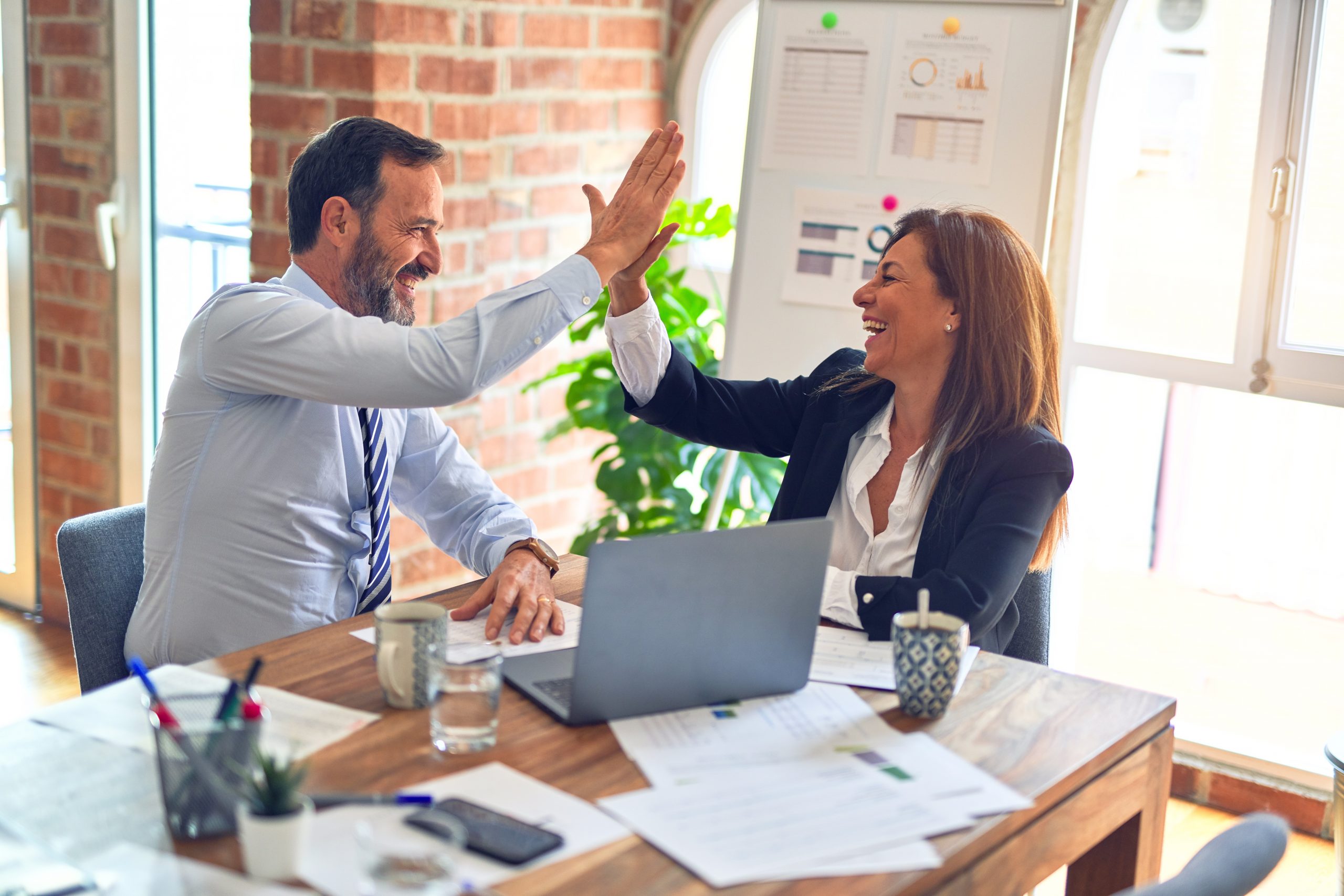
Virtua Health System has applied Six Sigma, change acceleration process and Work-out across its four-hospital system in New Jersey since 2000. Recently, as the institution was co-sponsoring and serving as a training ground for a Lean seminar, it was adding Lean to its process improvement toolkit.
