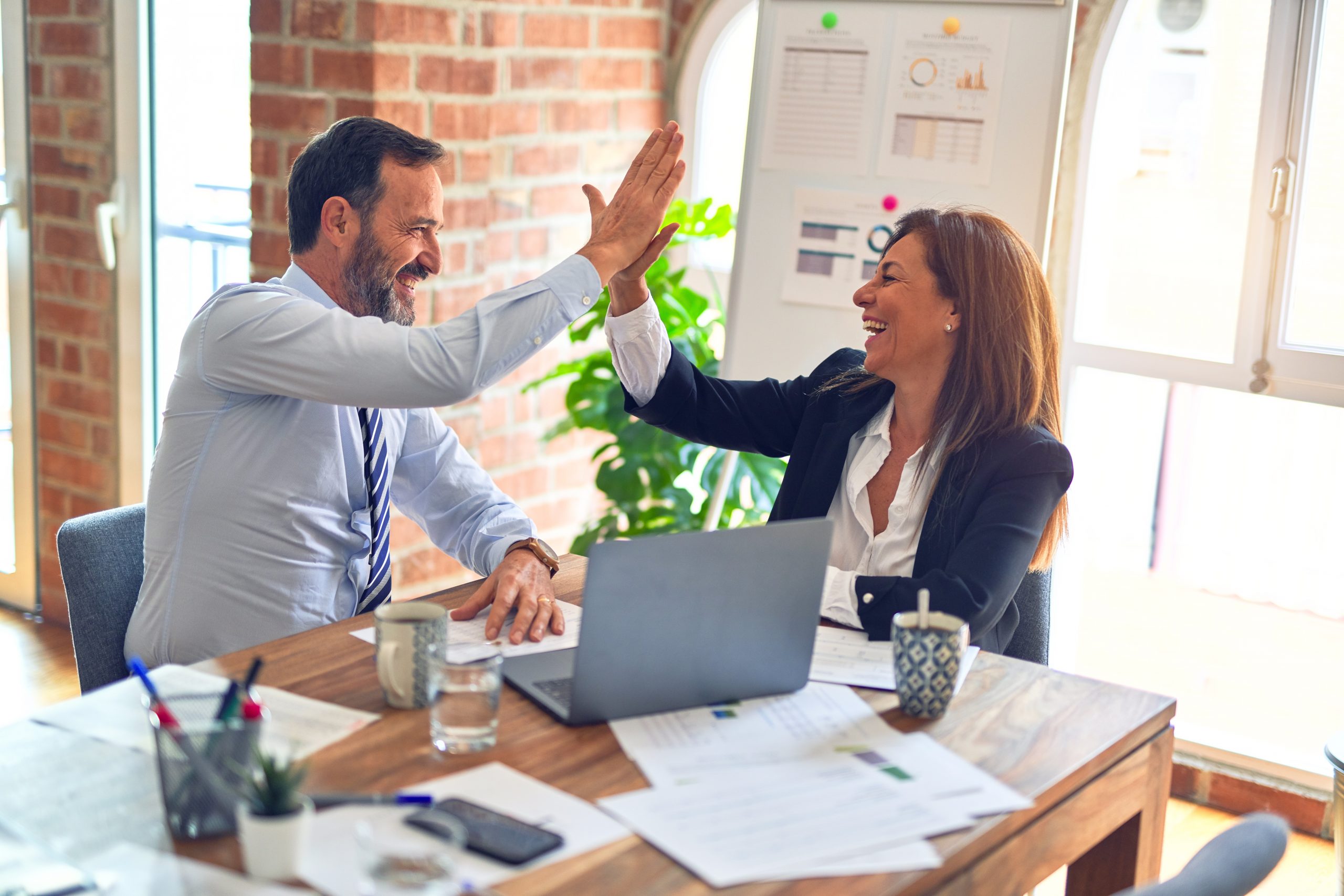
Since launching its Six Sigma program in 2001, Decatur Memorial Hospital has trained a team of Green Belts, Black Belts, Master Black Belts and change agents, and completed projects that have led to increased quality and efficiency across the organization. And despite being four years old, the program remains vital with a high energy level. In fact, the leadership team has invested significant time during the last year redefining and aligning Six Sigma and Lean projects with the hospital’s strategic objectives.
Aligning People, Projects and Priorities
In selecting projects, Decatur Memorial not only looks at the likelihood of success, the leadership team also examines the most strategic areas of the organization to find improvement opportunities with a financial impact and that can positively affect the quality of care. As part of the increasing emphasis on aligning Six Sigma projects with organizational objectives, leadership is encouraging a focus on “noble goals,” or concentrating on efforts that support a noble purpose. Examples of such noble goals include becoming a top performer with respect to raising patient satisfaction (as measured through Press Ganey), eliminating any medication errors, and preventing all hospital-acquired infections. Results are then included in the hospital’s scorecard.
