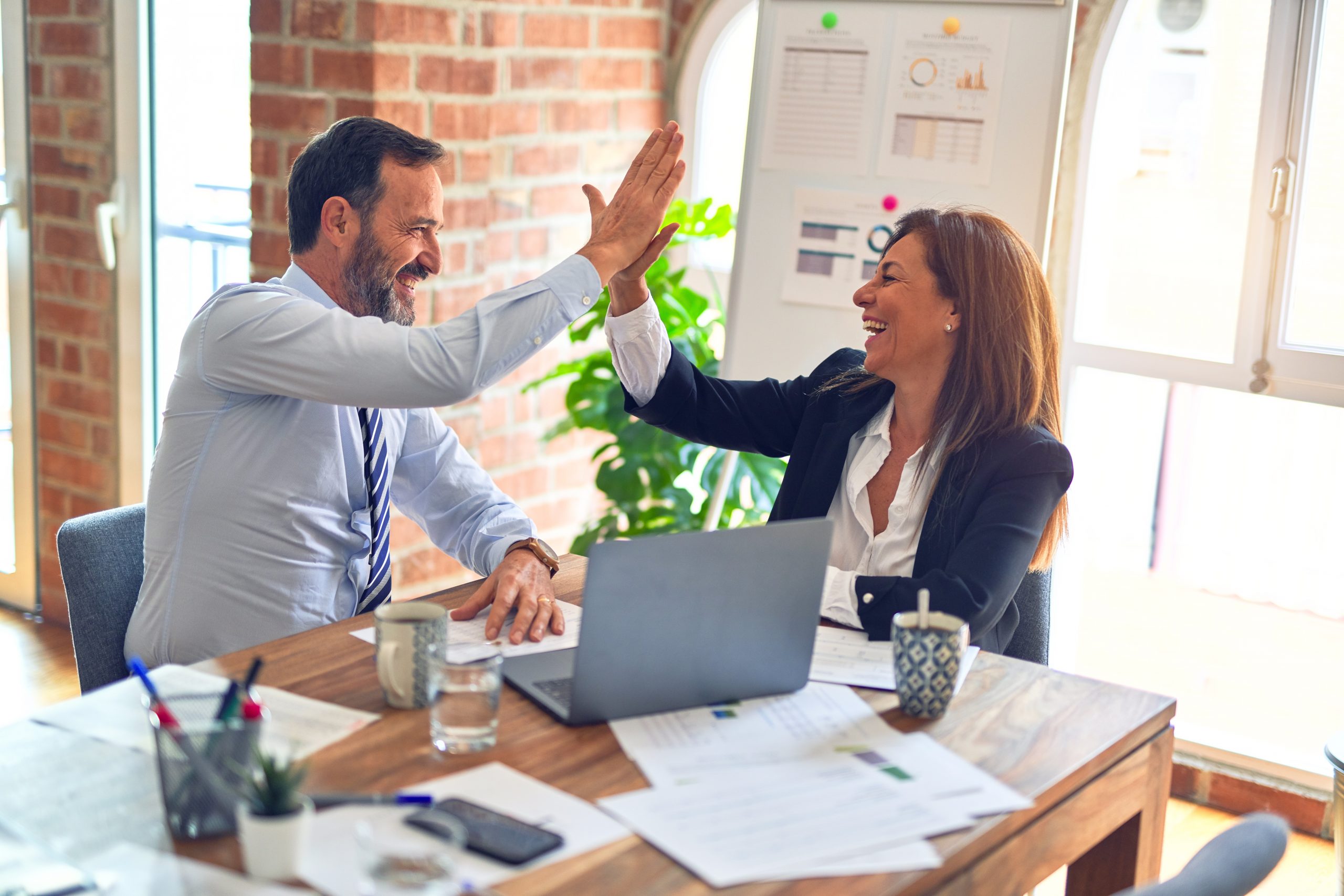
The organization described in this case study is a large insurance company headquartered in the western United States that began exploring Six Sigma about three-and-a-half years ago. The deployment included software development organizations across five regions and was initially driven by vice presidents. The company engaged a Six Sigma consulting firm to lead the effort.
The Story
The outside consultants drove Six Sigma strategy, training and coaching. Internal Black Belt candidates were selected and trained from across the organization. Projects were selected from critical organizational issues, some more than 20 years old. Black Belt candidates drove these projects, with coaching from the Master Black Belt consultants. Organizational leaders were chosen to own and monitor projects in their areas, and weekly and monthly status meetings were held to report on progress and issues. Many projects were slowed or cancelled due to a lack of usable data for baselining and analysis. Inflow of project ideas was always an issue for the group.
One-and-a-half years after initial deployment, a Green Belt program was initiated to supplement Black Belt activities on smaller projects, and Lean thinking, training and approaches were added to the ongoing Six Sigma effort. Internally developed Master Black Belts began taking over for outside Belts as consultants were trimmed.
