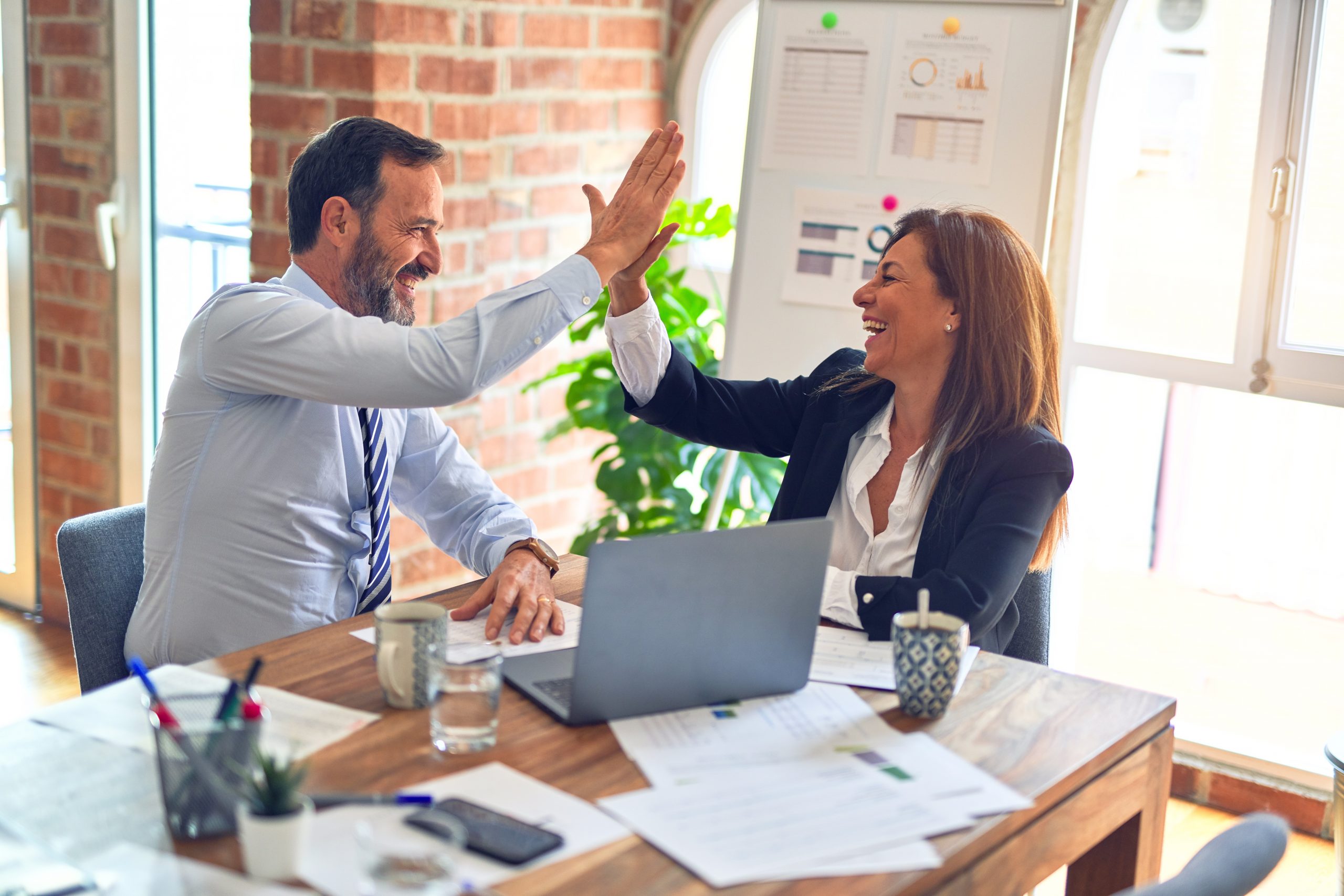
Many people in the private sector are aware that the U.S. Air Force is using continuous process improvement (CPI); however, few may know that CPI is utilized throughout the central command area of responsibility in the Middle East and Central Asia – also known as “the war zone.”
War is never easy, and the fog and friction of war causes frustration, dilemma and chaos. The constant threat of rocket attacks, ground attacks, and suicide bombings is a typical day in the lives of aircraft and munitions maintenance crews. But a remote base in Afghanistan has proven that CPI can be implemented anywhere, specifically in those key processes that can be the difference between life and death. Led by the efforts of the Maintenance Group, the men and women of this remote base have changed the way people approached the mission and the war.
Recognizing the Need for Change
Successful organizations in the private sector need to recognize the need for change before it is too late, and it is no different for the Air Force. When the Maintenance Group was established, the senior leadership quickly realized that they did not have applicable local maintenance governing instructions that were unique to the area. They also were hampered by organizational differences between integrating the active duty and reservist maintenance crews. In addition, the prevailing attitude by most crew members was, “We are at war; we can do what we want.” Recognizing that the status quo was not a way to run an efficient and cohesive organization, senior leadership initiated effective policy deployment and developed a strategic plan, complete with a vision statement, mission statement and objectives focused on two basic aircraft maintenance fundamentals: aircraft availability and munitions support. The development of policy deployment and a strategic plan served as the launching point for the Maintenance Group to begin its CPI journey toward turning the organization around.
Policy Deployment and Strategic Plan Development
An effective CPI journey begins with a strategic plan developed at the top of the organization and deployed down to the men and women carrying out the day-to-day tasks of the mission. One of the initial steps in developing a strategic plan is to define the mission and vision statement. Defining both is never easy and usually leads to intense discussions about what is really important to an organization and what the future should look like.
