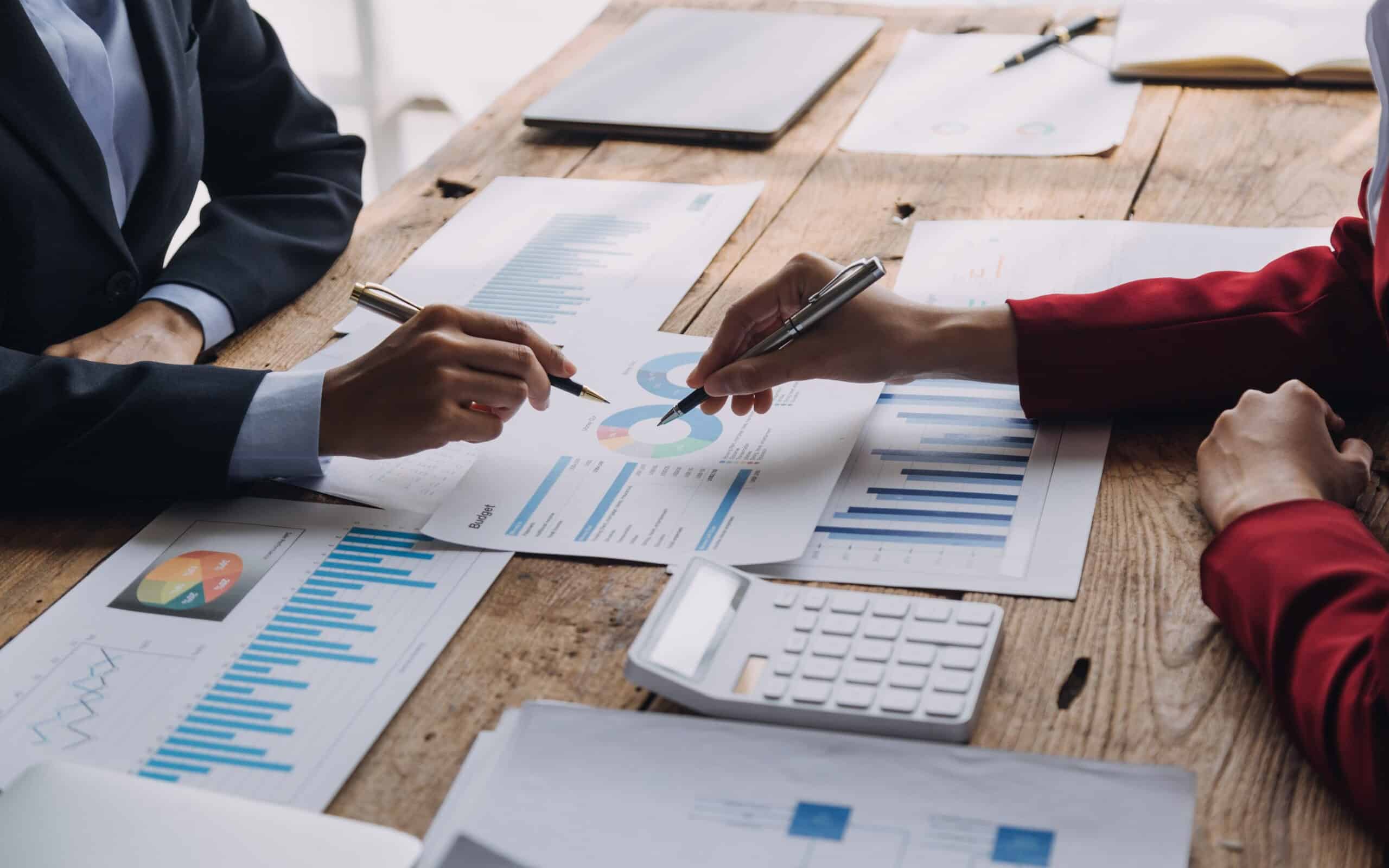
Key Points
- Cpk is a means of calculating your process’s capability.
- It can be used to compare the performance of departments in your organization.
- You can also utilize the calculation to determine if defects are present in production.
Cpk is a common measure used in process capability analysis that allows you to know how well your process is meeting your customers’ expectations and specifications. This article will explain how Cpk is calculated and interpreted.
We will explore its application, and benefits and provide some tips and best practices so that you can begin assessing how well your process is doing when measured against the requirements specified by your customer.
