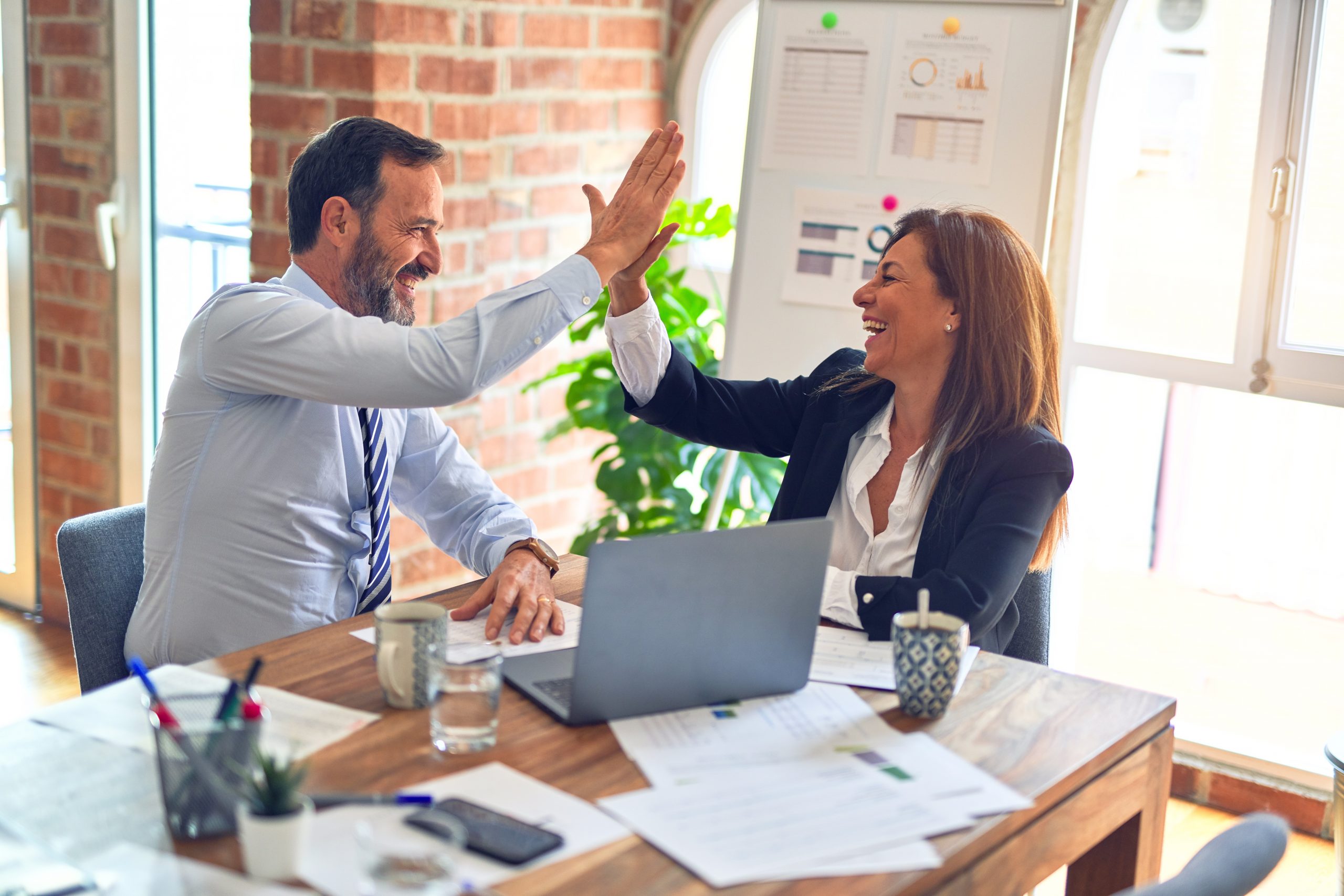
A Six Sigma project at a medical transcription company in India for U.S.-based customers first debunked the myth that output quality variability cannot be systematically improved because of the inherent variability of input quality and human skills. Then, encouraged by the results, the company launched a second phase of the quality movement to consolidate learning, spread the quality mindset and vigorously pursue further improvement.
