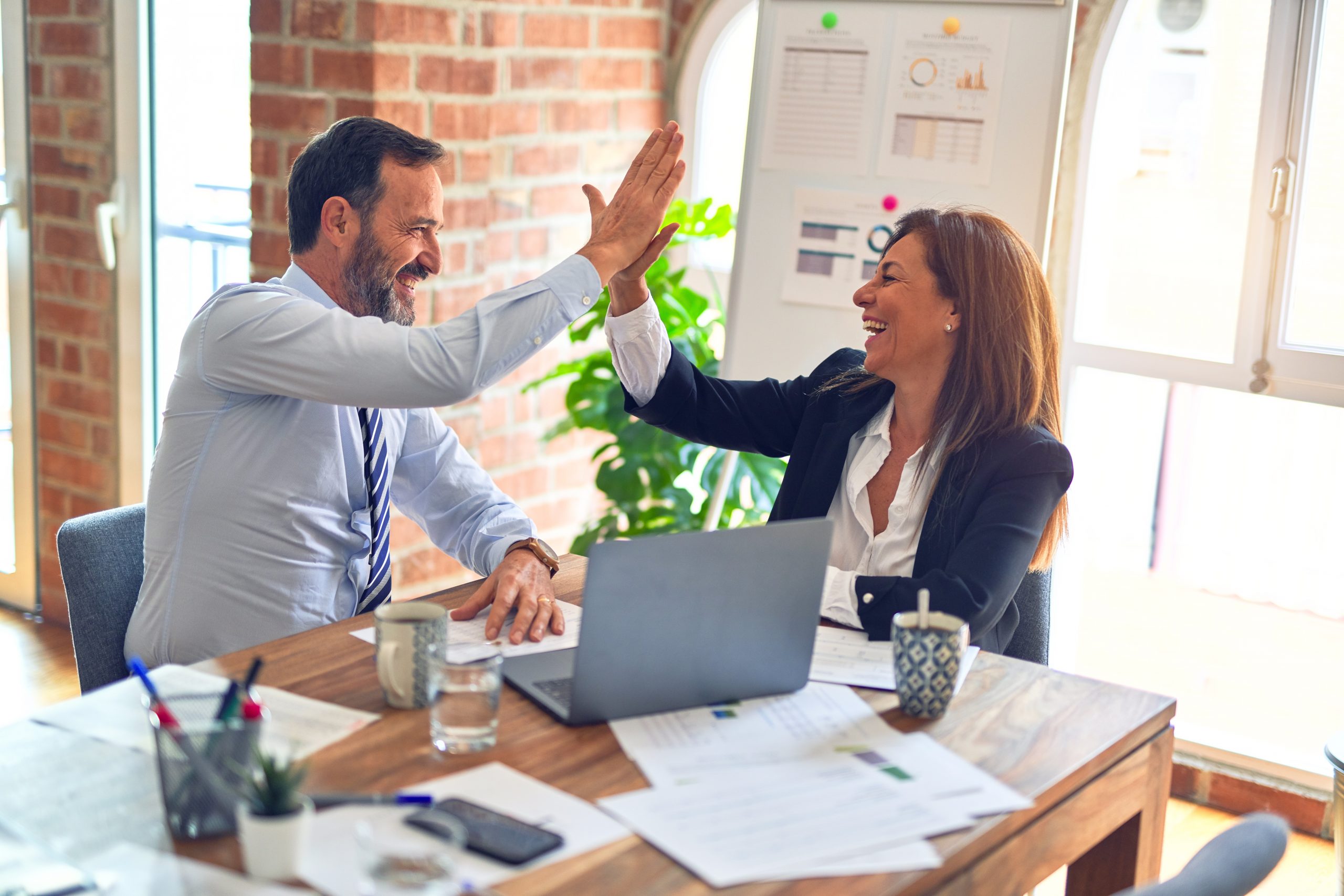
Teach people about Lean manufacturing. That is what the U.S. Air Force asked me to do. OK, but before I could teach it, I had to learn what Lean was. I grabbed some books and started putting together a basics course on Lean, which they wanted done in two weeks. I was surprised at how little there seemed to be to it. Then I discovered how easy it is when talking about Lean principles to fall into a good/bad, black/white mindset. But life is rarely that straightforward.
I knew I was in trouble when my one of my brightest students…who was already running successful Lean projects at his site, said to me on the phone one day, “I know, I know…batching is bad.” I realized at that point that though the basics of Lean seemed so simple on the surface, there is a fair amount of complexity involved in why they work (or do not work) in the real world. Let me back up to the beginning, a few years before this phone call.
Teach Lean? Sure, but I Had to Learn It First
I was in put charge of bringing the concepts of Lean to my organization about four years ago. That meant not only being the expert, but designing training courses and teaching Lean at all levels. Having to be that guy was an interesting and terrifying experience. I had taught many courses throughout the years in quality improvement, but I had not heard of Lean before. At first, everything seemed so clear-cut. There were five principles of Lean and seven categories of waste. It sounded to me like all I needed to do was tell people “here are the things you should do (the principles),” and then “here are the things you should not do (the waste).” In a nutshell, Lean means two things:
1. Figure out what value is to be created or provided.
2. Create or provide that value with the least amount of waste.
How much easier could it be? The first several classes of “Lean awareness” were great! I had a little flow exercise, I made jokes, I presented the basics of Lean, and everyone had a good time learning cut-and-dried concepts.
