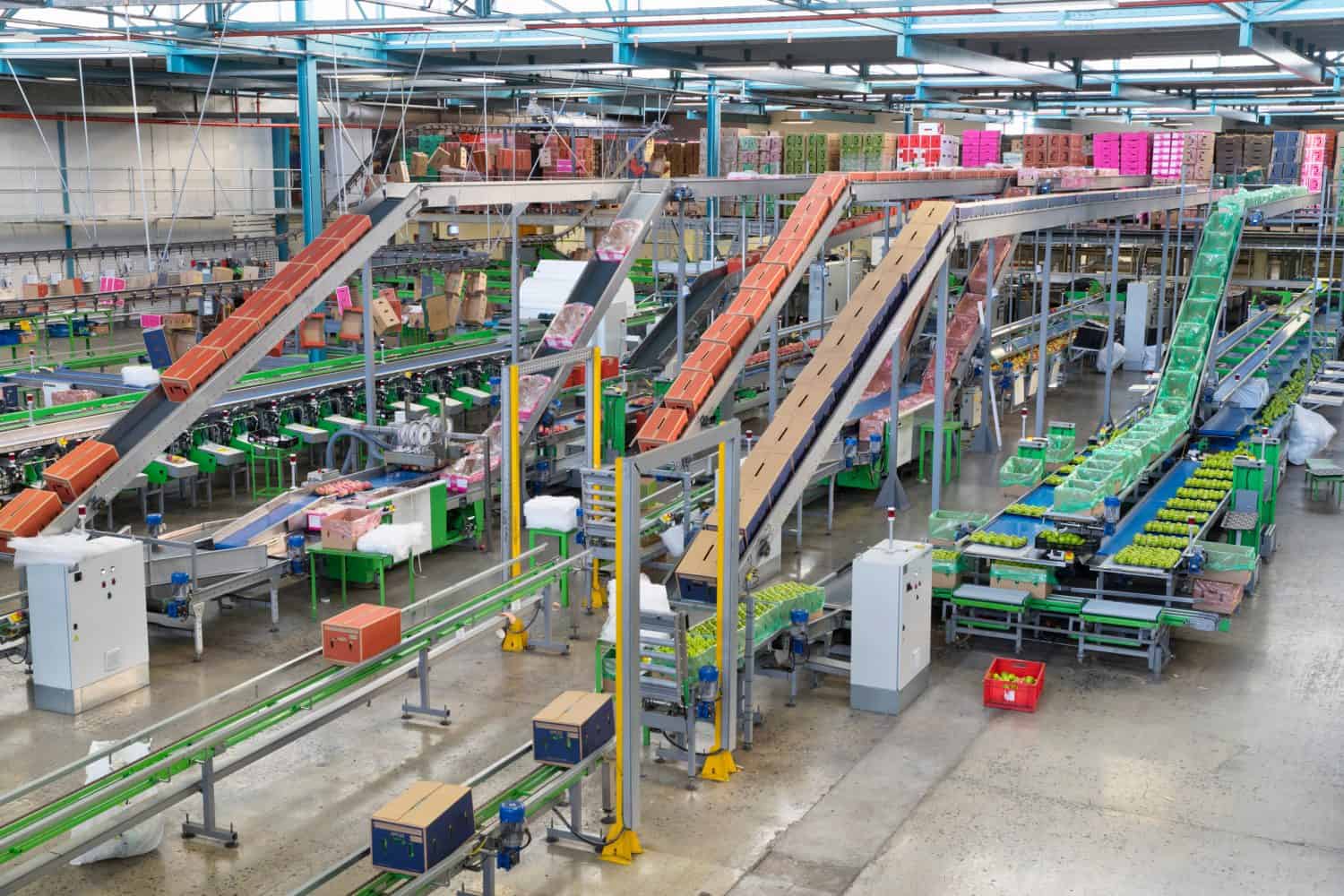
© Juice Flair/Shutterstock.com
Key Points
- The clean point is the first product off the line to meet customer satisfaction after the remediation of defects.
- It can be expensive to reach this point, interrupting production.
- The benefits of it allow you to see the reliability and precision of your production line.
Overview: What is the Clean Point?

In a manufacturing environment, the clean point is the first output after a quality issue has been discovered and remedied. It is the signifier for the point where the product is again acceptable for customer satisfaction.
3 Drawbacks of a Clean Point
While it is necessary to halt production if an item is not meeting customer standards and fixing processes becomes paramount, it can be a large expense. It is a better strategy and can cost a fraction of the cost of implementing more error-preventive mechanisms at the onset.
1. Diminished Customer Confidence
Even if you get production back on track and can present customers with items from a clean point and they are satisfied with their merchandise going forward, the hiccup will always be in the back of their minds. This is bad for your business in that an element of trust has been breached. Customers will be less tolerant should even unrelated issues arise in the future.
2. Excessive Costs
It is extremely expensive to stop everything in the middle of production to rework a design. You have everything from the cost of diverting the workforce to help address the problem, the loss associated with having to dump the defective goods,
3. Employee Disengagement
Having to stop the production of an item, make the necessary fixes, and do the work all over again is bound to create some employee frustrations. This could cause some disengagement amongst your staff.
