
AQL, originally known as acceptable quality level, was redefined in 2008 as acceptable quality limit. ISO 2859 defines AQL as the “quality level that is the worst tolerable process average when a continuing series of lots is submitted for acceptance sampling.”
This article will describe the sampling and testing procedures for AQL as well as the benefits and best practices of using an AQL approach.
Overview
The original standard for assessing AQL was MIL-STD 105 E. This standard has formally been replaced by various commercial standards such as ISO 2859-1 and ANSI/ASQ Z1.4.
ISO 2895 states the purpose of AQL is “to induce a supplier through the economic and psychological pressure of lot non-acceptance to maintain a process average at least as good as the specified acceptance quality limit, while at the same time providing an upper limit for the risk to the consumer of accepting the occasional poor lot.” It is measured in defect percent (or non-conformities) per hundred items.
AQL is a sampling methodology for doing incoming inspection of products. The decision to accept or reject lots of incoming materials is based on how many items can fail when sampled and inspected.
How It Works
The AQL procedure provides three things during your inspection. They are:
- The number of units or sample size to inspect
- The number of units with minor defects resulting in a failed result
- The number of units with major defects resulting in a failed result
The type of defects can be categorized as:

- Critical defects: Accepted defects could harm customers. This kind of defect is not acceptable and is defined as 0% AQL.
- Major defects: Defects are not acceptable by the end users since they are likely to fail. The AQL for major defects is often 2.5%.
- Minor defects: Defects do not reduce the product’s functionality or purpose, and end users will still buy these products. The AQL for minor defects is usually 4%.
As long as sampled defective pieces remain within the AQL range, the incoming lot of materials will not be rejected. If the number of rejections is higher than the set AQL, the entire batch will be rejected. Two tables provide the necessary guidance to reject or not reject the batch.
The first table, shown below, helps you determine the appropriate sample size as a function of the lot size and desired inspection levels.

AQL table for determining sample size
Note, there are three levels of General Inspection and four levels of Special Inspection. Based on previous experience with your vendor and the cost implications of sample size you would select the appropriate inspection level. The table provides the sample size code for determining whether to accept or reject the lot based on the number of defectives sampled from the lot.
Here are some guidelines for selecting your inspection level:
Level I (reduced inspection): Select this inspection level if you have had good experience with the vendor and they have been providing good quality in the past. This level requires fewer samples.
Level II (normal inspection): Usually the default level.
Level III (tightened inspection): If a supplier recently had quality problems, this level is appropriate since more samples will be inspected.
Special inspection levels (S-1, S-2, S-3, S-4) are normally used for certain types of on-site inspections or checks on a relatively small number of units in the lot. This is where an inspection requires destructive or time-consuming tests. The required sample sizes are smaller than the general inspection levels.
The second AQL table, shown below, tells you how many defects you are allowed to find in your sample before you reject the entire lot.
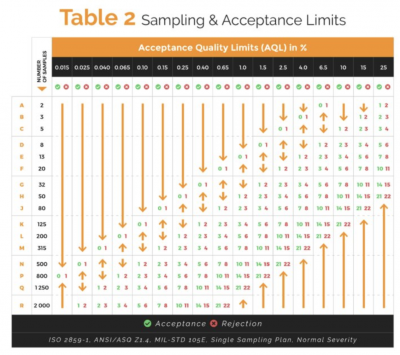
Sampling and Acceptance Limits
Benefits of AQL
The use of AQL to inspect either outgoing or incoming materials is a proven method for deciding whether to accept or reject a lot of materials. It is relatively easy to implement and has some significant benefits.
Cost-Effectiveness
Random sampling is less expensive than 100% sampling.
Flexibility
You get to choose your general inspection level and acceptable AQL percentage.
Clear Decisions
Your decision to accept or reject is clear based on the values in Table 2 for major and minor defects.
Doing More with Less
As we’ve discussed, there are some definite benefits to AQL. However, what does that mean for your production? If you’re looking to eliminate defects, it’s going to be a costly and time-consuming endeavor to do a complete inspection. While AQL doesn’t eliminate defects outright, it is going to get you much closer to your intended ideal.
Why It’s Important
While AQL is easy to use, there are some things you need to keep in mind.
It Doesn’t Guarantee Defect-Free Products
Since your sample size and decision criteria are based on a preselected level of quality, there is no assumption your lots will contain zero defects. The only expectation is that your quality will be no worse than your selected AQL defective rate.
It’s Better Than a Complete Inspection
In most cases, it’s not practical to inspect 100% of your product. Inspecting all your products is time-consuming and more expensive than sampling. The effectiveness of your inspectors decreases as they get tired.
It Is Based On Statistics
The sample size and accept or reject values are statistically based. This gives you more confidence in your decision of what to do with the lot you have inspected.
An Industry Example
An electronics manufacturer was finding an excessive number of defects during an incoming inspection. They decided to start using ISO 2859 and AQL as a methodology to more effectively sample the components coming from their suppliers.
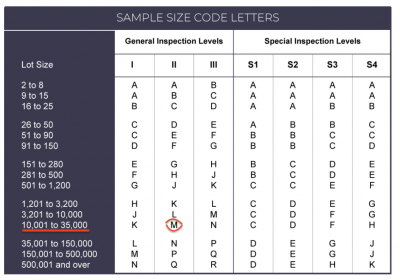
They tested their new approach with their largest supplier for a newly received lot size of 20,000 units. They chose a general inspection level II.
Since the 20,000 lot size fell between 10,0001 and 35.000 units on the left column, they needed to use a sample size in Table 2 associated with the letter M.

The sample size for the letter M from Table 1 is 315 units. They used an AQL of 2.5% for major defects and 4% for minor defects. Looking at the table above, you see the lot will be rejected if they find 15 or more major defects and 22 or more minor defects.
Unfortunately, inspection results found 13 major defects but 24 minor defects. Since that exceeded the allowable 21 units at the selected 4% AQL percentage, the lot was rejected.
Best Practices
Using AQL is a structured approach to sampling for acceptance. Here are a few hints to help optimize your use of the approach.
Pick One and Stick With It
Don’t send a signal that your AQL is negotiable and flexible.
Reward Your Suppliers
The default inspection level is II. If your supplier is doing a great job, consider using a less restrictive level.
Operational Definitions and MSA
Be sure you have agreed-upon operational definitions of what a defect or defective is. Also, be sure your measurement system is capable of identifying the defect. Conduct a measurement system analysis (MSA) before implementing an AQL process.
Other Useful Tools and Concepts
There is still plenty to learn when it comes to getting your organization to its absolute best level. Take FOCUS PDCA, for example. This comprehensive approach to process improvement gives you a total framework to adhere to throughout the entire cycle.
Additionally, you can see how things like AQL apply directly to your production line through the use of MSA tests. These tests are set up to make sure accuracy and reliability are consistently being met through your production line.
Summary
AQL is a popular sampling standard for choosing a sample size to be inspected, and the number of defects which will help determine whether to accept or pass an inspection lot of material. AQL’s random sampling approach is more time and cost-effective when compared to a 100% inspection of all of the units.
To determine the sample size to be inspected and the maximum allowed number of defect units, you use two AQL tables. The first table is used to find a letter code based on your lot size. The letter code is then used in the second table to find the sample size. The acceptable quality levels in the second table determine the maximum allowed number of defects.
The default general inspection level used in Table 1 is II. An AQL level of 2.5 and 4.0 in Table 2 are commonly used for major defects and minor defects, respectively. If the lot has either an excessive amount of major or minor defects, the lot is rejected.