Overview: What Is Cpk?
Process capability is the quantifiable comparison of the Voice of the Customer (specs, requirements, or expectations of your customer) and the Voice of the Process (control limits). The goal of process capability is to come up with a quantified measure that informs you as to whether you are meeting your customer expectations or not as well as a relative value of how well you are meeting or how badly you are missing.
Besides Cpk or Capability Index, there are several other process capability metrics. They are Cp, Pp and Ppk. Since Cp and Cpk are related, we will need to spend a little time talking about Cp before discussing Cpk to provide context for Cpk.
Defining Cp
Cp, or capability potential, is a measure of the potential capability with the assumption that the distribution of the sample process data is normally distributed and centered within the customer’s upper specification limit and lower specification limit. It represents the best the process capability can be for the specs and process distribution. If there is only a one-sided spec, then Cp cannot be calculated. The formula is:
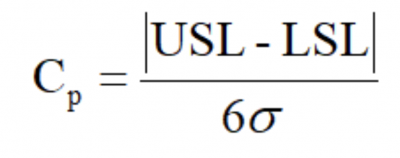
You can say this as Cp is equal to the Customer’s Upper Specification Limit minus the Lower Specification Limit divided by 6 standard deviations.
We are assuming that the sample distribution is normally distributed, and its width is calculated by adding and subtracting 3 standard deviations on either side of the sample data mean. The standard deviation that is used is called a “pooled standard deviation” or “within variation.”
Things to Note About Cp
Cp can take on values equal to 1, greater than 1, or less than 1. Therefore, if we look at the formula above, a value of 1 would mean that the width of the distribution is equal to the width of the specifications or specs.
A value greater than 1 would mean that the specs are wider than the distribution of the process, so we are comfortably within spec. If the value is less than 1, it means that the width of the process distribution is wider than the specs, and items will be outside the specs.
However, all of this assumes that the process is centered within the specs. But this is rarely the situation. More often than not, the process mean (x-bar) will not be centered within the specs. Interestingly, if the process mean is off-center, the Cp will still be the same since the Cp does not consider the location of the process. That’s when we need to use the Cpk to assess the process capability.
How It Differs From Cp
Cpk is similar to Cp in that it utilizes the customer specs and process variation, as measured by the standard deviation, but it also includes the location of the mean relative to the specs. Since the process mean is now off-center, you will report the minimum condition depending on whether the process has shifted closer to the upper spec or closer to the lower spec.
Essentially what you are doing is measuring the distance from the mean to the different specs. Then you divide that distance by half the width of the distribution or 3 standard deviations. Finally, you report out the minimum of the two values since that will be your “worst” condition and lowest process capability. See the formula below.
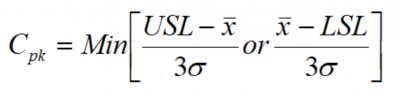
The value of the Cpk ratio can take on any value ranging from 0 to any positive or negative number. A value greater than positive 1 means that the spec limit is far enough away that the process should be capable and be within specs. A value of 0 means that the mean of the distribution sits on the spec so that half the process will be out of spec. A negative value means that the process mean is beyond the spec, resulting in more than 50% of the process being out of spec.
In most business applications, you want the minimum Cpk value to be 1.33. This means the closest spec is 4 standard deviations away from the mean. If staying in the spec is critical, then the preferred value is 1.67, meaning the closest spec is 5 standard deviations away. Finally, if the value of Cpk is 2, then the closest spec is 6 standard deviations. This is the definition of Six Sigma, and you can then claim that you have a Six Sigma process.