This case study looks at the seven steps of problem solving accompanied by discussions of the application of the Six Sigma techniques relevant to the problem. Special attention is given to critical points at which major mindset changes occurred.
Step 1: Defining the Problem, the Metric and the Goal
Defining the Problem – A meeting of the company’s senior management was conducted to select the project theme, or the top critical-to-quality elements (CTQs). A brainstorming session produced a long list of problems. These were separated into two categories:
- End-result problems faced by external customers.
- Internal problems that were causes of customer problems, rather than basic problems themselves.
Because the managers had a customer-focus, the realization that end-result problems were the real problems came spontaneously. Prioritization, using a weighted average table, followed by a quick discussion established the main concerns as “consistency of quality and timeliness.” The medical transcription business consists of receiving dictations from doctors, transcribing them according to set rules, editing the output for errors and transmitting it back to the sources of the recordings. An initial project addressed the issue of timeliness; this one addressed consistency in quality.
Within the theme, management selected a particular company location and customer line for a pilot project. The managers defined what customers wanted as the industry standard of 1.5 errors per 100 lines.
Defining the Metric – For ease of analysis, the metric was modified to errors per 1000 lines (EPT). With the new metric, the customer desire became less than 15 EPT.
Without an understanding of variability and sigma level, an average below 15 EPT for any reporting period or batch was considered satisfactory. The concept of sigma was introduced to define:
3-sigma quality equals average + 3 sigma < 15 EPT
6-sigma quality equals average + 6 sigma < 15 EPT
Immediately it became clear the average had to be <15 EPT for the above to be achieved. The concept of sigma began to sink in.
The current status was explored in a Pareto diagram of errors identified during a 30-day period. It revealed that the general category accounted for 40 percent of the errors. That indicated the need to redefine error categories. A new classification was developed, breaking up the general category to provide greater resolution.
While analyzing errors it was discovered that a weighting factor, unknown to the customer, was assigned to different error categories. Since weighting factors imply greater care for highly weighted categories and it is impossible to produce different standards of quality for different categories simultaneously, it was suggested that all errors be considered equally. Using these rules, and an appropriate batch size, the current state (batch average and sigma) was ascertained for one month.
Average + 3 sigma equals X EPT was found to be significantly above the desirable levels.
Defining the Project Goal – The initial objective was to reduce X by 50 percent.
Step 2: Finding the Root Causes
A brainstorming session for possible causes revealed that 60 percent of the causes were classified as “uncontrollable or external.” Further, any discussion to isolate systemic causes invariably dead-ended around the uncontrollable causes. For example, two killer external causes often referred to in the medical transcription industry are “listening skills” and “difficult dictator accents.”
To segregate errors with systemic rather than uncontrollable causes, a special test was designed. Eight editors were asked to edit the same set of files. The compilation of errors overlooked by the editors showed that 80 percent of errors were overlooked by more than 50 percent of the editors. This proved to be an eye-opener – no longer could “listening skills” be cited as a predominant cause. Further it was recognized that even for external causes, countermeasures would need to be developed if quality was going to improve. Repeating the test four times produced similar results. The critical mindset change from “We can do very little about these errors?” to “How do we stop these errors?” had occurred.
An experimental process permitting audio replay of files was developed to enable team analysis of root causes. An intense discussion – in which there were repeated reminders that errors missed by more than 50 percent of the editors must have reasons and solutions – eventually established that 87 percent of such errors had just four root causes – process step omitted, speed accent, knowledge error, and lack of judgment training.
Step 3: Idea Formulation for Countermeasures
Discussions of each of the four vital root causes revealed just three vital countermeasures – ensure process step, customize judgment training, foolproof software – accounted for 88 percent of all errors. The process of identifying causes and countermeasures became easier and easier as the exercise progressed. The final output is summarized in Table 1.
