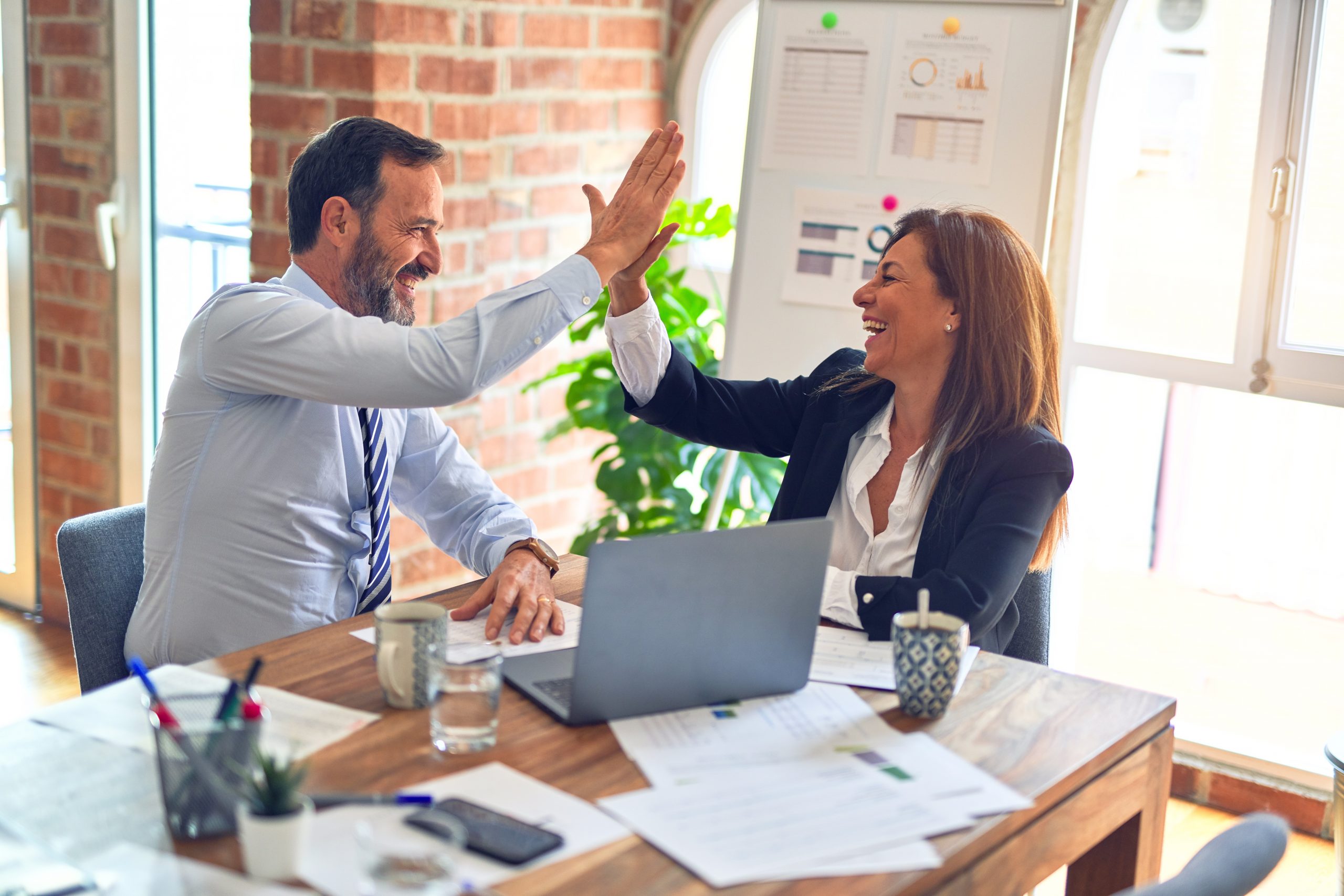
Message: 8897
Posted by: Carlos Castillo
Posted on: Tuesday, 29th January 2002
What are the benefits of choosing 6sigma over Kaizen, 6 sigma seems a great deal more expensive and more bureucratic. I have obtained great gains from Kiazen with minimal investment.
Message: 8899
Posted by: mn
Posted on: Tuesday, 29th January 2002
——————————————————————————–
I fully agree with you,so go ahead with kaizen and Gemba-kaizen, it is cheaper,cost-effective and much easier to understand & implemnt,less arrogant,it is a company-wide attitude based mainly on common sense.
Message: 8919
Posted by: Al
Posted on: Wednesday, 30th January 2002
——————————————————————————–
It should not be a question of one over the other.
Some companies get into a culture where you can not do anything unless it is six sigma – avoid that.
If Kaizen is working, keep doing it. But six sigma may be applicable to some of the bigger isues.
Message: 8922
Posted by: Jaran S.
Posted on: Wednesday, 30th January 2002
——————————————————————————–
I totally agree the Kaizen is effective. Many can get great gain with minimum investment. Happy to hear that you are the one of those.
However, all organizations are not the same. For some organization, the benefits of choosing 6sigma over Kaizen may be as the following :
1. They want breakthrough improvemnt, not just continuous improvement.
2. They hope they will improve faster.
3. It is expected that Six Sigma has better capability to solve the problem which can not be solved easily by Kaizen.
4. Six Sigma is more fasionable. It look good today to say “We have Six Sigma”.
For me, I want to use both at the same time.