But in the back of my mind, a voice began to whisper something like, “you’re telling them the right things, but not why they’re right, and that’s because you don’t know why they’re right.” That was unsettling, since I was supposed to be the one with the answers. I had to get those answers fast. One thing I saw repeatedly emphasized in all the literature was the need to “go and see” an operation to really understand how Lean can improve a process. This led me to start trying to apply Lean principles in real life….my own real life. For example, I had read, and had been teaching, that in Lean, we must avoid “batch-and-queue” situations, and try to do things in “single-piece flow.” So I attempted to apply this theory was when I was in the kitchen making salads for my family. It was clear that this was a repeatable production process to which I should be able to apply Lean principles.
Applying Lean Principles to Salad Making
“OK, where should I start?” I asked myself. I decided to just examine the concept of flow in my salad production. What was my current state? “Hmm, I grab one ingredient, and while I have it out, I add that ingredient to all the salad bowls in progress.” I realized I had a classic batch-and-queue technique, which according to the books, and my class, was bad. “No problem,” I told myself. I’ll simply change it to single-piece flow and Lean this process out.
But as I started thinking about what that would mean, it became clear that it was going to be ugly. Single-piece flow would mean I would add every ingredient, one after the other, to the first salad bowl, and complete that salad (so it could flow), before working on the second salad, and so on. This kind of set-up would require me to leave all the ingredients out in the preparation space until the last salad was done.
This did not seem logical, but I was prepared for that reaction. All the books say that Lean feels wrong. And boy, did this feel wrong to me. But it would be Lean if I did it the new way, right? After all, single piece-flow is better than batch-and-queue…or is it? Dang, it was my first crisis of faith. The answer was clearly no! There would be no benefit to single-piece flow in my process. Suddenly I began to panic. How could the Lean way be the wrong way? How can I teach this stuff if I don’t believe it myself? “OK, calm down,” I told myself. “Let’s think about this for a second.”
Why does the Lean literature say batch-and-queue is bad? It all boils down to this: If something is waiting because it is part of a batch process, it is not flowing down the line to the next operation. Short lead times are beneficial in manufacturing for many reasons. Errors surface faster, work flow can be made smoother and more predictable, work-in-process (WIP) inventories can be reduced, and best of all, customers get their orders filled faster. So how do we get shorter lead times? One way is to reduce batch sizes…all the way to a size of one (single-piece flow) if we can, which we usually do by moving operations physically close together so an operator can finish one piece and move it along to the next operation. If we can achieve this, we will have a fast operation with minimal inventory…Lean and mean. It is not easy, but that is the goal.
Avoid Batch-and-Queue Situations, Unless…
However, as good as that all sounds, it depends on one thing being true…that there is inherent value to short lead times. Are there situations where that might not be true? Uh, yeah. Mine. We eat our salads at the same time, in other words, in a batch! If I finished one salad before I start the others, it is just going to sit there until I finish all three anyway. Going back to the two basics in Lean, I started by asking “what value is being created?” In my process, the answer is not “as many salads as fast as I can,” like it would be in manufacturing. The answer in my kitchen was “three salads all served at the same time.” Also, there was only one person in my operation, unlike in commercial manufacturing. So there would not be another worker downstream in my process to whom I could pass partially completed salads. The concept of batch processing had little impact on the “Leanness” of my process at all.
Whew! First crisis of faith averted. Once I had a good grasp on why batch-and-queue is maligned in Lean literature, it became clear how it did or did not apply to me.
So it was not that Lean does not work, which is what I was so worried about. It was that the concepts of Lean, which appear so simple, are anything but. Sure, they are easy to explain, but they were developed as specific tools to fix specific problems. If you do not have that problem, you might not need that tool! A hammer is for pounding in nails. If I had a specific problem involving, say, screws, I would not throw my hammer away. I would simply use the other tools in the kit to fix what is wrong.
There is one rather obvious fact I should mention here. The reason why some things are done in batches in the first place is that it seems to make sense to do a group of things as long as you are…using a certain set-up, in a particular place, holding a certain tool, etc. For example, it feels like it makes sense to make, say, all the green parts of something as long as you have the green-making tools set up. Or I might as well hammer everything that needs hammering as long as I have the hammer in my hand.The waste comes in when that logic stops something from flowing that should be flowing.
Then, Is Batching Bad? It All Depends…
However, if doing things in batches does not stop flow in any way, then it is the best way to do something (assuming safety and quality do not suffer). For example, if it takes the same amount of time and resources to move or process five widgets as it does for one, you should move or process five. If simultaneous work takes the same amount of time as sequential work, then it will probably be faster. The danger comes in when you forget that even though it is just as fast to move five widgets at once, if widgets one-through-four have to wait on widget number five to be ready, flow (for the first four widgets) is suffering. It is all a balancing act.
So let us pose the question again: Is batching bad? The answer is: It depends. If you can then answer the question, “it depends on what?” you’ll start to see that Lean is much more subtle and multifaceted than the seemingly simple elements and tools might imply.
By the way, just because my salad-making process did not suffer from the specific batch-and-queue problems I mentioned, there were still many Lean improvements to be made.