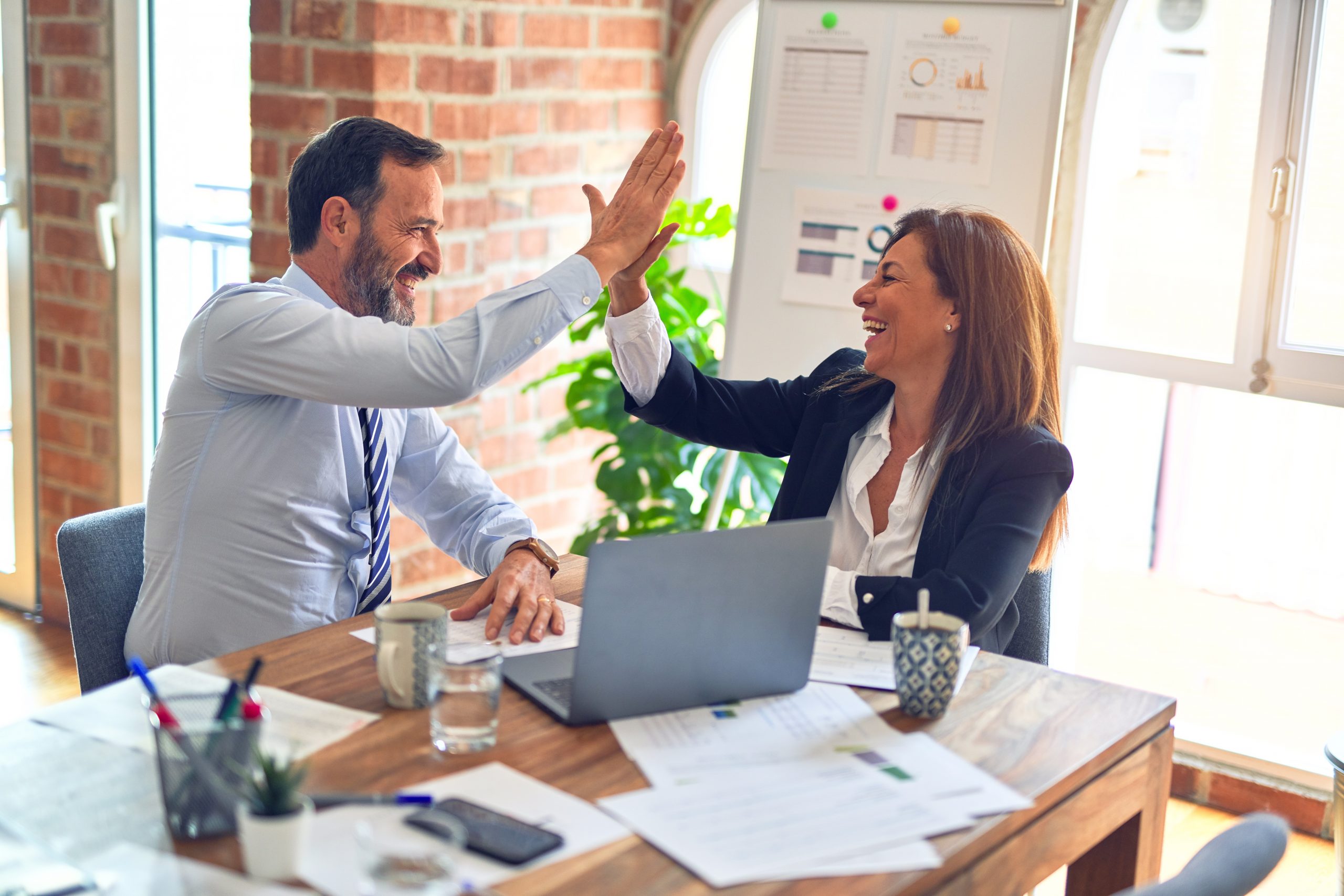
Why create a thought map? What are the benefits? What common mistakes occur, or challenges may be faced, if a thought map is not used?
Using non-statistical tools as well as more complex statistical techniques such as DOE (design of experiments) and SPC (statistical process control) can improve processes and products. A potential shortcoming in using these methodologies is that often they are positioned within an artificial framework or roadmap more commonly referred to as a “model for continuous process improvement.” The common element shared within frameworks and/or roadmaps is that they are sequential in nature – which can cause limitations in thought and work. Although most questions, ideas and thoughts are generated in a random fashion, there is a tendency to structure these in a sequential framework. Their backbones of parallel thinking is a critical asset in identifying key areas associated with work to improve a product or process. The thought map is beneficial with any focused work activity – to document questions, record paths taken in obtaining solutions, the resources required and the solutions obtained.
What Is a Thought Map?
A thought map is an on-going documentation of existing knowledge, the questions asked, the parallel paths of work needed to answer those questions and the tools applied to answer those questions. The thought map is also documentation of the knowledge gained from the project and the direction of future work.
There is no right way to construct a thought map, because there are multiple ways to improve understanding and new knowledge. And while there are no step-by-step guidelines to building a thought map there are guidelines and critical elements to follow:
- Consider major alternatives and initial questions.