Jaran S.
Message: 8926
Posted by: kiong
Posted on: Wednesday, 30th January 2002
——————————————————————————–
Hi,
Kaizen works well in slow-growth economy whereas six sigma is better suited to fast-growth economy. So it is important that organizations must know whether they are operating in a slow or fast economy. I liken that six sigma tends to skew towards “innovation” type of strategy thus only a selected few “champions” will called the shot, very rugged individualism, individual ideas and effort. And the mode of operation is scrap and rebuild and with a heavy dosage of technology leverage to get the results.
Whereas Kaizen tends to involve everybody and the pace of improvement is gradual and small but we know that every drop of water will eventually form the great ocean. Then why not combine Kaizen & Six sigma? Maybe this combination can bring the organisation to a much greater height!
Kiong
Message: 8945
Posted by: codeone
Posted on: Wednesday, 30th January 2002
——————————————————————————–
You hit the nail on the head. it is exactly because of the bureaucracy that 6 sigma is choosen. It is a great place for people to hid. One other benifit is, you can “in the name of 6 sigma” drive already overworked employees into giving more. for instance, the poster boy for 6 sigma who I work for has dictated that all managers have to do a 6 sigma project IN ADDITION to their normal job. and they have big bucks expectations. So, in the guise of driving this down the organization, they are really using it to drive revenue up and cost down. so instead of it being a tool to use when you have something to fix, it is no more than another tool for driving employees. so you see, you have to understand what is really behind this program. there are two main points.
1. make stock holders and analysis think there is something magic about the process that just makes your company so much better than it really is.
2. you can use the program to drive your employees, in the name of “learning more about 6 sigma” to work longer hours and produce more results.
so, bottom line is, don’t get hung up on which is better for your organization or future. 6 sigma offers too many opportunities for pulling the wool and abusing your employees.
Message: 8947
Posted by: ?
Posted on: Wednesday, 30th January 2002
——————————————————————————–
Because everyone is doing it. Pretty soon Six Sigma is going to burden corporations as does ISO-Yada Yada Yah.
Message: 8970
Posted by: RR Kunes
Posted on: Thursday, 31st January 2002
——————————————————————————–
Carlos,
Be very careful. While the kaizen type event is tanilizing the after taste may hurt you. I am learned six sigma and lean at Allied Signal and while we are strong advocates of the Lean Enterprise approach most advocates of “LEAN” do not understand the damage a quick one day or two day event can cause.
Believe me nothing is going to be fixed in a one day or one week event. What will occur is a long list of action items that may or may not get done. I do the Gemba Day, however, I fold it into the six sigma regimen. If you do not you will usually get bad data and miss the major cause of problems.
Remeber six sigma andd lean are designed for two distinct different things. Six Sigma is for reducing variaiton in the process, lean is for improving the process flow. Identify what your problem is then utilize the proper aproach. If you don’t you will get a faster production of defects, or, reduced defects but still a bottleneck.
Use your tools appropriately.
RR Kunes
Master Blackbelt/Lean Expert.
Message: 8971
Posted by: Bobby
Posted on: Thursday, 31st January 2002
——————————————————————————–
Codeone, you appear to be contradicting yourself.
“So, in the guise of driving this down the organization, they are really using it to drive revenue up and cost down. so instead of it being a tool to use when you have something to fix, it is no more than another tool for driving employees.” You state that the company uses it to impact revenue and cost, but then turn around and say they don’t do that, but instead use it to drive employees.
I would think it the responsibility of every member of a company to impact revenue and cost in positive ways AND show a resulting benefit to the customer. If the SS projects being performed don’t do this, then either the proj mgr is not choosing the appropriate business case or the champs, sr. mgrs, etc are not ensuring SS is being used appropriately.
I would agree that SS can be used in incorrect ways and shouldn’t be used for every problem, but the tools learned and applied during a SS project can be used outside of project work, and should be.
I hope you can see the positives of the program even though it may not be applied correctly in your organization. I mgmt is focused on doing SS for the sake of doing SS without being focused on the results, then surely there is a significant amount of waste occuring.
Message: 8975
Posted by: smithsigma
Posted on: Thursday, 31st January 2002
——————————————————————————–
I agree to a great extent…
So, if you are truly a certified Lean Expert and Master Blackbelt – you must be in high demand. I went through Allied Signal’s Lean training – really good stuff.
Message: 8990
Posted by: Ray
Posted on: Thursday, 31st January 2002
——————————————————————————–
Sounds like Codeone should look for a different job…
The company I work for successfully combines both Kaizen & 6S. It’s all in the project scoping & selection. It becomes evident very quickly what level of involvement is required to get the bottom line results.