Deployment Results
Over approximately 39 months, 184 projects were measured and analyzed. Compared with baseline measurements, the number of problem reports, cost of development and cycle time all decreased after completion of the Six Sigma projects. Productivity (measured in thousands of lines of code produced per person per month) and defects found per unit of time relatively increased. The percentage of schedule and cost overruns also decreased significantly relative to baselines.
Drivers and Roadblocks
The table below lists the particular driving and constraining forces that helped and harmed this deployment. These forces, and the stages of the deployment they impact, are explored in following sections.
Implementation Driving and Constraining Forces | |
Driving Forces (+) |
Constraining Forces (-) |
CEO initiated and drove implementation | Resource availability low and stressed |
Experts pulled in to lead and mentor | Culture of ‘not invented here’ dominant |
Solid approach to Six Sigma provided | Need for Lean dominated processes |
Black Belts selected, trained, groomed | Black Belts often selected for wrong reasons |
Green Belts added to support plan | Green Belts added to program too late |
Key process issues selected for work | Usable data seldom available for projects |
Solid financial results delivered | Victory declared prematurely |
Internal leaders taking over program | External experts discontinued too early |
Hints for Early Stages of Implementation
In this type of deployment, senior management support and participation should be evident at all times. Companies also should partner with the right consultants and mentors. In this case, the company may have hurt itself by initially hiring external resources who:
- Did not introduce Lean concepts in the early stages of deployment.
- Implemented Six Sigma separately from Lean in order to drive additional consulting needs later.
- Did not have a software background.
During early stages, it is also important to get all employees some initial orientation in Six Sigma (about 4 hours). At the beginning of this deployment, only Black Belts and Champions were trained, and as a result, team members were not sure of their roles and responsibilities. Also, potential project inflow was reduced because the general population was unaware of what Six Sigma really was. Although management and leadership orientation is critical, training for support personnel is valuable so they can support the program’s needs.
Software organizations should consider hiring a few external Black Belts for hands-on support. The company in this case did not hire any outside Black Belts. The plan was to develop all Belts internally. This slowed initial progress and provided no internal, local hand-holding for new trainees. Green Belt training also proved an issue, as it did not begin until one-and-a-half years into the deployment. An earlier focus on Green Belt training would have provided a better selection pool for potential Black Belts. Green Belt projects also can help the effort by addressing small but critical needs that are often overlooked because of the smaller dollar returns from such projects.
Along these lines, selecting the right projects is another key element for success, one that this company did not immediately capitalize on. Project selection should be based on:
- Real need or pain – There are always obvious projects that should be addressed first. These typically can add value in areas of known issues that have been begging for help over many years. These early successes can stimulate interest and demand for additional Six Sigma efforts.
- Data availability – Avoid taking on projects without good data available until later in the implementation cycle. Such projects can kill progress and turn people off to the ideas of Six Sigma. Save these more frustrating projects until later.
Another tip for early success: Advertise a new Six Sigma program repeatedly through:
- Senior leadership visibility and involvement
- Internal publications
- Home pages or internal websites
Following Through During Middle Stages
Once the deployment is off the ground, it is important to continue the key early-stage practices – these basics must always be in focus. However, there are new steps to implement at this phase:
- Publicize early wins to gain support and momentum.
- Select stand-out Green Belts for Black Belt training.
- Deliver appropriate Black Belt training with good examples of software applications embedded throughout.
- Mentor new Black Belts with combined internal Black Belt and external Master Black Belt leadership.
- Use common, automated tools to track and house project templates and deliverables.
Companies have a tendency to declare victory to early, which can be harmful to the effort. Some signs that an organization is moving too fast:
- Moving from hands-on to virtual – As costs become an issue, organizations sometimes move to online training and coaching-by-phone, which can give a false sense of security.
- Eliminating outside support – Again, for cost purposes, companies often release outside consultants before internal Belts are fully prepared and stability is attained, leaving Belts over-stressed.
- Reshaping the program – Some organizations who worked with outside experts to help implement Six Sigma quickly declare themselves experts and embark on a “not invented here” process of butchering the program. Failure can ensue.
This middle stage is a good time to establish an internal center of excellence for Lean Six Sigma to focus and add cohesiveness to the efforts.
Maintain Progress in Late Stages
As a deployment progresses, organizations should continue the key early- and middle-stage practices, but also make more advanced developments. These include:
- Selecting a few stand-out Black Belts for Master Black Belt training.
- Delivering appropriate Master Black Belt training.
- Grooming Master Black Belts for Black Belt, Green Belt and Champion training delivery, as well as coaching and mentoring.
Now the organization may be weaned away from external consultants. This timing should be based on organizational readiness, not budget-reduction needs. At this time the firm should document best practices and lessons learned to share with other internal organizations.