The Maintenance Group at this remote base in Afghanistan faced no different challenges. A one-day meeting to establish policy deployment was initiated by the commander. For the vision statement, senior leadership decided on “people, planes, processes – mission-focused and right the first time.” Keeping true to this vision enabled the leadership to get focused on what was important and develop the mission statement: “Professional Airmen providing exceptional maintenance and munitions support, anytime, anywhere.”
The next task was to create objectives that each subordinate unit and, in turn, individuals within the organization could strive to align themselves with. Each individual had a different perspective of what needed to be accomplished throughout the next year. The team employed brainstorming techniques and then created an affinity diagram to narrow down the long list to four objectives:
- Develop Airmen to their fullest potential
- Manage fleet health to ensure aircraft availability
- Enhance infrastructure to facilitate maintenance and improve quality of life
- Foster joint and coalition relations to maximize airpower and showcase great Airmen
By the end of the day, the mission statement, vision statement and objectives were all formated into a document and identified as the orgnaization’s strategic plan. The next step for the senior leadership was to deploy the plan throughout the organization.
Gaining Easy Wins
Establishing policy deployment within the organization instantly increased morale among the middle and lower ranks because they now knew specifically what their priorities were and what to begin working on first. Each unit was tasked with creating an “easy win” that aligned to the objectives of the organization and could be showcased for all personnel to see. Based on these requirements, the A-10 unit focused on applying 5S to the A-10 aircraft consolidated tool kit (CTK) support section. A support section is an industrial area that issues tools and parts to support production efforts in any manufacturing area.
The CTK area 5S was a pivotal event to accomplish because of the specific mission of the area – storing tools and equipment utilized by the maintenance crews to fix the A-10 aircraft. It aligned to the objectives of the organization because, under the current layout, crews were taking a substantial amount of time to find the needed tools and equipment to fix and maintain the aircraft (Objective 2). In addition, the increasing workload and decreasing space, coupled with a lack of standard work, were causing an issue with capacity (Objective 3).
Led by an experienced Green Belt, the team, comprised of active-duty and reservist maintainers, sat in a tent with one table and a roll-away white board and began to work. Utilizing a spaghetti diagram, the team gathered the required data by analyzing the current layout and configuration; they also determined what tools and equipment were utilized most often. After a few days of collecting data, the team gathered around the table and analyzed the data to prioritize the frequency with which the maintenance crews utilized the equipment and tools. From there, they constructed a model layout to begin placing equipment and tools strategically, according to utilization. After much discussion, the team finalized a layout and began the 5S process.
Sort: The team shifted through the tools and equipment and determined what was needed and what was no longer required to accomplish the mission. Items that were no longer required were red-tagged and placed in a holding area, while tools and equipment that needed to be utilized were placed in a different holding area. The unnecessary tools and equipment returned to the supply system saved the Air Force $575,000.
Straighten: The team used the model layout created during the data-collection phase to reference and place all applicable tools, toolboxes and equipment strategically, according to the utilization frequency and, to create a future state. For example, high-use items were moved closer to the entrance, which reduced travel for maintenance crews by 460 feet for every visit. The area was remodeled according to the future-state layout, and tape was placed on the ground to distinguish specific locations of equipment and toolboxes. In addition, visual management was created and displayed to provide clear instructions to the tools that corresponded to specific toolbox drawers.
Shine: Even in an austere environment, housekeeping and cleanliness are necessary. Everything in the support section was thoroughly cleaned, and the entire area was washed, scrubbed and dusted. The hangar was pressure-washed. The offices were gutted and plywood furniture was constructed to serve the war fighter.
Standardize: To ensure that the new changes were going to be sustained, the team created checklists to allow the maintenance crews within the unit to consistently inspect the newly renovated area on a daily, weekly and monthly basis. The checklists were developed and placed in books to ensure visibility for all crew members. A continuity book also was written and maintained by the section to ensure consistent messaging as new personnel arrived on station.
Sustain: Audit programs were written into the local instructions, and inspections were performed by all personnel, which were signed-off by the middle-management. Any discrepancies noted during the inspections were briefed during the daily roll call. In addition, audits by the senior leadership were conducted at least quarterly.
These changes provided instant success, not only throughout the A-10 CTK, but also the Maintenance Group. The men and women began to see and believe that CPI could work within the organization and that their voices would be heard. A second-order effect was the teamwork between the active duty and reservist crews. This event allowed each side to begin breaking down the organizational differences between them and start to work together as a cohesive team. In addition, the actual savings of the 5S event were phenomenal:
Curent State | Future State | Difference | |
Usable storage space | 5505 sq. ft. | 6825 sq. ft. | 20% recapitalization |
Usuable inside work space | 1440 sq. ft. | 2160 sq. ft. | 50% recapitalization |
Distance to aircraft parts | 300 ft. | 70 ft. | 300% saving |
Personnel involved in supply pallets moves | 5 | 1 | 4 personnel reduction |
Keeping the Effort Going
Sustaining CPI is naturally tough, but in a war zone, it is especially difficult. However, it can be done. In this case, senior leadership knew that conducting events were just the beginning; the tough part was going to be sustaining the improvement initiatives due to constant personnel turnover. To sustain these events, senior leadership ensured that resources were bought in immediately and progress was monitored daily during production and staff meetings. Additionally, as leadership throughout the organization turned over, CPI projects were reviewed and discussed.
Achieving Further Victories
An effective strategic plan and an easy win proved to the men and women of this remote base in Afghanistan that CPI could be incorporated in any of their processes to improve effectiveness and increase efficiency. After the initial victory, the Maintenance Group continued to work on the strategic plan by outlining events that aligned to the organization’s objectives. Accomplishing each of the events eventually led to many other successes, such as: establishing local maintenance governing instructions; increasing aircraft availability; reducing maintenance downtime; and educating CPI processes and practices for the total force integration, to include Air Force active, reserve and guard components.