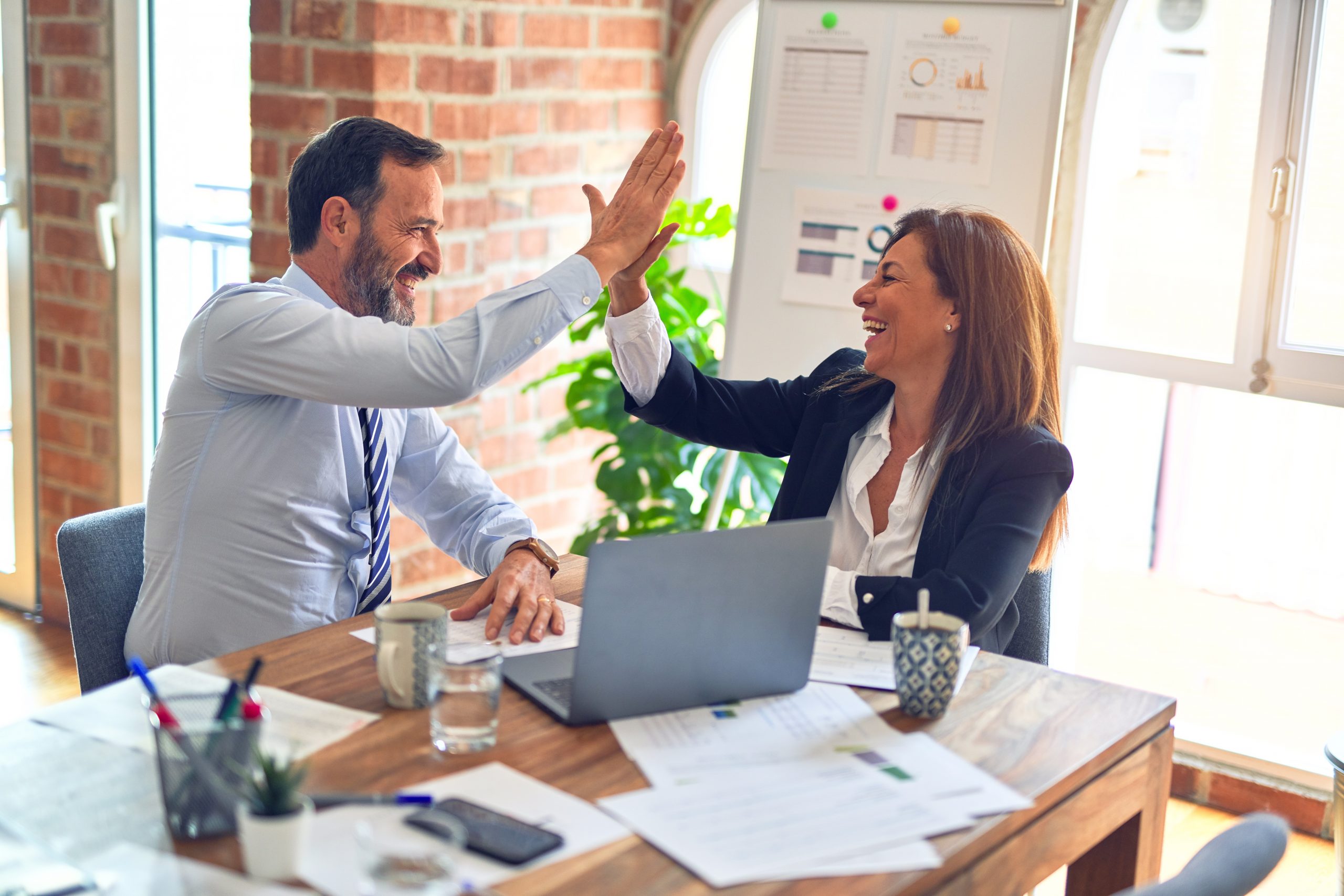
Baselining is a critical concept in Lean Six Sigma. Think of it as the foundation on which all improvement efforts are built. But in order to understand this concept and its importance, it’s necessary to first have a deeper understanding of what it is and what it does.
Overview: What is baselining?
This methodology — the first step of any project — is the process of establishing a standard or point of reference against which future performance can be measured. In business, it is often used to compare current performance against past performance. This can help organizations identify areas where they are performing well and areas where they need to make improvements.
Establishing a standard is done in any situation where it is important to track progress over time or compare different scenarios. When used effectively, it can provide a valuable benchmark against which to measure improvement.
3 common benefits (and three drawbacks) associated with baselining
The process of establishing measurement standards is so beneficial in some cases, the existence of drawbacks is often undervalued, or overlooked altogether. Following are the most common benefits and drawbacks associated with establishing measurement standards — there are three of each.
Top 3 benefits
1. Increased accuracy and reliability of data
By standardizing data, you can ensure that it is accurate and reliable. This is important for making sound decisions based on that data.