Why Is a Clean Point Important to Understand?
Having a record of exactly where an improvement was made in production to show that an issue has been resolved is extremely important for a few reasons:
1. Tracking the Durability of Machines
Being able to know when exactly in a production run a defective item had been addressed and remedied is important to gauge the long-term durability of your machine processes.
2. Maintaining Relationships
Being able to show a customer that the issue that caused the product to not meet standards has been rectified is imperative to keep that customer and smooth the business relationship.
3. Tracking the Long-term Health of Your Business
There will be a myriad of costs associated with halting production and making changes. It is important to be able to accurately track how the changes improved business and also know when the associated costs were recovered.
4. Test the Validity of Your Process Improvement
While process improvement can seem successful, the clean point is going to the litmus test as to whether those improvements have stuck. As such, it pays to keep a close eye on your production line to ensure whatever steps you have taken are successful.
An Industry Example of a Clean Point:
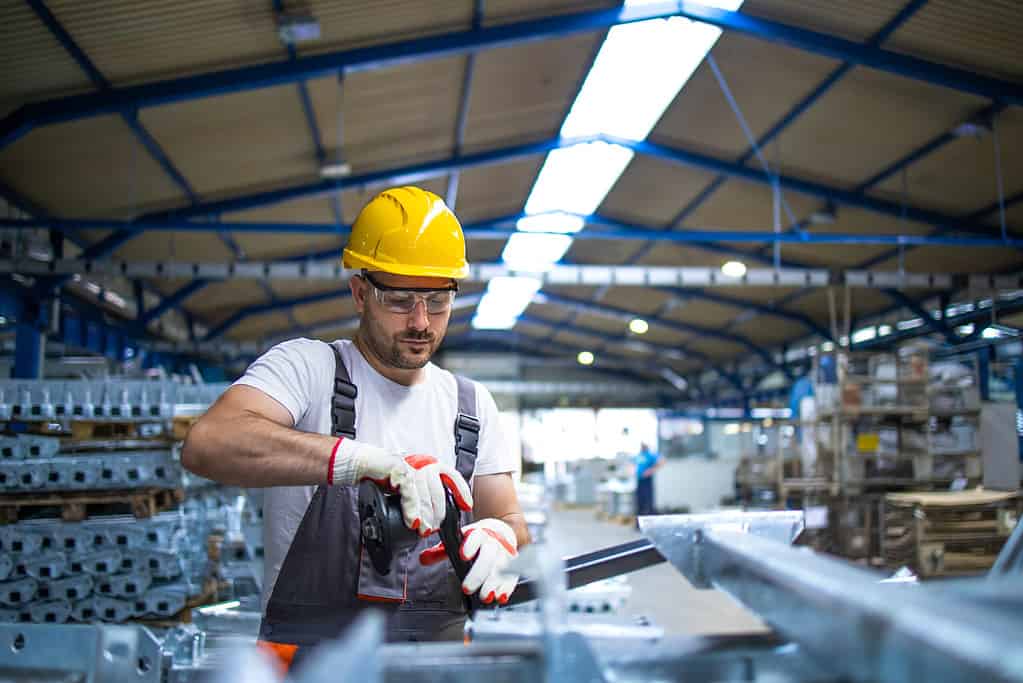
A record plant is tasked with making 10,000 copies of the latest Adele album for Columbia Records. Some test pressings are sent to the label, and the quality control department at Columbia finds that the vinyl has been poorly mastered by the plant.
The coming shipment is deemed unacceptable. The plant makes the needed changes in the production, a clean point is established, and a new test pressing from the clean point is sent to Columbia. The run continues as planned.
3 Best Practices When Thinking About a Clean Point
There are several practices to keep in mind when thinking about a clean point. Here are a few:
1. Invest in Preventative Measures at the Onset
Investing in prevention costs that prevent issues from occurring during production is a much cheaper option than having to halt production, address an issue, and start again.
2. Make Sure the Fixes Are Not Just Temporary
If you have to halt production due to an issue, be sure to establish processes and remedies that are not just quick fixes but can continue working over the long term to prevent further issues from arising.
3. Avoid Further Erosion of Customer Trust
Keep in mind that even if you have solved the problem, your customer’s confidence has been affected. It may take a long time and many uninterrupted runs for customer confidence to completely return.
Other Useful Tools and Concepts
If you’re on the hunt for other useful tips and tricks, you’re in the right place. While there are many metrics for gauging process capability, few are as universal as the Z bench. Our guide covers how it works, and also marks the differences between things like Cpk and Sigma.
Additionally, understanding and implementing replicates in your DOE can see great results on the whole. You’ll want to learn how to best implement these to make the most of your production, especially when testing for changes or precision.
Keeping Customers Happy With a Clean Point
Remember, while you may run into a situation where halting production, fixing your processes, and giving your customers their products from a clean point may allow you to finish the run, preventative measures done ahead of time are a much more inexpensive business strategy.
The image featured at the top of this post is ©Juice Flair/Shutterstock.com.