Message: 8991
Posted by: codeone
Posted on: Thursday, 31st January 2002
——————————————————————————–
I guess it kind of makes me mad that all hype at GE is “this is customer focused”. when in fact, 90% of all of this is internally focused. One division I know of even went to far as to come up with a quicksigma idea. basically, they wrote things up on an excel spread sheet and sent it in to get six sigma credit at corporate. This is what always happens. The Bureaucracy takes over. The organization is chock full of people that have never produced a good or a service, but they can make charts and know how to manage up. In my division, the optics are of course very much in play. but we have some of the more aggressive managers pushing the employees to produce extra in the guise of doing a six sigma project. In all my years of experience with this process, I have never seen six sigma produce anything. basically, someone has an idea and (of course anyone that has been around for a while can do most of these things as second nature) and they put the project in place. but in order to get the six sigma credit, they spend many many man yours trying to back fill the six sigma template so they can in fact get the credit. like one of the “master black belts” told me one time, if it did not happen in six sigma, it didn’t happen. it is truely a joke.
Message: 8998
Posted by: Chris
Posted on: Thursday, 31st January 2002
——————————————————————————–
Let me guess. Either you were passed over to be a Six Sigma practitioner or…you were never good enough at it to get anything done or…YOU are trying to hide in your organization and can’t now because they are driving YOUR job with metrics.
This forum is for people who have something constructive to contribute to process improvement. Not people who want to complain about it because they don’t understand it.
P.S. If you are a Black Belt and have this attitutude, I feel sorry for you, your company and anyone around you. Gallup Q12 has a term for you – Actively Disengaged. This means you are one step from being fired because you can’t contribute to your company in a tangible manner.
Message: 9008
Posted by: isoquality
Posted on: Friday, 1st February 2002
——————————————————————————–
Six Sigma concept is focusing on “do the right thing” from the early stage like in R&D to have robust product and/or process design.
I don’t say Kaizen is wrong or no good, but its incremental improvement approach may falling into “do the thing right” trap. For people in the production floor shall understand how tough to reduce process variability if the process design is incapable or not robust.
Incremental improvement with Kaizen may not be the most cost effective way in attaining robust process or product.
This is just my 2-cent of thought.
Message: 9042
Posted by: Carlos Castillo
Posted on: Saturday, 2nd February 2002
——————————————————————————–
Mr. Kunes,
I think you are confusing Real Kaizen, with Kaizen Blitzes. Real kaizen is a very long process, it is about changing peoples’ mentality. I don’t want my employees to perform a weeklong Kaizen event only to return to their daily work and see waste all around them and not do anything about it. I want people to question things and to notice when things are not right. The number one reason TQM and Zero Defects died was because, companies thought that if they measured and fixed a problem they were TQM or Zero Defects. Get a team of Operators, Managers and “Experts”, tackle a problem for a week see what happens, a month from now they will not remember what they did. Any long term change requires Upper Management’s drive as well as a lot of training and follow up. Quick wins are good but you need long term to really get benefit.
Message: 9044
Posted by: isoquality
Posted on: Saturday, 2nd February 2002
——————————————————————————–
Kaizen was originated from Toyota Japan. It’s more on continual improvement or small incremental improvement over a long time span rather than a drastic breakthorugh or revolution. Toyota car is still the most reliable (MTBF) car in the world. So I don’t see Kaizen is a bad thing if people can really understand its concept and implement it in systemic or holistic way.
I prefer to say leadership than management is key to everything.
Message: 9045
Posted by: Kim Niles
Posted on: Saturday, 2nd February 2002
——————————————————————————–
Dear Carlos, et.al.:
Good question. I just attended a Six Sigma workshop in San Diego where nearly the same question was brought up.
Key contextual aspects include:
1- Large companies use “Kaizen blitzes” or “Kaizen Events” both at the same time. Example, Honeywell (former Allied Signal) uses both in combination (I know this from numerous personal sources).
2- Six Sigma has been adopted more by very big companies with very big confounded situations and ROI potential as opposed to small companies where the processes are more easily fully understood and the ROI potential is small relative to the cost of implementing Six Sigma.
In my opinion, there isn’t a very big difference between a Kaizen Event and a Six Sigma project other than mandated talent, scope, and time frame (~3-4 days vs. 3-4 months). Most other basic principles still apply to both.
I see the future of Six Sigma within the smaller company consisting of a lot more merger with Kaizen and the future of Six Sigma within the larger company consisting of a lot more Kaizen and Six Sigma in combination. The reason for my statements is purely implementation cost justification.
I’ve heard a lot of complaints that the training Black Belts are receiving is not enough to meet the needs of managing a Six Sigma team unless the candidate already has a large head start before the training starts. One way I see this happening is through Kaizen.
What do you think?
Message: 9178
Posted by: codeone
Posted on: Wednesday, 6th February 2002
——————————————————————————–
Well, I think we all know how to classify you. A sycophant no doubt.
No, you are wrong on all counts. I have been promoted over 12 times in my career. I have even spent a stint running a large part of our business overseas, where I lived.
All I am trying to say is that if your only tool is a hammer, every problem starts to look like a nail. The statistics are easy. I used most of them 20 years ago when I was a lowly industrial engineer.
I have been a code one or two at the largest multinational company in the world for over 30 years. But I cannot roll over and play dead when organizations are embracing this stuff like a “magic bullet” thinking it will replace experience, common sense and business smarts. And this is exactly where it is going.