Table 1: Causes and Countermeasures | |||||
Cause |
Countermeasure |
Occurrence |
Cum. |
% |
Cum. % |
1. Speed accent | Customize judgment training |
14 |
14 |
25 |
25 |
2. Audio | Customize judgment training |
1 |
15 |
1 |
26 |
3. Judgment training |
Customize judgment training |
5 |
20 |
9 |
35 |
4. Process step omitted | Ensure process step |
20 |
40 |
35 |
70 |
5. Knowledge error |
Foolproof software |
10 |
50 |
18 |
88 |
6. Wrongly classified as error | Not an error |
5 |
55 |
8 |
96 |
7. Other errors | ? |
2 |
57 |
4 |
100 |
While recognizing that all measures proposed might not be 100 percent foolproof, it also was acknowledged that a target of 50 percent error reduction seemed within reach.
Since regular measurements, error and mistake proofing, feedback, training and implementation take time to introduce and sustain, control charts and regular analysis were introduced while testing and implementation were still in progress.
Step 4: Idea Testing and Modification
The two most vital countermeasures were tested to confirm the results with customized tests.
Ensure Process Step – In the company’s two stage-transcription checking process, the second stage was being omitted leading to the category of errors labeled “process step omitted.” A set of files was subjected to careful comparative testing to confirm the hypothesis both at the transcription and editing stages. The eye-opening results are shown in Table 2.
Table 2: Comparative Testing of Hypothesis | |||
SO: T – Yes |
SO: T – Yes |
SO: T – No |
SO: T – No |
SO = step omitted T = Transcriptionist |
The results emphasized the need to go back to basics. The transcriptionist must follow the two-stage checking process. The editor is, at best, a polishing function. They challenged the perception that the more skilled and experienced editors would take care of quality even for below-standard transcriptions. Further, they reaffirmed the well-known Six Sigma philosophy, “Prevent defects closest to the point of creation.”
Judgment Training – This was the fix for errors which often occurred due to hard-to-understand voice recordings. Traditionally these errors had been the “imponderables” of medical transcription where human factors of listening skills inevitably would lead to inconsistencies.
The analysis, however, produced a very interesting perspective. Accepting that there would always be difficult files and only very few employees with exceptional hearing skills, the process stipulated that cases of “reasonable doubt” be referred to those endowed with exceptional hearing skills. A test confirmed that the exceptionally endowed employees produced only two percent errors. The root cause was therefore not “difficult voice recordings” but poor judgment in when to refer a case.
A customized training process was devised among a batch of transcriptionists and editors. They were asked to listen to difficult recordings and to fill or refer them. From initially adventurous guesses, gradually their judgement was tempered until the percentage of correct responses increased four-fold from 20 percent to 80 percent.
Step 5: Implementation of Countermeasures
Implementation involved training personnel using specially prepared sessions to explain the measurements, reasons for change, and what was expected of them. This was followed by an exercise in which they actually experienced the results with and without the countermeasure so that conviction about the new process was internalized.
Step 6 : Confirming the Results
Even as the training was in progress, a noticeable reduction in errors began to occur, as shown in the figure below

The monthly batch average + 3 sigma had reduced by at least 50 percent and in the best month – June – by 75 percent.
Step 7: Compilation of the Quality Improvement Story
The story of change was compiled and presented to senior management highlighting the need for the following:
- Develop software to help foolproof knowledge errors at the source – potential 18 percent error reduction.
- Make permanent a daily cycle of identifying and attacking root causes of the most frequent errors of the previous day. This will be a way to ingrain the continuous improvement habit.
- Develop a metric to regularly ensure that process steps are not omitted.
It is estimated that with the consistent implementation of these countermeasures a further reduction of 50 percent is achievable. This would result in a total reduction of 80 to 90 percent from the pre-project level.