Decatur Memorial Hospital has been able to achieve and sustain success with its initiative because the organization’s leadership views continuous improvement as part of an overall framework for creating the best healthcare environment possible. Complementing education in Lean, Six Sigma and change management, hospital employees go through four days of “Imagine 21” training. Imagine 21 training encourages people to think about their goals, understand how they respond to change, and evaluate how their personal views inhibit optimal performance both in their personal and professional lives. With 65 percent of the employee group through the training, the comprehensive curriculum is helping everyone understand that their lives can be better than they ever “imagined.”
About Decatur Memorial Hospital
Located in the heart of central Illinois, USA, Decatur Memorial Hospital is a rapidly growing 300-plus-bed, community-based hospital. It employs approximately 2,500 fulltime equivalent employees (FTEs) and averages about 13,000 patient discharges annually.
The hospital recently opened an emergency care center, started a “hospitalist” program and opened a new ortho-nursing unit for post-operative care of orthopedic patients.
Decatur Memorial Hospital has a state-of-the-art heart program offering options in care not previously available in central Illinois. The organization includes numerous outpatient service facilities offering rehabilitation, imaging, home health, wellness, urgent care and a separate occupational health facility.
Preventing Infections
One of the hospital’s primary goals involves ensuring patient safety – specifically eliminating nosocomial or hospital-acquired infections. This is one of the key indicators Decatur Memorial has tracked for several years, and the Six Sigma team launched several projects that target this important area of clinical quality.
Toward the end of 2003, a project was scoped to focus on reducing nosocomial infections in three key operational areas – intensive care, intermediate care and the cardiovascular unit. The project was successfully completed and the hospital has been able to sustain its improvements.
Another project, launched in August 2004, focused on the reduction of surgical site infections. Now in the Control phase, this project was scoped to include all total joint replacements for hips or knees. With the project completed and improvements in place, there have been no nosocomial infections for three consecutive months related to joint replacement surgeries.
In completing this project, the team discovered a related issue it wanted to target next. The Centers for Disease Control (CDC) recommends that for certain cases, antibiotics should be delivered prophylactically to the patient in order to reduce or eliminate the risk of infection. The focus is on the length of time between complete delivery of the antibiotic and the surgery or “cut time” on the patient.
The CDC recommends this should be less than an hour, and early analysis by the hospital’s Six Sigma team found that although averages were close, there were variability issues in consistently meeting the recommended guidelines. This project is currently in the Define phase, and progress is being closely monitored.
The data and box plot below illustrate the before and after results for a separate project that focused on improving the timeliness of antibiotic administration to pneumonia patients:
Table 1: Data on Time Until Antibiotic Given | ||
Baseline Measures | Project in Control | |
Mean | 406 Minutes | 111 Minutes |
SD | 954 Minutes | 199 Minutes |
SPMO | 622,000 | 1,000,000 |
Zst | 1.81 | 6.0 |

Working with Physicians
For Six Sigma or any other initiative to succeed in the healthcare area, it is important to find ways to involve physicians without consuming too much of their time. At Decatur Memorial Hospital, rather than becoming a regular member of a project team, physicians often play the role of “consultant” at various stages and offer advice or input to specific processes. Using tools such as the stakeholder or GRPI (goals, roles, processes and interpersonal relationships) analysis helps to determine whether a clinician needs to be involved and at what level (i.e., whether they will participate periodically, receive information on a need-to-know basis or serve as the chief decision-maker).
One clinical project that focused on the acute myocardial infarction (AMI) core measure included a physician as a team member. Though he was not asked to attend every meeting due to time constraints, he was able to provide direction and share unique insights into key parts of the care delivery process. His involvement had a significant impact on the overall success of the project. Since concluding the project, Decatur Memorial Hospital gone several months without any patients failing to meet the AMI core measure standard of care.
The Journey Continues
More than 50 Green Belts have been trained at Decatur Memorial Hospital and every formal project or Six Sigma study has an internal Black Belt assigned to provide mentoring. There is a formal review process once a month, with an administrative group composed of executives, Six Sigma leaders and others who may want to attend and gain insight or provide information on the projects under discussion. These reviews have become an important communication tool within the hospital.
As the deployment continues to mature, the Six Sigma team at Decatur Memorial is developing a Yellow Belt team concept. Yellow Belts are trained on basic Six Sigma concepts (such as the DMAIC [Define, Measure, Analyze, Improve, Control] methodology), and given some basic training in the area of Lean and waste reduction. Then they launch localized projects to improve workflow and conditions within their individual work units.
Six Sigma, Lean and related methodologies have become an integral part of the framework for managing change and improving processes at Decatur Memorial Hospital. Results from the Six Sigma initiative can be seen in higher patient and staff satisfaction, increased efficiency and better service quality. Initially receiving education and mentoring through an engagement with consultants, the hospital has been self-sufficient for some time, providing internal training for staff and leading a wide array of projects.