What I have found is that most of the people that embrace this at my company are in fact short time folks with no real success behind them. Those with any tenure did hide in the organization until this process came along. Now they can sit in a cubicle and make charts and attend conference calls and not really have to produce anything. 90 % of the “Projects” that these folks do could have been done in one-fourth the time and without dragging 40 other people into the thing. And 90% of those are no longer in place six month later. Why? They were done for all the wrong reasons. It is a dog and pony show. Projects are selected and completed in order to meet the goals of the company. You have to be a “green belt”, or a “Black Belt” or a “Master Black Belt” in order not only to keep your job, but to ever hope to have a promotion. And now that it is a business initiative, no one in upper management will tell the emperor that he has no clothes. We find ourselves in the business of managing careers, not the business and this process is the perfect tool. By embracing it, you get to appear that you are a “team player” while not really doing anything constructive for the business. This process does have its place. In a DFSS, if a company does not already have a good product introduction plan, this will work. And for everyone else, its like the song says, its full of “pretty pretty boys, we call men”.
Message: 9179
Posted by: Terry
Posted on: Wednesday, 6th February 2002
——————————————————————————–
I’ve been reading the Kaizen vs. Six Sigma debate and decided to add my thoughts. Sorry if its a bit lengthy.
First of all, If you look at this as a choice, you’re doing the wrong thing. These are tools in a toolbox, nothing more. I tell people to think of Kaizen, Lean, and Six Sigma as drawers of tools in your big Craftsman toolbox. Its like a carpenter saying I’ll always use the hammer but forget about the chisel. Then another carpenter comes along and says he hates hammers but likes the mitre box. The person who made the comments about “not a choice” was right on. It all depends on what kind of problems you’re trying to solve.
Second, Kaizen blitzes are great for the no-brainers that we fall over everyday. If you’re having success, then keep it up (You must have a lot of low hanging fruit). If you have logistics, cycle time, delivery, flexibility/responsiveness, or asset utilization problems, then the Lean tools work best. If you’re trying to reduce a 24 hour burn-in cycle by 75% or you’re trying to optimize weld schedules for a $12 million progressive assembly operation or you’re trying to strategically size your inventory pipeline for quick response, you better think about using the Six Sigma tools. These kind of projects have $ millions of opportunity. Kaizen blits “ain’t gonna get you there.” In fact, Kaizen Blitzes might make the problem worse if you start to make a bunch of changes without understanding the variation drivers and root causes.
Last, if Six Sigma is a bureacuracy or a pretty boy process in your company, it’s not Six Sigma’s fault – Its the way your organization has implemented it. This stuff works well, but simply cloning what GE or some other organization has done will probably result in an unsuccessful program. Its takes more than going through the process and the education, hanging up the charts, or talking the statistical jargon to each other. Leadership, execution and results makes any of these programs successful or unsuccessful.
The most successful organizations deploy all of these tools concurrently. They focus on the problem and then select the appropriate tools to fix it. They don’t debate about Kaizen, Lean, Six Sigma – They just open the right drawer, take out the right tools, fix their problems, and enjoy the results.
Message: 9189
Posted by: Eoin Barry
Posted on: Thursday, 7th February 2002
——————————————————————————–
Ovidiu. Thank you for your slide.
I have a couple of observations which I hope you don’t mind if I share with the community. The complexity of the problem is not an appropriate method of determining the tool to use to fix it.
Six sigma and lean or TOC are complimentary. There is nothing in six sigma, which impedes either lean priciples which, for example, are embodied say in the Toyota production system (TPS) or theory of constraints which, for example is beautifully illustrated in the book “The Goal”.
TPS and TOC may share some differences however.
Lean excercises or KAIZEN or Blitzes provide excellent platforms for six sigma. They put the D in DMAIC!
Message: 9349
Posted by: chris
Posted on: Friday, 8th February 2002
——————————————————————————–
Thank you for the reply and a better explanation of your attitude toward Six Sigma. What you have described is a dysfunctional company – not a dysfuntional problem solving tool. Basically everything you said is exactly why many companies fail at implementation. I was involved in one of those failed deployments at a large company.
Some points:
1.The statistics are easy. I have been using them for 20 years also
2.Six Sigma is not a magic bullet and should not be treated that way
3.Good companies embrace several problem solving tools which address issues at various levels (just do it, kaizen, Six Sigma, Lean, etc.) and integrate them. That way you are not using a hammer to fix a watch.
4.If 90% of the projects were no longer in place, then I would be looking at Champions and Process Owners. My question when this comes up is – If I can’t get the Process Owners to implement these changes, what chance do I have of getting them to implement the “common sense” changes. People tend to forget that It doesn’t matter what tool you use. If the people don’t integrate it into their business, NOTHING will stay fixed.
5.In good companies, projects are tied to business goals which can be found in the Balanced Scorecard or other system which allows a company to make sure their efforts are directed to critical areas.
Again, thank you for adding more detail to your story. I have blasted a few people on this forum before in order to get to the real reason for their frustration. If I can quote a phrase “Don’t throw the baby out with the bath water”. If used correctly, Six Sigma is a good high powered tool which can enhance a business. But like any tool, it can be abused if not used correctly. Good luck.
P.S. After 12 promotions, aren’t you the CEO by now:)
Message: 10094
Posted by: Allen
Posted on: Thursday, 28th February 2002
——————————————————————————–
“Toyota car is still the most reliable (MTBF) car in the world.”
