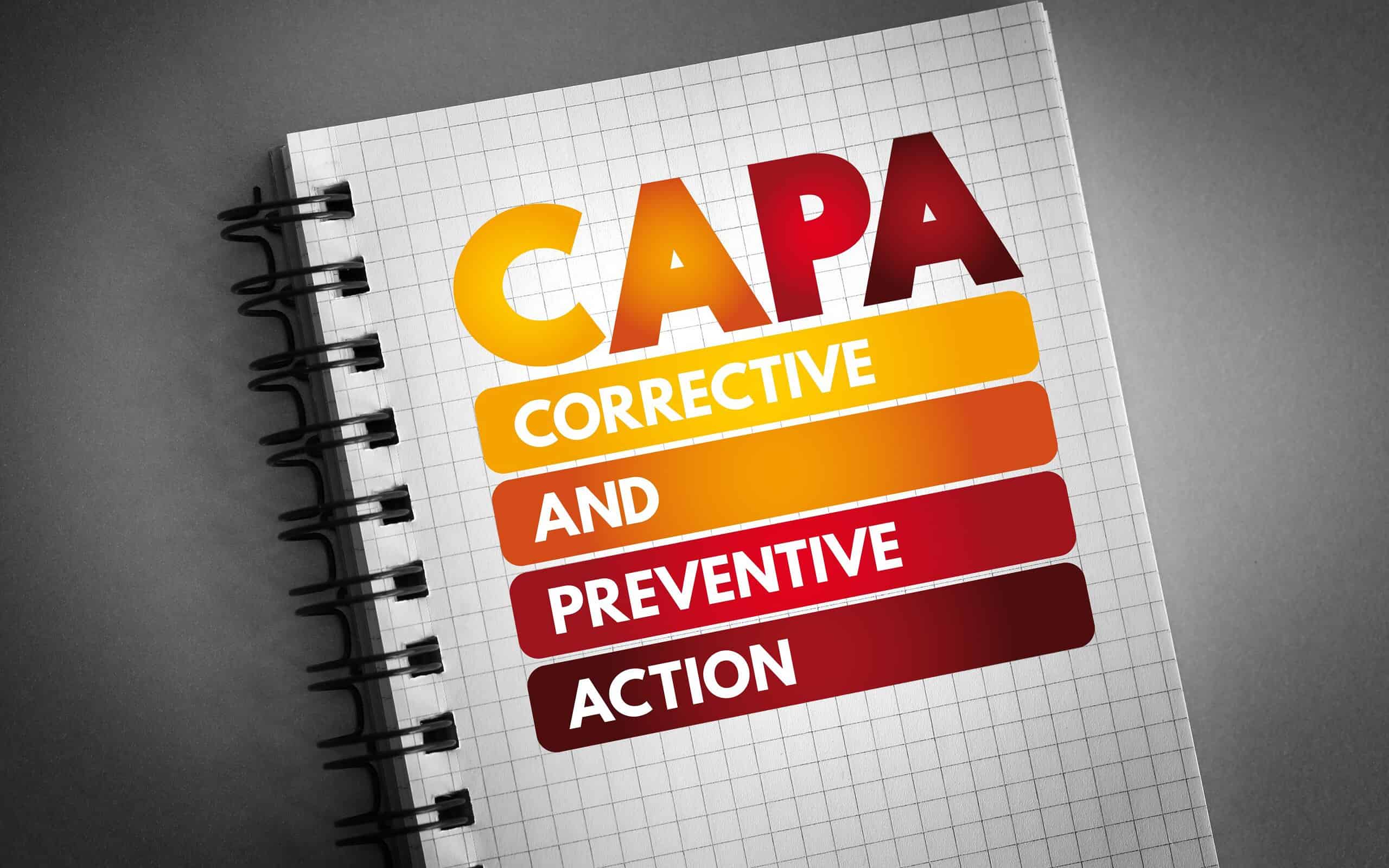
Often organizations do a root cause analysis after a problem has occurred. Is there something you can do as a preventive action prior to something happening. Let’s learn more about CAPA.
Corrective and Preventive Action (CAPA) is a systematic approach used in various industries, including manufacturing, healthcare, and quality management, to identify and address the root causes of problems and prevent their recurrence. CAPA is an essential component of quality management systems and is often required for compliance with regulatory standards, such as ISO 9000.
