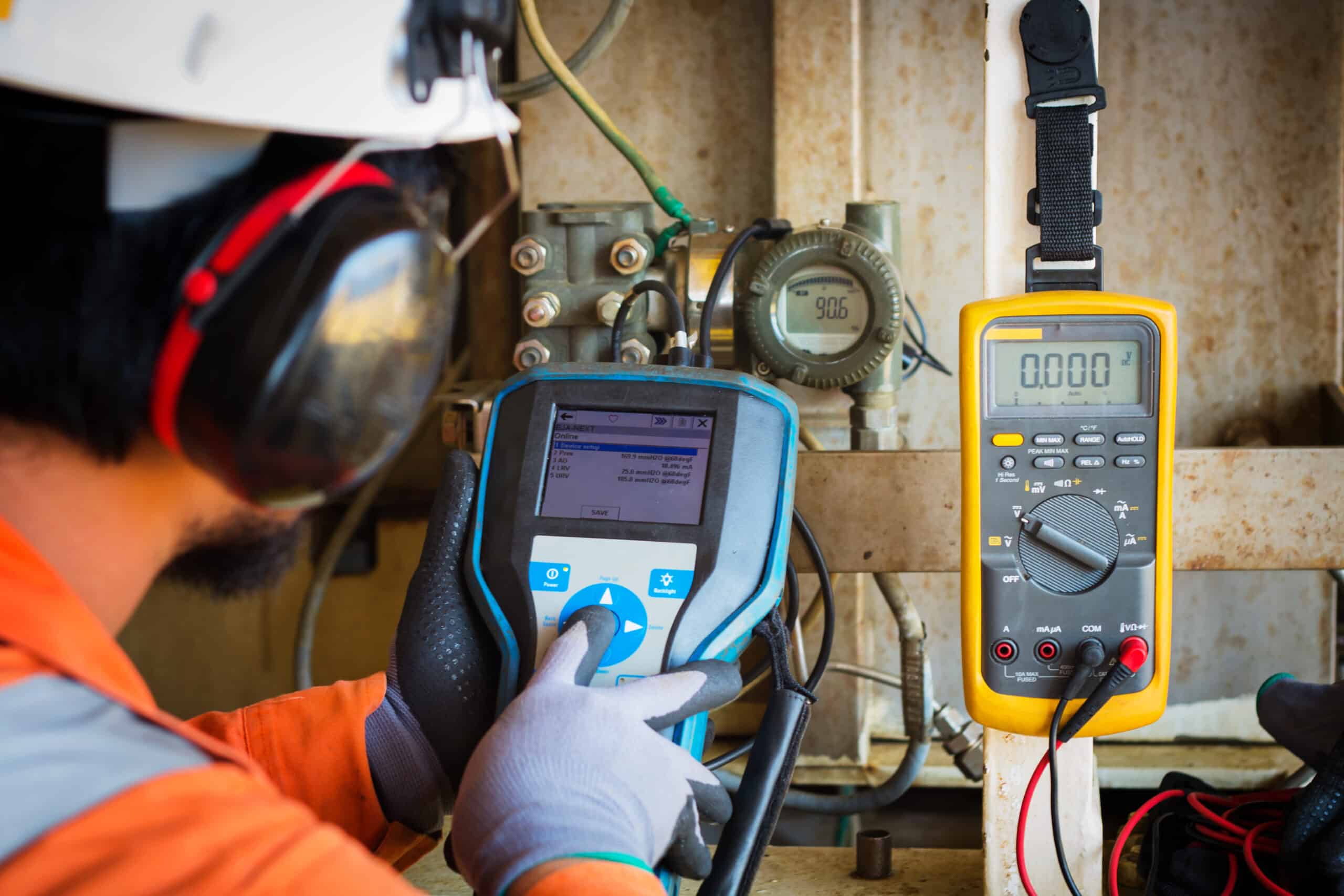
You can’t trust a new clock if it hasn’t been calibrated by comparing and changing it to global standard time first. The concept of calibration has become fundamental in most production and manufacturing environments, especially with digital devices. Companies need to improve and streamline their calibration strategy if they want to effectively embrace lean manufacturing principles.