Where can this data be found?
Message: 27800
Posted by: Manoj Bhardwaj
Posted on: Wednesday, 21st May 2003
——————————————————————————–
During Control phase of any Six-Sigma Project many “small but new” improvement activities are carried out.We may “see” these new,small and large number of improvements as “Kaizen*” resulting out of Six-Sigma implementation.
Inversely,a large collection of “Regular Kaizens”, if carried out in a “Single” well defined Process, may result in an improved state with lesser number of defects in the output of that Process.
I think it just depends on whether the initiative for improvement has come from the shop floor or from the top/mid level managers.
The Best is the right combination of using the right tools for getting the right improvement at the right cost at within the right time span at the right time!The combination will definitely vary from time to time even for the same Business Organization.
It should be a Win Win situation and it has to be the right combination of Six-Sigma and Kaizens.
I sincerely request feedback as this is a very very important topic for sustaining the faith in Six-Sigma initiatives.
Manoj Bhardwaj
Message: 36961
Posted by: KBailey
Posted on: Monday, 1st December 2003
——————————————————————————–
Is it really a choice of one or the other? Or is it really a matter of being flexible to invest appropriate resources in defining the problem, measuring the current state, analyzing relationships between inputs and outputs, improving the process, and controlling the process to sustain the improvement?
I’m no Kaizen expert, but it seems to me that fundmental problem-solving steps are basically the same. Back in elementary school in the 1970’s I learned that the first step in solving a problem is to define it. The time and energy you put into each step should be a function of the risk associated with change and Cost of Doing Nothing. The risk associated with change is largely a function of complexity. (Risk = Probability * Cost, totalled over everything that could go wrong.)
Sometimes, eyeballing as a measurement system is good enough. This can even apply to “measuring” whether a problem is adequately defined, measured, analyzed, or improved. I don’t believe Six Sigma per se says you can’t be flexible with these standards when it’s appropriate.
We live in an increasingly complex and competitive world. Competitive pressures on price, quality, and timeliness increase the Cost of Doing Nothing. Risk associated with change also grows due to the higher potential cost associated resulting from this competitive pressure. The risk increases even faster, however, because the competitive pressure also increases the probability of something going wrong with the change. Over time, the need for a disciplined, methodical, proactive approach with potential for continuous and radical improvement like Six Sigma, will tend to grow in organizations seeking long-term success.
Message: 37002
Posted by: Mike Carnell
Posted on: Tuesday, 2nd December 2003
——————————————————————————–
Carlos,
I am not sure why anyone has to make a choice. They are two different things – Kaizen for incremental improvement and Six Sigma for Breakthrough type improvement. If you read “Lean Thinking” by Womack you will see that both techniques were part of the Toyota Production System although the breakthrough strategy was called kaikaku (probably spelled wrong but I don’t have a copy of Lean Thinking close).
You need to understand what you are trying to accomplish and select the appropriate methodology. If you read Juran’s “Managerial Breakthrough” (yes it is Juran’s book) he explains the difference between control and breakthrough. It may help you understand the difference and therefore the reason it is more logical not to choose one over the other but how to create a balanced program that uses both as well as Lean.
Good luck.
Message: 43907
Posted by: sebastian
Posted on: Tuesday, 13th April 2004
——————————————————————————–
Fully agree with you. I take a strong liking to building the basics, and creating the right knowledge ecologies. Six sigma is just another tool, albeit an expensive one. I was lucky enought to study a pure version of Kaizen. It’s really beautiful in its simplicity, and aplicability. Add a little knowledge management, and respect for people to boost innovation and you’re there!
Of course you don´t land a 80k job by being a team-player.
Best regards
Message: 43920
Posted by: Doug
Posted on: Tuesday, 13th April 2004
——————————————————————————–
Carlos,
I understand your question and would pose the following question back to you…
“Why not use Kaizen to aide Six Sigma?”
I have worked a variety of Lean and Six Sigma projects and have used Kaizen to shorten then amount of time needed for a SS project. If you can get the dedicated resources required for a Kaizen event (which, in my opinionn, is the most difficult part of Kaizen), you can easily complete the DMA portion of the DMAIC SS project. Then your team basically just has to work on the Improvement implementations and the control phase of the SS project. I have used this approach with very good results and have cut the average 3-4 month time frame of a SS project to 2 months (we have done some quicker than that).
Doug
Message: 43949
Posted by: Ron
Posted on: Tuesday, 13th April 2004
——————————————————————————–
Carlos,
I think I know understand the point of your message. I apologize for the U.S. centeric viewpoint on these issues. In eastern countries thier philosophy has evolved continuous improvement as a way of life. In the West we have not been so fortunate.
In Japan kaizen is small incremnental changes that evolved as a standard work practice, unfortunately those type of events are normally under the control of only those processes changeable by the work group involved, and that is the only limitation to that process. If you are already at 5+ sigma perhaps that is all that you can do outside of the designed in issues.
In the U.S. and the philosophy behind the six sigma movement is to implement breakthrough changes that significantly change the way we do business. I utilize what I call kaizen events to crumble any barriers that may pop up in the implementation of those significant corporate changes that we focus our projects on.