Benefits of Cpk
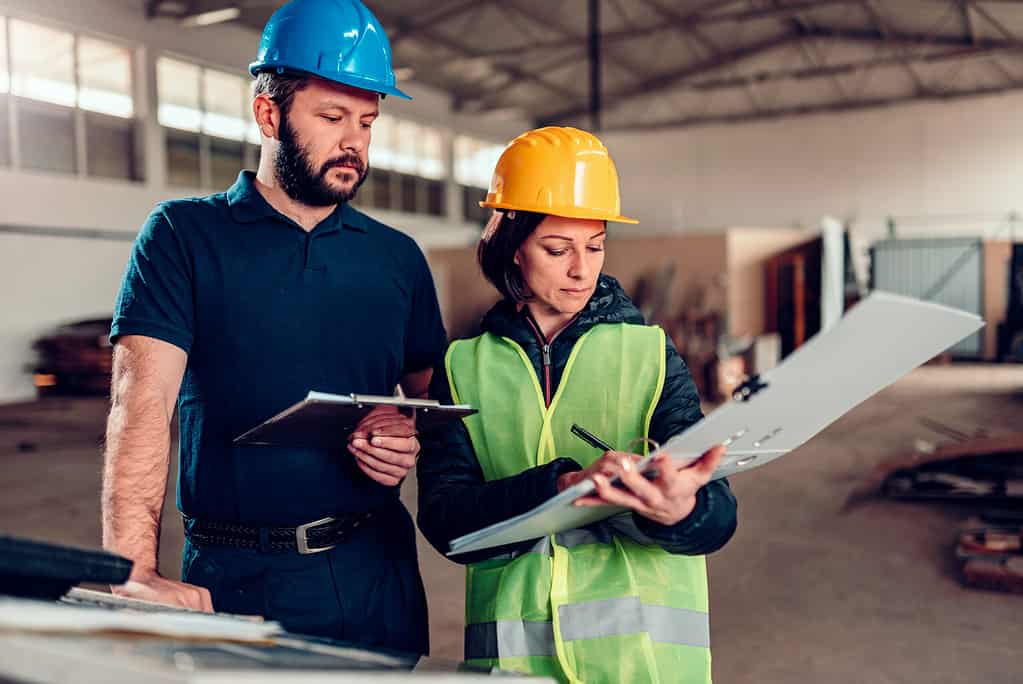
Cpk is a simple and useful metric for comparing your process with your internal or external specifications, targets, expectations, or any other desired outcome for your process.
Simple, But Powerful Calculation
To compute your Cpk value, you only need to know the mean and standard deviation of your data and the specs you want to test against.
Can Account for a Process Not in Spec
If the process is centered within the specs, you would use the calculation of Cp to assess the potential of your process capability. But, as it is in most cases if the process is shifted off-center, then the Cpk will account for that shift.
It Can Compare Processes
The Cpk allows you to compare the performance of disparate functions since it is a generic measure of the process’s ability to meet specs. If a manufacturing line had a Cpk of 0.82, and a finance department had a Cpk of 1.89, you could say that finance is doing a better job of meeting its customer’s requirements than manufacturing.
Why Does Cpk Matter?
As with any index, understanding its use is crucial to guaranteeing future success. Cpk is a valuable calculation due to its sheer versatility. Compared to Cp, you’ve got a more robust means of comparing disparate sources like departments in your organization. Further, knowing how a process is performing is vital regardless of the stage in the project cycle.
Why Is Cpk Important to Understand?
Meeting your customer’s expectations and requirements is vital to your organization staying in business. By understanding how to compute Cpk and interpret its value, you will be able to know what you have to do to meet — and possibly exceed — your customers’ expectations.
Know What Variables Are Needed
If you intend to use Cpk for decision-making purposes, you need to know what variables are needed and what their values are so you can do the proper calculations.
It Represents Your Current Process
If your Cpk is not high enough to satisfy your customers’ specs, you need to take action so that out-of-spec products are not produced and shipped.
You Might Want to Adjust Your Specs
If you’re not meeting specs, you might want to speak with your customer to see if they can be adjusted without any negative impact. You can use the current Cpk calculation to back into what level of specs you’re able to meet.