2. Improved decision-making
When you have accurate and reliable data, you not only make better decisions, you also make them faster. This saves money and time, and also improves your organization’s performance.
3. Easier identification of trends
By standardizing data, you can more easily identify trends. This can help you spot potential problems or opportunities that you may not have otherwise noticed.
Top 3 drawbacks
1. It can be time-consuming
The process of establishing these standards can be time consuming, particularly if you are trying to do so for a large number of data points.
2. It can be difficult to establish meaningful standards
This can be particularly challenging in industries or situations where performance is constantly changing.
3. It can be easy to become attached to these standards
Once a standard is established, it can be tempting to stick with it even if the situation changes. This can lead to sub-optimal decisions.
Why is baselining important to understand?
Establishing standards for measurement is important to understand for a multitude of reasons. First and foremost is its reach. Done right or wrong, it is something every employee not only feels when it happens, but also must continue to live with and work within for the foreseeable future. A good leader understands how changes of this nature can potentially affect morale and culture. Greater organizational understanding, resource allocation improvement, process prioritization insight, increased productivity levels, more informed decision-making, improved communication within an organization, and a better bottom line (increased profit) are all amazing benefits. But they can be difficult to achieve because the road to getting there is not always clear.
Most importantly, an intimate understanding of how to establish measurement standards is needed because doing so is by far the best benchmark from which to measure improvement. Knowledgeable and thoughtful oversight is crucial. When standards are not established at the beginning of a project, team members can find themselves basing their conclusions on incomplete or even incorrect data. In this situation, standardizing is essential for ensuring that projects continue moving forward in the right direction and do not veer off track.
An industry example of baselining: cybersecurity
Cybersecurity is an industry heavily ensconced in the world of establishing measurement standards. The very service they offer — or their ability to deliver an acceptable version of it — is almost entirely dependent upon accurate data derived from these standards. This industry faces particular challenges because, at least in the cyber world, situations (and therefore baselines) are constantly changing. And global events — like a pandemic, for example — can create challenges for even the most well-planned strategies.
To continue to provide protection and avoid downtime, cybersecurity firms deal with these changes by taking measurements of their work at various stages of the process. The data itself is also reclassified into different levels of protection. Critical business data, for example, may need a different standard than less important data. The next step is to identify which standards are achievable and relevant to the company’s security posture. After that, cybersecurity teams work to maintain those standards over time.
Top 3 best practices when thinking about baselining
The No. 1 most important best practice of this methodology is ensuring accurate baselines. Without that, it can be difficult to measure the success (or failure) of a project or process improvement initiative. Inaccurate baselines can lead to incorrect conclusions and wasted time and resources.
In addition to maintaining accurate data, here are two more key best practices to keep the data as relevant as possible.
Standards should be regularly reviewed. A review determines if they need to be adjusted or updated, which is necessary for baselines to remain relevant. By reviewing regularly, companies can ensure their offerings are still representative of current processes or projects. This will allow them to make changes when necessary and take corrective action when needed.
Use historical data whenever possible, because the more data you have available for this, the better. If you can use historical information to establish standards, your current data and future measurements will be much more accurate and reliable. That said, it’s about picking and choosing key, relevant data while eschewing anything superfluous.
Frequently Asked Questions (FAQs) about baselining
Q: Are baselines and benchmarks the same thing?
A: No, they are not the same thing. The former refers specifically to the starting point of a project or process, while the latter can be used to compare standards against other data sets.
Q: How often should standards be reviewed?
A: This depends on the project and organization, but it’s generally recommended that they be reviewed regularly — at least every quarter to six months.
Q: What if the baseline changes during the project?
A: In this situation, it’s important to re-evaluate the baseline and determine if it still accurately represents expectations for the project. If not, then a new standard should be established.
Q: What is a good way to establish baselines?
A: The best way to establish baselines is to use historical data. This will provide a more accurate representation of the current level of performance. However, if historical data are not available, you will be unable to establish truly accurate baselines.
Q: I’m having trouble establishing the baselines for my project. What should I do?
A: If you’re having trouble establishing baselines for your project, you may need to seek help from a Lean Six Sigma professional. They can assist you in setting realistic baselines that account for the specific project at hand. Additionally, they can help you track performance against those baselines over time.
Q. Is standardizing a project always a good idea?
A: No, this may not be a good idea, depending on your organization. For example, if you’re compiling data that is highly volatile or irrelevant to future performance, then it may not be necessary.
Is baselining the solution to your problem?
By standardizing a project, an organization is better able to analyze the effects of environmental factors that may have otherwise been overlooked. This way, a determination can be made as to if a process needs to be reworked from the ground up, rather than just trying to make changes within the current development parameters. And though the practice can create many significant benefits, remember that not every situation will require or be a good fit for it, and being able to recognize the difference comes with experience. To know for sure, reach out to a qualified Lean Six Sigma expert for guidance.