Overview: What is calibration?
Calibration is a basic concept that has been broadened into an entire field of business management called Measurement Systems Analysis (MSA). Both production and quality control processes can involve the testing of dimensions, functionality or durability. All of these tools and processes need to be calibrated regularly to maximize positive results.
3 benefits of calibration
Calibrating tools and equipment helps ensure accuracy and efficiency in the overall operation.
1. Reduce variability
Adopting a more thorough and proactive policy regarding calibration of company equipment can significantly reduce variability. The benefits of this reduction ultimately depend on the potential risks and consequences of product defects in the first place. Over-calibration isn’t always worth the cost for some processes.
2. More useful data
The value of data depends on its detail, accuracy and relevance. Companies that calibrate their equipment and processes are reducing the impact that these errors have on workflow. This makes it easier for analysts to spot other important trends or patterns that could lead to meaningful improvements.
3. Better reputation
There’s something to be said for quality. Even if a company is willing to replace defective units purchased by customers, this doesn’t always make up for the experience of purchasing a faulty item. Calibration is the key to quality and quality is something customers will recognize.
Why is calibration important to understand?
Company leadership needs to understand the relative importance of calibration and how to prioritize it alongside other major considerations.
Measuring and six sigma
Measuring is one of the first parts of six sigma’s DMAIC action plan. Since calibration and measurements go hand-in-hand, it’s something business leaders definitely need to know about.
Overall process variability
It’s important to keep things in the right perspective. Calibration is just one of the ways that companies can cut down on variability, so it shouldn’t take on more significance than the process itself.
Defining acceptability
Any serious discussion about calibration also necessitates a conversation about defining defects. There is always a point where the variation is enough for the product to be defective, but it’s not always easy to tell where the line is. Calibration procedures should support this decision, not direct it.
An industry example of calibration
An electronics manufacturer produces a range of digital fitness products that help users track their vitals and exercise statistics each day. Since each of these items contains several types of sensors that are all integral to basic product features, they must be tested to reduce defect rates on the retail end.
The company has several ways to handle this challenge. They could do real tests with actual human beings and compare the results with calibrated devices. The company could also engineer a testing station designed to properly trigger sensors and detect errors. Either case could be considered effective calibration, but might have drastically different costs and results.
3 best practices when thinking about calibration
For six sigma practitioners, calibration is a gateway to several practices that can benefit any organization.
1. Ongoing optimization
Calibration and optimization are exercises in patience. It’s all about establishing a pattern of ongoing, cyclical improvement. It may not be dramatic and exciting, but it is consistent and effective.
2. Set the standards
People only care about calibration if there are real standards in the workplace. It’s not something you can do casually. Quality standards are seen in the products, but they begin with the people. Help team members understand and appreciate the value in what they are doing.
3. Invest in training
Even if you have the best equipment out there for calibrations, it won’t do much good if employees are unable or unwilling to use it right. Invest in training and get people onboard with these practices.
Frequently Asked Questions (FAQ) about calibration
How do you conduct calibration?
The answer to this question is completely dependent on the demands of the situation. Ultimately, you need to hold the subject up to a more trust-worthy standard to see if it gives the same readings or results.
What is social or team calibration?
The concept of calibration can be applied to people in a social setting by deliberately setting a group dynamic rather than let one naturally develop. This can be a very effective way to avoid unproductive friction and create more room for collaboration.
How does calibration relate to smart devices?
Smart devices need to be calibrated just like old-fashioned scales and thermometers, it’s just a lot more complicated to do so. Calibrating electronic devices quickly and effectively requires intimate understanding of the production process and product capabilities.
Keep up on calibration
Calibration isn’t a chore or an obstacle to overcome. It’s an opportunity to make production processes more efficient and less variable, which are among the chief goals of six sigma practices. Calibrating equipment, processes and products keeps companies in control of their processes and opens up the opportunity to improve them.