Hope that clears it up for you.
Message: 55266
Posted by: Aurangabadi
Posted on: Monday, 20th September 2004
——————————————————————————–
Doug,
I have been reading your opinions and of everyone else in this session.
Let me pose my comments as a question (slightly long one)
From times immemorial (and through common sense), we have used the familiar cycle of identifying a problem, putting metrics around it, making a CBA, brainstorming for solutions and finally implementing one (you would have done it too). We then put in reports and Incident reports etc to monitor the process and look for improvements. The people responsible have been those who want to get things done and are perhaps accountable for good performance. The management is always interested in good initiatives and they are being played as the villains for ever !
For the above processes, we have always used cause and effect (fishbone) diagrams, flow charts, histograms, pareto analysis, process maps, architecture diagrams, test models, SLA documents, training programs, market surveys etc.
My question is: What’s causing this issue to create such a fuss.”. Is it the question of top management support? Is it the question of tools? Is it the question of techniques? Is it the question of jargon and buzzwords?
We have had all this before and we still have them. Do we mean to say that Six Sigma is different from what we already know? That we will be lost without the buzz words and the multicoloured belts?
Why not just do our jobs and minimise problems through the core concepts? (unless you need to join the jargon bandwagon). What do we need Six Sigma for? We are still doing it even without the label, right?
Manish
(manishgrovermail.com)
Message: 55478
Posted by: Doug
Posted on: Thursday, 23rd September 2004
——————————————————————————–
Manish,
I applaud you for being so dedicated to your job that you already follow a rigorous process that makes your projects successful. However, not everyone is like that – which can be where Six Sigma comes in and helps out. Six Sigma provides structure to a project – it provides a path for people to follow in order to drive towards a successful completion. The integration of the Lean Principles into Six Sigma (or vice versa) makes it even more powerful and successful. Most of the companies that I have worked for have always complained about solving the same problem over and over again – guess what – it is because they did not lock in their improvements. They spend there time going from one issue to the next, firefighting.
I have read a lot of the posts and debate that this topic has launched – which I think is great. Discussions like these will help produce a better, more robust system than what many have in place today. I am also disappointed, but not surprised, to hear the abuse that the methodology is taking at various companies around the country and world. Six Sigma and Lean, Lean Sigma if you will, should only be used when necessary. If you already have the answer to a problem, don’t force the methodology on the solution. Implement the solution, lock it in place, and move on. Lean Sigma should be used when the solution is not known – then it can be one of the most effective tools in your tool box. To steal from another comment that I read in this chain of posts, just because you have a hammer in the tool box does not mean that you have to use it. Use it when you need to. Otherwise, it is just waste.
Sorry for rambling…
Doug
Message: 84400
Posted by: Reza Pirasteh, Ph.D.
Posted on: Friday, 2nd December 2005
——————————————————————————–
Kaizen is an effective approach, generically, in identifying NVA and removing it. Many times it has to do with process Takt improvements, CT improvements, etc. As the 5th element of Lean, it may be necessary to control variability in the process. This is when Six Sigma approach is effective: – to identify the source(s) of variation – To separate trivial many from the critical few – Identify CNX – Set up control parameter (DOE if necessary) – Identify guidelines for a robust process – Set control parameters and metrics to ensure process stability and capability.
I don’t like to separate Lean and Six Sigma. I believe they need each other for a sustainable solution. I am not sure why integration of SS into your process would be expensive! unless the CE-CNX process is not done properly and much time and money is wasted on too many or non-critical factors or useless DOEs. If you have many low hanging fruits in your organization, with large CT, inventories, WIP, spaces, traditional layouts… then initially Kaizen efforts is the way to go. But if your processes are highly sensitive to variability and looking for quantum leaps, then you may benefit from SS. I suggest keeping an open mind and accepting what brings you solution rather than being hung up on what is the method called. Good luck.
Message: 88068
Posted by: Walter
Posted on: Wednesday, 8th February 2006
——————————————————————————–
Six Sigma and Kaizen are not used due to fast or slow growth of a company. Kaizen is used to prevent chronic problems that Six Sigma tends to solve. I spent my time with a comapany using Six Sigma and now I work with a company that uses Kaizen as a foundation ( which will be the # 1 Auto maker of the world in 2 years or less). I see the need for both tools, but if you are always improving the total package of Six Sigma is not needed.
Message: 88092
Posted by: Adam L Bowden
Posted on: Wednesday, 8th February 2006
——————————————————————————–
Heebee ….
Insanity – doing the same thing over and over again and expecting different results 🙂
Six Sigma, Kaizen, Kaikaku, Lean, Hoshin etc etc – you need a subtle blend of them all – only the foolish or ignorant solely focus on one methodology.
Best regards,
Adam
Message: 88108
Posted by: Horticulture
Posted on: Wednesday, 8th February 2006
——————————————————————————–
Ha!
Dictionary.com: the source of all knowledge.
My 2nd favorite (after this one): thefreedictionary.com. Check out the daily word match game.
Heebeegeebee, it sounds like you have this Lean vs. 6S thing all sewn up.
How would you answer the question?