Overview: What is CAPA?Â
Here’s a breakdown of the key elements of CAPA:
- Problem Identification – CAPA begins with the identification and documentation of a problem or nonconformance. This can be done through various means, such as customer complaints, internal audits, quality control checks, or other forms of monitoring.
- Root Cause Analysis (RCA) – Once a problem is identified, a thorough investigation is conducted to determine its root cause(s). RCA techniques like the 5 Whys, fishbone diagrams, or fault tree analysis may be employed to delve deeper into the underlying factors contributing to the issue.
- Corrective Action – Corrective actions involve implementing measures to address the root cause of the problem. These actions aim to eliminate or mitigate the identified issue. Corrective actions can include process changes, equipment repairs, retraining employees, or revising procedures.
- Preventive Action – In addition to addressing the immediate problem, CAPA also focuses on preventing similar issues from occurring in the future. Preventive actions involve implementing proactive measures to identify and eliminate potential causes of problems before they happen. This can include process improvements, employee training, enhanced quality controls, or changes in design or materials.
- Documentation and Verification – Throughout the CAPA process, it is crucial to document all steps taken, including the problem description, root cause analysis, corrective actions, and preventive actions. This documentation serves as evidence of compliance and provides a reference for future evaluations. Furthermore, the effectiveness of the implemented actions should be monitored and verified to ensure that they have effectively resolved the problem and prevented its recurrence.
- Continuous Improvement – CAPA is closely tied to the concept of continuous improvement. By addressing problems and preventing their recurrence, organizations can enhance their overall quality and efficiency. Lessons learned from the CAPA process can be used to improve processes, systems, and procedures across the organization.
An industry example of CAPA
Problem: The company has been receiving customer complaints about a specific product’s packaging being damaged during transit, leading to product loss and customer dissatisfaction.
- Problem Identification – The company’s quality control team receives multiple customer complaints regarding damaged packaging.
- Root Cause Analysis (RCA) – The team conducts a root cause analysis and identifies that the packaging material used is not strong enough to withstand the transportation process, resulting in damage.
- Corrective Action – The company decided to address the immediate problem by changing the packaging material to a stronger and more durable alternative. They communicate this change to the packaging supplier and implement the new packaging material in the production process.
- Preventive Action – To prevent similar packaging issues in the future, the company decides to conduct a thorough review of its packaging specifications and requirements. They collaborate with the packaging supplier to assess the suitability of different materials, conduct packaging tests, and establish updated packaging standards that ensure product protection during transit.
- Documentation and Verification – The company documents the customer complaints, the RCA findings, and the implemented corrective and preventive actions. They also established a monitoring system to track future customer complaints related to packaging damage. Regular audits and inspections are conducted to verify the effectiveness of the new packaging material and adherence to updated packaging standards.
- Continuous Improvement – The company uses the lessons learned from this CAPA process to continuously improve its overall packaging process. They proactively review other products’ packaging, assess potential risks, and implement preventive actions, such as enhanced packaging design, additional protective measures, or improved packaging handling procedures.
Frequently Asked Questions (FAQ) about CAPA
Here are some frequently asked questions about Corrective and Preventive Action (CAPA):
What is the difference between corrective action and preventive action?Â
Corrective action is taken to address an existing problem or nonconformance, focusing on resolving the root cause and preventing its recurrence. Preventive action, on the other hand, aims to identify and eliminate potential causes of problems before they occur, thus preventing future issues.
Why is CAPA important?Â
CAPA is important because it helps organizations improve their quality management systems, enhance customer satisfaction, and ensure compliance with regulatory standards. It provides a systematic approach to problem-solving, root cause analysis, and prevention of recurring issues.
How can the effectiveness of CAPA be measured?Â
The effectiveness of CAPA can be measured by monitoring key performance indicators (KPIs) related to the identified problem. This can include tracking the recurrence of similar issues, monitoring customer feedback and complaints, assessing process or product quality metrics, and conducting internal audits or inspections.
Can CAPA be applied in non-manufacturing industries?Â
Yes, CAPA principles can be applied in various industries beyond manufacturing. It is widely used in healthcare, pharmaceuticals, information technology, aerospace, automotive, and other sectors where quality management is important. The specific implementation may vary based on industry-specific requirements and regulations.