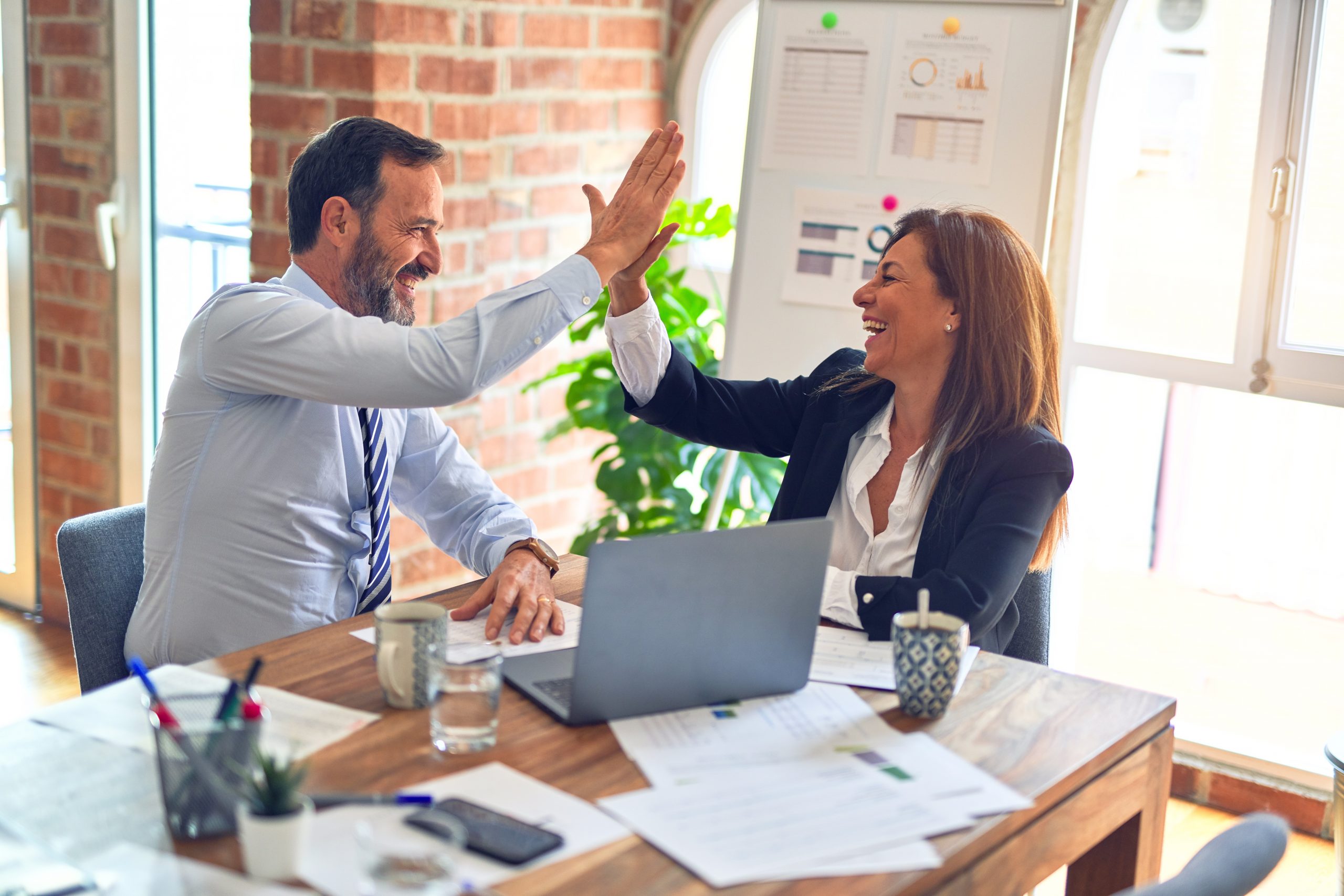
“Every defect is a treasure, if the company can uncover its cause
and work to prevent it across the corporation.”