Message: 88148
Posted by: heebeegeebee BB
Posted on: Thursday, 9th February 2006
——————————————————————————–
A tool, is a tool, is a tool…
I have a tool box. My toolbox contains Lean, Six Sigma, TQL/TQM, Taguchi methods, Kaizen, Hoshin, deming and Juran concepts, Team building, Change Management, OD, Basic data collection, a big wooden club, the” Jedi Mind-Trick”, etc…ad infinitum
I still find amazing how “religious” some people get about using certain methodologies…
If I have identified a sub-tier process that is causing problems, I’ll likely conduct Gemba Kaizen. If I identify a pervasive/systemic issue, I’ll commission a full-blown project. Scope plays a big role in how i attack a problem.
It is not a zero-sum condition… I call it the chinese-food approach, take what you like (what works) and leave the rest.
They are just tools, people!
Message: 88235
Posted by: Horticulture
Posted on: Friday, 10th February 2006
——————————————————————————–
Which tool works for a specific problem depends on a bunch of things. Key ones are:
The people dynamics in the relevant areas
Complexity of the problem
Availability of information and data
Time allowed
The majority of the things identified in this discussion thread
and
Support for the approach being used.
If there is no support then the initiative – whatever it is, and regardless of anything else, will fail.
If the problem solver who is to lead the effort is well respected with a strong track record of good solutions, then the chances are that they will be able to say “I want to use approach X” and they will get the necessary support.
If there is discussion and uncertainty as to how best approach the issue, then concise guides as to which approach to use when, are useful.
H.
Message: 88252
Posted by: Dog Sxxt
Posted on: Friday, 10th February 2006
——————————————————————————–
Thank for quoting my old posting. isoquality.com was my former handler before this domain was transferred to ISO. 🙂
Kaizen and Six Sigma have their own value proposition. My approach on which one shall be used is pretty simple and straight forward.
If the root cause is unknown and problem is complex, then six sigma is a better candidate. If the root cause already know (almost know with 5-why probe) and problem is simple, then Kaizen is more appropriate.
In my rough guess without supporting data, 70-80% of problems can be tackled with a few day kaizen event by first line workers, while another 20-30% stubborn problems need more skilled Black Belts and longer time to dig out their root causes.
Kaizen is more useful and practical solution for transactional processes. Besides, try to teach admin workers about six sigma tools is daunting task, trust me. 🙂
DMAIC can be used for both Kaizen and Six Sigma though the tools used are different between them. A bunch of people equal DMAIC as Six Sigma is another myth.
Let apply IE thinking in lean and Quality thinking in Six Sigma will make you see the light at the end of tunnel.
The Six Sigma founding company re-adopted lean after ignoring lean for many years. We help them at behind the scene under a strict non-disclosure agreement.
Another two Fortune-500 companies with Asian background are inviting us to discusss lean and very interested to re-introduce lean after many years of sole Six Sigma journey.
Message: 89401
Posted by: Ripman8
Posted on: Thursday, 2nd March 2006
——————————————————————————–
RU Kunes, I don’t have a lot of time to properly respond to this so let me just say what Lean really is. Lean is Eliminating Waste. The process will automatically flow better as you identify and eliminate the 7 wastes. Six sigma is for organizations with fast technology turnover and organizations that are on the top level of lean. Even Toyota isn’t at the top level yet.
Message: 95356
Posted by: Peter McDonald
Posted on: Monday, 12th June 2006
——————————————————————————–
I am all for integration of techniques.
In regard to kaizen, lean and six sigma can we be clear: kaizen just means continuous improvement…lean and six sigma are kaizen strategies.
Some how kaizen has been misinterpreted as a fast facilitated workshop or action oriented improvement event.
Six sigma and lean as just branded names for continuous improvement both with the same basic philosophy: in my words:
All work is a process, it can be measured and improved.
They have the same principles:
Customer focus (this is the key principle that allows you to determine what is waste in lean), manage and understand variation, Use facts and data to make decisions.
All with similar enabling philsopohies around team work and leadership.
Allthough lean, six sigma etc, etc have been fantastic in raising the profile of the process profession both cloud themselves with some eastern mysticisim and unsustainable names eg black belt, that I suspect will undo them in the longer run. In the short term I think these names have provided some interest and media attention …do you really think in 20 years we will still be hiring black belts or do you think we will move to process professional similar to projects management proffessionals.
The quicker we let go of the lean and six sigma schisms and move to process professionals embracing all brand names the better. I read too much splitting hairs on why one is better than another and restrictive trade practices around who is and who isn’t a six sigma professional despite the fact there is little standardisation of course, requirements. Certification from within a commercial organisation that despite it being well-meaning is fraught with dangers and politics. Rather than embracing the underlying philosophy and just use the right tool at right time.
I see the key for success is to move to a common profession including the very important underpinning area of process management an area highly underdone by both lean and six sigma.
Cheers Peter
Message: 95376
Posted by: Gary
Posted on: Tuesday, 13th June 2006
——————————————————————————–
Codeone
I am a Master BlackBelt who has been at it for almost 20 years. What I hear in your writing is someone who wants someone to answer the question, “So What?!?” I believe that your concerns are well founded and should not be directed at Six Sigma, but at the Six Sigma implementation at your company. It is a shame that common sense has been denegrated and experience discounted. Those are the hallmarks of any good (read: successful) improvement effort, or company, for that matter.