An Industry Example
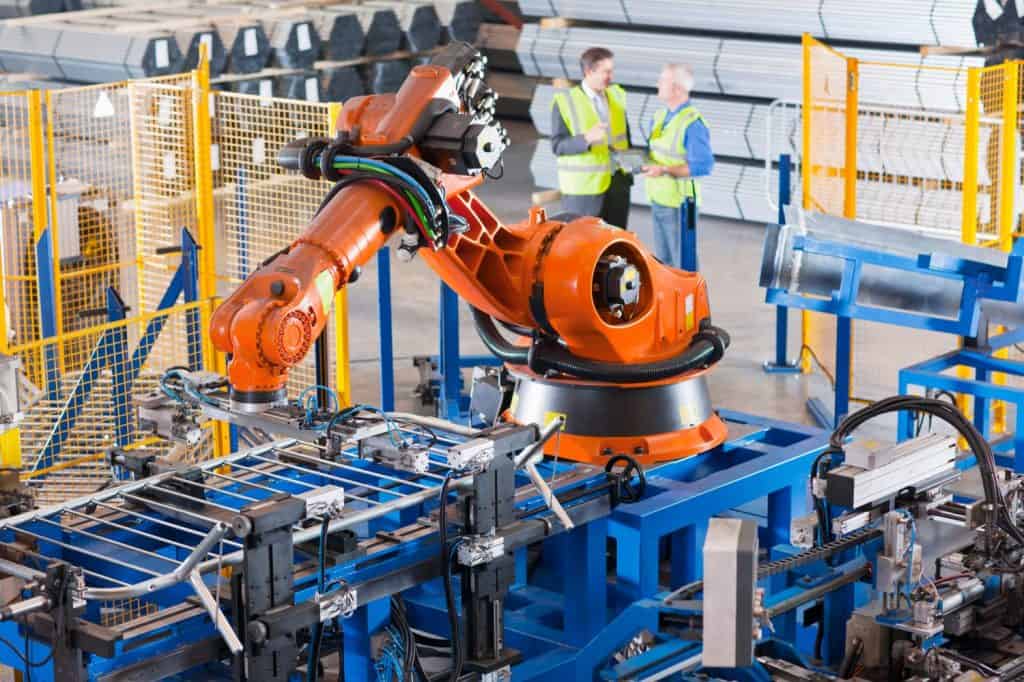
©Juice Flair/Shutterstock.com
A plastic extrusion company had contracts with major suppliers of plastic parts to the auto industry. The owner, Norman, was an advocate of Lean Six Sigma and had improved their processes as well as invested in the best equipment available. His customers had rigorous specs because their customers, the auto companies, had rigorous specs for them.
Upon calculating the Cpk for his extrusion process, Norman found that his equipment was capable of achieving a Cpk of 4 consistently. He was sure that his competitors were nowhere as good. Because he was so tight and centered on the customers’ specs, he decided to launch a two-pronged strategy to improve sales and profits.
The first strategy was to approach the customers and suggest they tighten their specs for his products. Using the Cpk formula he backed into how much tighter the specs could be made and still be well within them. Knowing his competitors, Norman figured that if the specs were made tighter, his competitors would no longer be able to produce products at a competitive price or quality. That meant Norman would get a bigger share of the total business.
His second strategy was based on how tight he was within the specs, even the tighter ones. He realized that he did not need to stay centered within the specs. Therefore, he adjusted his equipment to produce off-center and closer to the lower spec while still staying well within spec. This allowed him to reduce the amount of plastic in each part, therefore saving a small amount of money on each part. Since he was producing parts in the millions, the small increment of savings would add up to a significant increase in profits. A win-win all the way around.
Key Suggestions
Cpk is merely a calculation, but there is a series of hints that can allow you to get the maximum value out of the calculation.
Do Cp and Cpk Calculations
By comparing the potential capability with the actual capability, you will understand what, if anything, you need to do to be sure you remain in spec.
Use Cpk to Compare Different Parts of the Organization
The use of the generic Cpk metric allows you to compare various functions in the organization. It’s a measure of how well each is doing relative to their specs and allows for an apples-to-oranges comparison.
Establish Strategies to Capitalize on Good Value
You can consider revising specs or shifting the mean of the process within the specs to take advantage of a good process and high Cpk.
Other Useful Tools and Concepts
If you’re after other ways to fulfill customer needs and expectations, you’re in the right place. One of the easiest ways to meet your goals is by defining CTQ outputs. These parameters are specified at the start of the design phase and pay close attention to the goals of the VOC to deliver high-quality deliverables.
Additionally, learning how the voice of the customer can influence the customer experience is paramount. While there are many voices to pay attention to throughout the production process, VOC is arguably one of the most important.
Conclusion
Cpk is a common measure of a process’s ability to meet customer expectations — primarily specifications. It assumes that the process data is normally distributed but does not require that the mean of the process be centered if there are upper and lower specifications.
It is calculated by finding the difference between the mean of the process and a spec. That difference is then divided by 3 standard deviations. The higher the value is, the better the process capability.
The knowledge and understanding of your Cpk value can be a powerful strategy tool for gaining competitive advantage and improved profitability. It can be used for any process with stated specs or qualitative expectations and can be used as a comparative tool across different functional areas.