– Kilchiro Toyoda, founder of Toyota
When people discover problems, the most frequent response is to rush to find a solution. Finding an immediate fix for the problem is very satisfying no matter how many times this process occurs. Unfortunately, it is not the best way to solve a problem, as it leads to the need to solve the same problem over and over again. A better approach is to eliminate the root cause.
The Six Sigma DMAIC methodology provides an effective way to accomplish this goal:
Define and Measure the Problem – What does the company want to prevent from recurring? When and where did it occur? What is the significance of the problem? The first step in the process is to define the problem. This is done by comparing the expectation of the customer to what he/she currently receives. Closing the gap between expectation or the voice of the customer (VOC) and reality or voice of the process (VOP) defines the problem.
Analyze Cause-and-Effect Relationships – Once the problem is defined, it is important to uncover the root causes of the problem and to understand how they interact with one another. Collect a sample of data related to the problem and conduct a root cause analysis to identify the reasons why the problem exists. This analysis will form the basis for determining solutions that will prevent any recurrence of the causes, and ultimately, the problem.
Implement and Control the Best Solutions – Identify solutions based on the results of the root cause analysis and perform a cost/benefit analysis. Solutions are specific actions that control root causes of the problem. Implementing the right solutions and controlling or monitoring the results will keep the problem from happening again. The best solutions are those that prevent problems from recurring, are controllable and meet the needs of the client.
DMAIC Problem Solving
One of the most important steps in the DMAIC process is the root cause analysis. This is where the real cause of the problem is uncovered. Many problem-solving processes applied without the benefit of the Six Sigma methodology, result in managing a symptom of the problem rather than eliminating the root cause of the problem. The root cause is one that, if corrected, would prevent a recurrence of the problem. There may be a series of causes that are identified, one leading to another, or more than one cause that combine to create the problem.
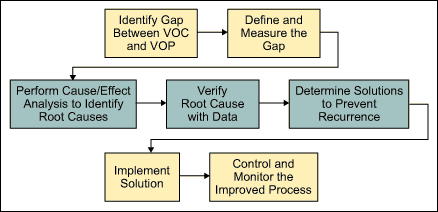
Problem Solving Is Just Common Sense?
Alexander Dunn, director of Assetivity Properties Ltd., in a paper posted on the Maintenance World website, quotes a study which showed, “…that, when trying to prevent unacceptable events from happening again, 10 percent of participants immediately sought to place blame, 26 percent immediately expressed an opinion of the causes and offered an opinion without investigating the problem, and only 20 percent of participants examined the problem in sufficient detail to be able to identify an effective solution.” From these statistics, its clear that effective problem-solving is far from common sense.
Root Cause Analysis Template
A root cause analysis template with this article provides a helpful way to structure a search for root causes, document the process and communicate the results.
Indeed, “Research has repeatedly proven that unwanted situations within organizations are about 95 percent related to process problems and only 5 percent related to personnel problems. Yet, most organizations spend far more time looking for culprits than causes and because of this misdirected effort, seldom really gain the benefit they could gain from understanding the foundation of the unwanted situation,” according to Gene Bellinger, who writes on the web site Systems-Thinking.org.

As a simple example, picture a large block of very good Swiss cheese on a kitchen table a few feet away from an open screen door. The weather outside is warm. A man comes to the table for some wine and cheese and sees a mouse in the cheese.
Problem: There is a mouse in the cheese.
Solution: Throw out the cheese with the mouse and put a new block of cheese on the table.
That is not the Six Sigma way.
To do a root cause analysis of this situation, follow the DMAIC approach. The analysis might look like the graphic on the left.
Notice that solutions such as, “Be sure to close screen door,” or “Put a note on door asking, ‘Did you latch me?'” are not good solutions. They might work but they will not prevent the problem from recurring. A spring latch is a sure solution.
 “Every problem is an opportunity.”
– Kilchiro Toyoda, founder of Toyota