I have consulted in TQM and Six Sigma and have seen so many failed, bureaucratic attempts that leave such a bad taste in people’s mouths that I want to cry. My mentors (from Japan) utilized the tools of TQC, CWQC, TQM and, by extension, Six Sigma to make real improvements that mattered to a country’s economy that was in desperate need of improvement (50s, 60s, 70s). One quote, “Total Quality Control is the practical application of common sense,” has always rung true to me in helping others through the bureaucracy. It is unfortunate that you are currently in an organization that is celebrating the form rather than the substance. That is usually the case in the early stages; then the program will either morph toward common sense or die an ugly death.
I get the feeling that your perspective on all this is really in line with those of us who think that Six Sigma has merit, and I hope in the future you will experience an implementation that utilizes the organization’s most important asset (its people and their experience) and exercises common sense to make lasting improvements to the bottom line and the company’s customers.
Hang in there
Message: 95437
Posted by: annon
Posted on: Tuesday, 13th June 2006
——————————————————————————–
Kaizen is simply a term that refers to continually improving a process by taking it apart (or some element of it) and rebuilding with improvements. Essentially, it gets the people in the room that know the process, identifies root cause, selects a solution and implements. You can do this anyway you want, using lean or 6S tools as appropriate. No need for a rigid seperation of skill sets…lean is very applicable where cost or time is the metric of choice, and 6S works nicely where a known target and spec are involved. Good luck.
Message: 102017
Posted by: Dominic
Posted on: Tuesday, 3rd October 2006
——————————————————————————–
I attempt: Why anyone has to make a choice between Six Sigma or Kaizen? The attempt is not supported by statistical data but based on a, man on the street type of analogy.
One has to walk before one could run. Therefore one has to learn to walk well before one starts to run, let alone win a race.
In the analogy, many a times one starts to run before one could walk (worse still if one is still crawling!).What happens if the attempt to run before one walks fail (irrespective of the fact that one will inevitably fail!)? The answer is obvious, the system does not work for us, we are a special case!
If one has mastered the art of walking well, then it is time for running!
If you are a good runner, then you can walk and run intermittenly and can manage both well. If you are struggling to walk (and in need of a walking aid) then running is not for you.
Likewsie it is my opinion that Kaizen, the incremental improvement (or change for better!) is equivalent to walking. And the Six Sigma, breakthrough improvement (BI) is like running. You can only attempt to do BI if you are capable of CI (continous improvement). If the organization is not capable of CI then I wonder how they could do BI.
Cheers! Dominic.
Message: 102046
Posted by: Mike Carnell
Posted on: Tuesday, 3rd October 2006
——————————————————————————–
Dominic,
Evidently you did not read my 3 year old post very well. I stated you don’t have to make a choice.
This is purely my opinion but you analogy is about as far off target as the people who believe they need to make a choice. It all sounds very nice andlogical but if you have any experience with someone who drives a Kaizen event – given a good project then you would realize in the correct application characterizing Kaizen as “baby steps” is insulting, condescending and arrogant.
It also implies since “a person must walk before they run” that the application is serial. It does not have to be and the order can be switched easily.
Just my opinion.
Message: 102093
Posted by: Brit
Posted on: Wednesday, 4th October 2006
——————————————————————————–
Not sure I agree Dominic.
I have witnessed breakthrough improvements in Lean, SS, and Lean SS. Actually, from a facilitation standpoint, a Kaizen event may even be harder to finish. Someone needs to keep the team focused/on track and that can sometimes be a challenge. Bottom line – you have to walk before you run no matter which improvement process you work with, if you start from scratch (i.e., no knowledge about either method).
One issue I have found relates to resources. I am currently working in a hospital. We conciously chose not to do Kaizen events because there was no concievable way we could pull nurses from patient care to be in a 4-5 day Kaizen event, given the nation-wide nursing shortage. We need their input for clinical projects especially, so a more drawn out project approach is the way we chose. I woudl rather have a problem solved in 5 days, but sometimes that isn’t possible.
Finally, as for the difference between Kaizen and SS – I’m assuming you might be referencing continuous improvement with Kaizen and not with SS. Our Lean SS process is a continuous improvement system, as we monitor throughout the control phase and beyond and make our necessary adjustments as market and process conditions change.
Message: 115980
Posted by: rp
Posted on: Monday, 9th April 2007
——————————————————————————–
Six Sigma & Kaizen, same thing. Kaizen is an accelerated method of using DMAIC, that’s about all…actually more pragmatic because I’m not a believer of stretching any project to more than a month…
Message: 135165
Posted by: Vinod Chandran
Posted on: Sunday, 3rd February 2008
——————————————————————————–
I would like to compare kaizen & 6 sigma with the game of cricket. For a batsman the 1’s, 2’s and 3’s are very important to build a large score and that is “kaizen”. However when the 4’s & 6’s come his score leaps and that is “6 sigma”. Both are important. Small incremental continuous improvements (kaizen) eventually will bring about breakthrough improvements (6 sigma).
Another significant difference is that 6 sigma is top driven and need the bottom to lock in the gains. Kaizen on the other hand is bottom up and need the Top to recognize the gain.