About Summit Surgical Center
The Summit Surgical Center is a for-profit, licensed freestanding ambulatory surgical center on the campus of Virtua West Jersey Hospital in Voorhees, New Jersey, USA.
Outpatient surgery (also called same-day surgery) is performed in the modern facility, which has seven operating suites and two procedure rooms.
Approved by the Accreditation Association for Ambulatory Healthcare, the Summit serves patients of all ages, from children to the elderly. It performed 9,899 procedures during 2005.
The seminar featured five Kaizen events. A Kaizen event is an intense, non-traditional meeting focusing on action and speed. It uses the concept of “try-storming” (an action-oriented version of brainstorming) where new ideas are tried in the process and then observed leading to improvements. While many other healthcare organizations benefited from the seminar, the Summit Surgical Center, a jointly owned partnership between Virtua Health and physicians, saw some direct improvements.
Three weeks before the Kaizen event which was to affect the surgical center, two experts from the Lean seminar co-sponsor visited Summit for four days of observation, data collection, spaghetti mapping and communications with members of the center’s staff. Lean was explained as a way to make their jobs easier. Since the staff needed to be in training or involved in the Kaizen the whole week, arrangements were made to cover their regular duties.
Learning About Lean
First the staff learned that the goal of Lean is to create flow and eliminate waste (or muda as the Japanese creators of Lean would say) so that work serves the customer’s needs and adds value to the process. Eight types of waste can be found in healthcare – defects, overproduction, transportation, waiting, inventory or resources, motion, over-processing and underutilization.
The first step in Lean is to define value by obtaining the voice of the customer, the staff was told. Second, it is important to develop a value stream map (VSM) of the process, which illustrates and labels each step as value-added or non-value-added. The VSM shows how value flows to the customer and defines relationships among key process points. It documents the current state and provides groundwork for developing a future state – making waste clearly visible.
The third step is to establish flow by “spaghetti” mapping product, services and information movements through the process or “value stream” (see figure below). The ultimate goal of continuous flow is achieved by continuously adding value that leads to a reliable and flexible process.

The fourth step is to implement “pull” or “just-in-time.” The customer at the end of the process signals the need for a product or transaction. Only then does the process start and only the amount of time needed is taken. TAKT equals the total available working time divided by the total customer demand.
The fifth phase is to work to perfection. The Lean project team strives to eliminate all waste so that every activity creates value bringing the process closer to perfection.
Summit Surgical Center’s Kaizen Event
Based on the pre-event work, the surgical center Kaizen event had a dual focus – addressing issues in the sterile store room in the operating room and improving the purchase order and accounts payable process. The Lean opportunities for improvement in the surgical center were outlined as:
- Improved visual management of the supply process.
- Streamlined workflow for the supply ordering, distribution and payable processes.
- Enhanced point of use storage and synchronized consumption based replenishment systems for supplies.
- Standardized process for ordering supplies.
The Kaizen event began on a Monday afternoon with a process walk through and worksite observations. The group then compared notes and brainstormed ideas for improvement. By the end of the day the group split into two teams – one to apply more traditional physical Kaizen methodology to eliminate the congestion in the central sterile supply room and the second team to apply transactional methodology to improve the purchase order through accounts payable processes.
Translating Ideas into Action
During the second day the teams began translating the ideas into action. The central sterile team focused on finding a way to change the rolling racks to stationary shelves. In order to lock the rolling racks in fixed position with enough aisle space between them for walkways, at least one rack would need to be removed from the room. This led to the first action step in the central sterile room to assure that the staff was only storing what was needed for case cart preparation.
One major accomplishment was removing the pain management supplies from the room and creating two standardized pain management carts. Meanwhile, the transactional team used the SIPOC model (supplier, input, process, output and customer) to define the flow of the purchase order through accounts payable process. The flow was illustrated on a wall, with a self-stick note labeling each step. Transactional processes involved 23 inputs with 13 input methods during 25 process steps that took 10 days to accomplish the 98 minutes of actual work. Day 2 concluded with a report of the accomplishments, challenges and next steps to all staff and the project sponsors.