- Have a quantifiable objective of the project or process work being undertaken.
- Be aware of parallel paths of questions and subsequent work.
- Prioritize questions to be answered.
- Acquire the tools and methodologies to answer questions.
- Maintain a history of work performed to obtain answers.
- Document answers to questions.
- Record how the metrics evolve in relation to the work performed.
The Benefits of Thought Mapping
Thought maps require the documentation of information most often retained in employees’ minds, or rather, those who own the process and work closest with it. Evaluating the logic of their thinking and actions with respect to the goals and objectives of the work is the evolutionary nature of the work. The benefits of thought mapping include:
- Expressing unanswered questions prior to proposing solutions.
- Documenting and maintaining parallel questions and ideas. As the mind generates multiple questions about different issues within seconds, a majority of these questions and ideas are lost.
- The “best” solution is obtained because multiple approaches are considered and appropriately evaluated.
- Providing a structure for sequential work within parallel paths and thoughts.
- Providing an excellent mechanism to communicate strategies, tactics and activities to peers, other functional areas, suppliers, customers and management.
- Describing the scope of work required to obtain effective solutions.
Common Mistakes in Thought Mapping
Sub-optimal or incorrect solutions with regard to product or process improvement are a result of three common mistakes.
- Starting with one proposed solution as opposed to investigating alternate paths and knowing which questions need to be answered is a common mistake. In an assembly line process if an engineer is tasked with increasing the capacity at a bottleneck, he may try to justify the purchase of new equipment when his primary objective should be to understand the critical “Xs” contributing to the performance in the assembly line location.
- Using existing historical data as a basis for improvement is another mistake. The historical data most likely came from a sample designed to answer a specific question. It is rare that historical data sets will provide sufficient and relevant information regarding current problems.
- To kick off a project using a standard set of statistical tools just because a group has used them in the past is another mistake in process improvement. Figure 1 shows a typical flowchart used in process improvement. This roadmap assumes statistical process control (SPC) is the appropriate tool for any improvement activity. Collecting data is one of the first steps. What questions are driving the need for process investigation? What paths should be considered – materials, design, outsourcing? Are the relationships among process variables or Xs and process performance understood? Without considering these questions, the statistical and/or technical tools will yield weak and irrelevant information.
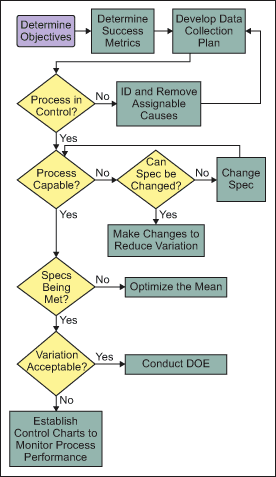
A closer look at the flowchart in Figure 1 shows that a sequential path of activities is frequently associated with the use of statistical and quality improvement tools. This is ingrained in the Six Sigma community. A portion of Green Belt training deals with the concept that a roadmap or flowchart will provide the “right” solution to any problem. More often than not, however, it is not the roadmap or formula that leads to the solutions, but the questions that are asked. If the goal is to obtain innovative solutions, think outside of the box and think sequentially.
To improve products or processes program managers must individualize technical or statistical tools. “Does it pass the giggle test?” As illustrated in Figure 2, existing knowledge, ideas and/or suspicions drive questions, which drive the type of information needed and work pursued (SPC, DOE, etc.) which provide answers that supplement existing knowledge and lead to new questions.

Why do Thought Maps Fail?
Using thought maps in the technical or engineering communities typically generates one of two responses – they find them extremely beneficial and powerful, or they fail to understand the relevance of the map to their work. Thought maps are extremely powerful tools, but two primary failure modes often affect their usefulness.
- Thought maps are treated as a static document, completed and left as is throughout the project work. This is an evolutionary process – the map document serves as a guide for a work project by documenting questions that need answers.
- Thought maps are not created with explicitly defined questions and theories. The work is not guided by rational and logical questions for defining data collection strategies and choice of analysis. Design the data collection and analysis to answer specific questions. Do not develop a thought map after collecting the data. If the conclusion is unclear after thought mapping consider the following questions:
- What questions need answers?
- What sources of variation are necessary?
- How was the data collected?
- How was the experiment set up and with what factors?
- How were the factors selected?
Conclusion
The greatest asset to any organization is the ability of its employees to think rationally, logically and creatively. Although there are improvement models intended to fuel creativity, if done incorrectly they too smother creativity and innovation. Past improvement activities have been forces designed to “fit within the box.” Think of a current rewards and recognition program and/or what motivates workers. Workers are encouraged to “check the box” on the list of tools and/or techniques applied to projects. Instead of business as usual and “fit the box” techniques, asking and answering the right questions is the basis for mapping thoughts and sequential knowledge building. To develop and test theories, and to understand and document untested assumptions are keys to success. Thought maps improve communication, idea generation, tool application effectiveness and, ultimately, problem resolution efficiency.