
Although there are some potential drawbacks to consider when it comes to efficacy – for example, the complexity of measuring accurately and subsequent difficulty in establishing universal benchmarks – the benefits that come from successful implementation are worth pursuing.
1. Efficacy enables organizations to identify and focus on the critical factors that directly impact the desired outcomes.
By understanding the efficacy of different processes, teams can allocate resources efficiently and streamline efforts toward areas that yield the most significant improvements.
2. Efficacy helps in establishing realistic goals and benchmarks.
This allows organizations to track progress accurately and make data-driven decisions.
3. Efficacy fosters a culture of continuous improvement.
This culture results in a clear understanding of the impact of process changes and encourages experimentation and innovation.
Why is efficacy important to understand?
Understanding efficacy is crucial for organizations practicing Lean Six Sigma. It provides a systematic approach to process improvement, ensuring that efforts are aligned with strategic goals and customer expectations. By grasping the concept of efficacy, organizations can make informed decisions regarding resource allocation, prioritize improvement projects effectively, and track progress accurately.
Efficacy serves as a guiding principle that drives continuous improvement and enables organizations to deliver exceptional quality while reducing waste and defects.
An industry example of efficacy
Let’s consider a manufacturing company that implements Lean Six Sigma methodologies to enhance its production process.
By analyzing the efficacy of various stages within the manufacturing line, they identify a bottleneck that significantly slows down production. Through process optimization and waste reduction initiatives, the company successfully improves the efficacy of that particular stage, resulting in increased throughput and reduced cycle time. This example showcases how efficacy assessment can pinpoint areas for improvement and lead to tangible benefits for organizations.
3 Best practices when thinking about efficacy
When it comes to understanding and improving efficacy in Lean Six Sigma, adopting best practices is crucial. These practices provide a framework for organizations to maximize the effectiveness of their processes and achieve consistent, desirable results.
1. Define clear objectives.
Clearly articulate the objectives and desired outcomes of a process or improvement project. This clarity enables teams to measure efficacy accurately and align their efforts accordingly.
2. Collect and analyze relevant data.
Gather relevant data points to measure efficacy accurately. Use statistical tools and data analysis techniques to interpret the data effectively and identify areas for improvement.
3. Consider the entire value stream.
When evaluating efficacy, take a holistic approach by considering the entire value stream. Look beyond individual processes and analyze the interdependencies between various stages to identify opportunities for optimization and eliminate bottlenecks.
Frequently Asked Questions (FAQs) about efficacy
Is efficacy the same as efficiency in Lean Six Sigma?
Can efficacy be improved in service-oriented industries?
How often should efficacy be assessed?
The efficacy mindset
The journey towards efficacy is not without its challenges, but the rewards are worth the effort. With each improvement project, organizations inch closer to streamlined processes, reduced waste, and enhanced customer satisfaction. As you embark on your Lean Six Sigma journey, remember that efficacy is more than just a measure. It is a mindset, a commitment to continuous improvement, and a dedication to delivering value to customers. By embracing efficacy, you can chart a course towards operational excellence, transforming your organization and remaining competitive in an ever-evolving business landscape.