The third day was filled with significant challenges. The central sterile team had already removed one set of racks when they made two major findings – there was not a sub-floor beneath the racks and, more importantly, removing the set of racks they had focused on would not create enough space to have clear walkways in between the aisles when the racks were locked in fixed positions.
Time was another pressure-inducing element. The surgery center was in disarray with pieces of racking and inventory spread through the hallway, and before closing in one hour, this would have to be restored to working order for the morning start-up.
The team considered scrapping the idea of stationary shelves, but then looked at alternatives, including expanding the central sterile area into an adjacent area. That could not be accomplished in the Kaizen event since the space was already in use and would need walls removed and locking doors installed to meet the requirements for a sterile area.
Turning Roadblocks into Results
With renewed energy from a late-night pizza delivery, the team recommitted to the original plan of stationary shelving. Tape measures, simulated self-stick note layouts and white board sketches led the team to determine that a different, and larger rack would have to be removed to provide sufficient clearance between the fixed shelves. The original rack was re-installed and the team revisited the 5Ss (sort, set in order, shine, standardize and sustain) sorting through what was really needed in the room.
The team questioned the need for specialty supplies, such as eye surgery supplies, to be located in the central sterile room since all eye/lenses surgeries were performed in a dedicated operating room (OR). This not only created space, it also broke through the thinking that there always has to be a case cart for a surgery.
Eye supplies were moved to the point of use, OR 3. In addition to removing the need for a nurse to prepare a case cart, this eliminated duplicate touches for the same supplies, preserving sterile integrity and enhancing visual management, while improving presentation and ease of use for surgery staff. With this breakthrough, the team was unstoppable, and before the night was over it had overhauled the central sterile storage room, the suture supply area, OR 3 and emergency supplies, among others.
The transactional team succeeded in standardizing the method and locations for requesting supplies, but realized the larger impact would require more physical changes. First, however, they members had to overcome resistance to the idea of moving processes to new locations. The team assembled a business case and received permission to tryout the changes – which involved co-locating staff from a separate building five miles away.
Kaizen Challenges Resolved by Creativity
These challenges forced the teams to find creative solutions to what would seem impossible situations. When the situation seems insurmountable, the team invariably finds a way to make it work.
Day 4 focused on completing implementation of the improvements and documenting their effectiveness. The teams developed standard operating procedures, adjusted item locations, and added finishing touches such as labels and signage. With solutions in place, measures were repeated to quantify and compare the impact of the improvements.
New spaghetti maps were drawn, distances were tracked using the new process, cycle times were re-measured and inventory quantities changes were tracked. The teams were impressed with the improvement they had implemented and how changes to daily processes made their jobs easier. The table below documents the impacts they had.
Kaizen Impact Summary | ||
Before |
After |
Impact |
Order Processing | ||
11 handoffs 13 input methods |
Lean activities > Process map > Visual management > 5S > Flow |
> Reduced time on non-value-added from 62 minutes to 38 per order > Reduced number of physical handoffs to six > Reduced input methods to eight > Clear process |
Central Serile Room | ||
Major safety issues Congestion Delays Interruptions |
Lean activities > 5S > Point of use > Flow |
> Reduced time on non-value-added from 18 minutes to 0 per case > No delays or interruptions > Reduced time from 20 minutes to 2 per CSS cart |
AP Cycle Time | ||
25 process steps 10 day lead time 98 minutes work |
Lean activities > Flow |
> Reduced process steps to 17 > Reduced lead time to four days > Reduced work to 62 minutes |
The final day was reserved for report outs and a well-deserved celebration. As exhausting as the experience was, participants reported their accomplishments with pride and were ready to participate in additional events. The Summit Surgical Center staff also responded positively to the changes. Now multiple departments are vying for the next Kaizen. With this week-long event, the Lean journey had begun.